Graphene synthesis involves a variety of techniques, broadly categorized into bottom-up and top-down methods. Bottom-up methods include chemical vapor deposition (CVD), epitaxial growth, and arc discharging, which build graphene layers atom by atom. Top-down methods, such as mechanical exfoliation, chemical oxidation, and exfoliation, involve breaking down bulk graphite into graphene layers. Each technique has its advantages and limitations, with CVD being the most widely used for producing high-quality, large-area graphene films. The choice of method depends on the desired graphene quality, scalability, and application requirements.
Key Points Explained:
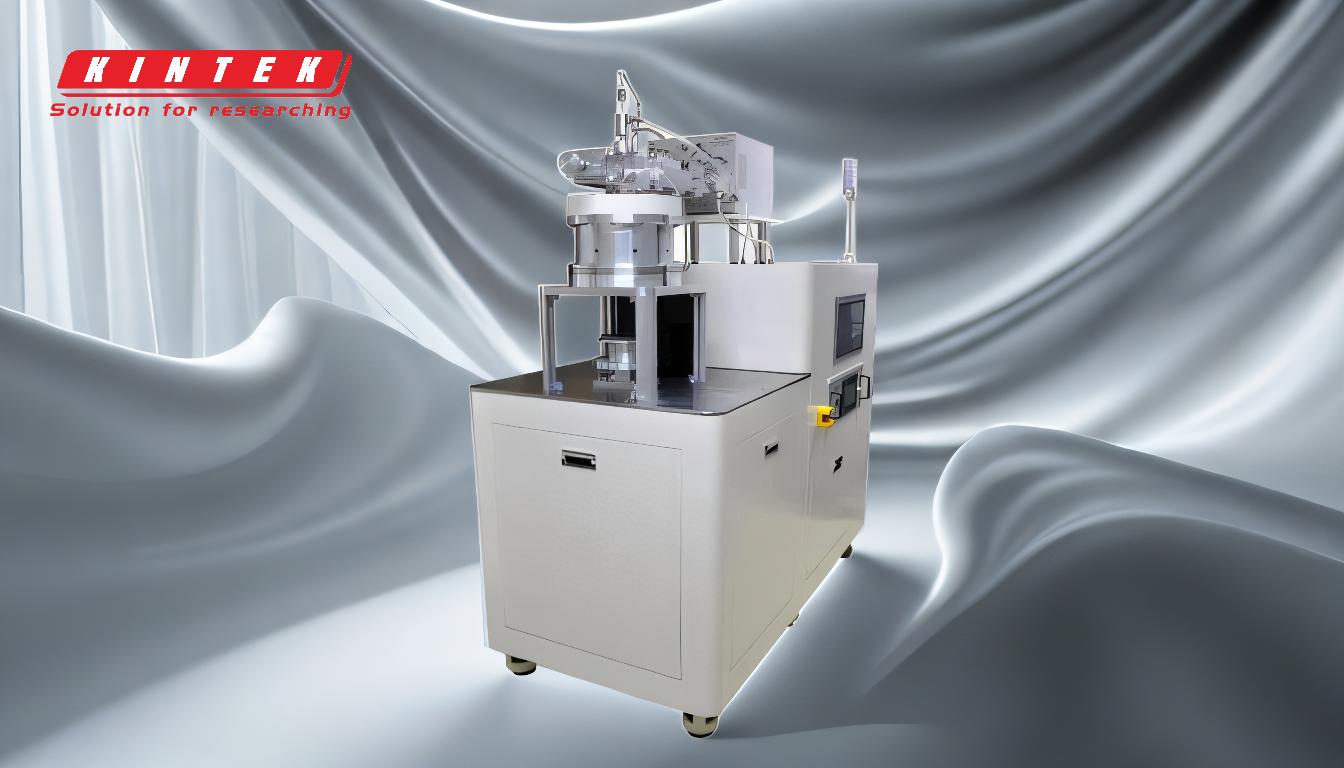
-
Bottom-Up Synthesis Methods:
-
Chemical Vapor Deposition (CVD):
- Process: CVD involves growing graphene films on substrates, typically transition metals like nickel or copper, by decomposing carbon-containing gases at high temperatures (800-1000°C). The carbon atoms then form a graphene layer on the substrate.
- Advantages: Produces high-quality, large-area graphene films suitable for electronic applications.
- Limitations: Requires high temperatures and specific substrates, which can limit scalability and increase costs.
- Substrate Modification: Annealing under a hydrogen atmosphere can promote grain growth and suppress defects, enhancing the quality of graphene.
-
Epitaxial Growth:
- Process: Graphene is grown on single-crystal silicon carbide (SiC) by heating the substrate to high temperatures, causing silicon atoms to evaporate and leaving behind a graphene layer.
- Advantages: Produces high-quality, single-crystal graphene without the need for a metal catalyst.
- Limitations: Limited by the high cost of SiC substrates and the difficulty in scaling up the process.
-
Arc Discharging:
- Process: Involves creating an electric arc between two graphite electrodes in an inert gas atmosphere, producing graphene flakes in the process.
- Advantages: Simple and cost-effective method for producing graphene in bulk.
- Limitations: Produces graphene with varying quality and requires post-processing to separate graphene from other carbon structures.
-
Chemical Vapor Deposition (CVD):
-
Top-Down Synthesis Methods:
-
Mechanical Exfoliation:
- Process: Involves peeling off graphene layers from bulk graphite using adhesive tape or other mechanical means.
- Advantages: Produces high-quality graphene with minimal defects, suitable for research purposes.
- Limitations: Not scalable for industrial production and yields small quantities of graphene.
-
Chemical Oxidation and Reduction:
- Process: Graphite is oxidized to produce graphene oxide (GO), which is then reduced to graphene using chemical or thermal methods.
- Advantages: Scalable and cost-effective method for producing graphene in large quantities.
- Limitations: The reduction process often leaves behind defects and residual oxygen groups, reducing the quality of graphene.
-
Exfoliation:
- Process: Involves breaking down graphite into graphene layers using solvents, surfactants, or mechanical forces.
- Advantages: Can produce graphene in large quantities and is relatively simple to perform.
- Limitations: The quality of graphene can vary, and the process may introduce defects or impurities.
-
Mechanical Exfoliation:
-
Comparison of Methods:
- Quality: Bottom-up methods like CVD and epitaxial growth generally produce higher-quality graphene with fewer defects compared to top-down methods.
- Scalability: Top-down methods, particularly chemical oxidation and exfoliation, are more scalable and cost-effective for industrial applications.
- Applications: CVD is preferred for electronic applications due to its ability to produce large-area, high-quality graphene, while top-down methods are more suitable for applications where cost and quantity are more critical than quality.
-
Recent Advances:
- Substrate Engineering: Modifying substrates or catalyst films, such as annealing under a hydrogen atmosphere, has been shown to improve the quality of graphene produced by CVD.
- Single-Crystal Graphene: Using single-crystal substrates or catalyst films in the CVD process helps produce single-crystal graphene, which is highly desirable for electronic applications.
In summary, the choice of graphene synthesis technique depends on the specific requirements of the application, including the desired quality, scalability, and cost. Bottom-up methods like CVD are ideal for producing high-quality graphene for electronic applications, while top-down methods are more suitable for large-scale production where cost and quantity are prioritized.
Summary Table:
Method | Process | Advantages | Limitations |
---|---|---|---|
Bottom-Up Methods | |||
CVD | Grows graphene on metal substrates via carbon gas decomposition at high temps | High-quality, large-area graphene films for electronics | High cost, limited scalability, requires specific substrates |
Epitaxial Growth | Graphene forms on SiC substrates by heating to evaporate silicon atoms | High-quality, single-crystal graphene without metal catalysts | Expensive SiC substrates, difficult to scale |
Arc Discharging | Electric arc between graphite electrodes in inert gas produces graphene flakes | Simple, cost-effective bulk production | Varying quality, requires post-processing |
Top-Down Methods | |||
Mechanical Exfoliation | Peeling graphene layers from graphite using adhesive tape | High-quality graphene with minimal defects | Not scalable, yields small quantities |
Chemical Oxidation | Graphite oxidized to graphene oxide, then reduced to graphene | Scalable, cost-effective large-scale production | Defects and residual oxygen groups reduce quality |
Exfoliation | Breaking graphite into graphene layers using solvents or mechanical forces | Large quantities, simple process | Varying quality, may introduce defects or impurities |
Need help selecting the right graphene synthesis method? Contact our experts today for tailored advice!