Steel production is a critical industrial process that relies heavily on specialized furnaces designed to handle high temperatures and large-scale operations. The three main types of furnaces used to produce steel are the Integrated Blast Furnace (BF) and Basic Oxygen Furnace (BOF), the Electric Arc Furnace (EAF), and the Direct Reduced Iron (DRI) with Electric Arc Furnaces. Each of these furnace types has unique characteristics, applications, and advantages, making them suitable for different stages and methods of steel production. Below, we explore these furnaces in detail, focusing on their operational principles, industrial applications, and relevance to steel manufacturing.
Key Points Explained:
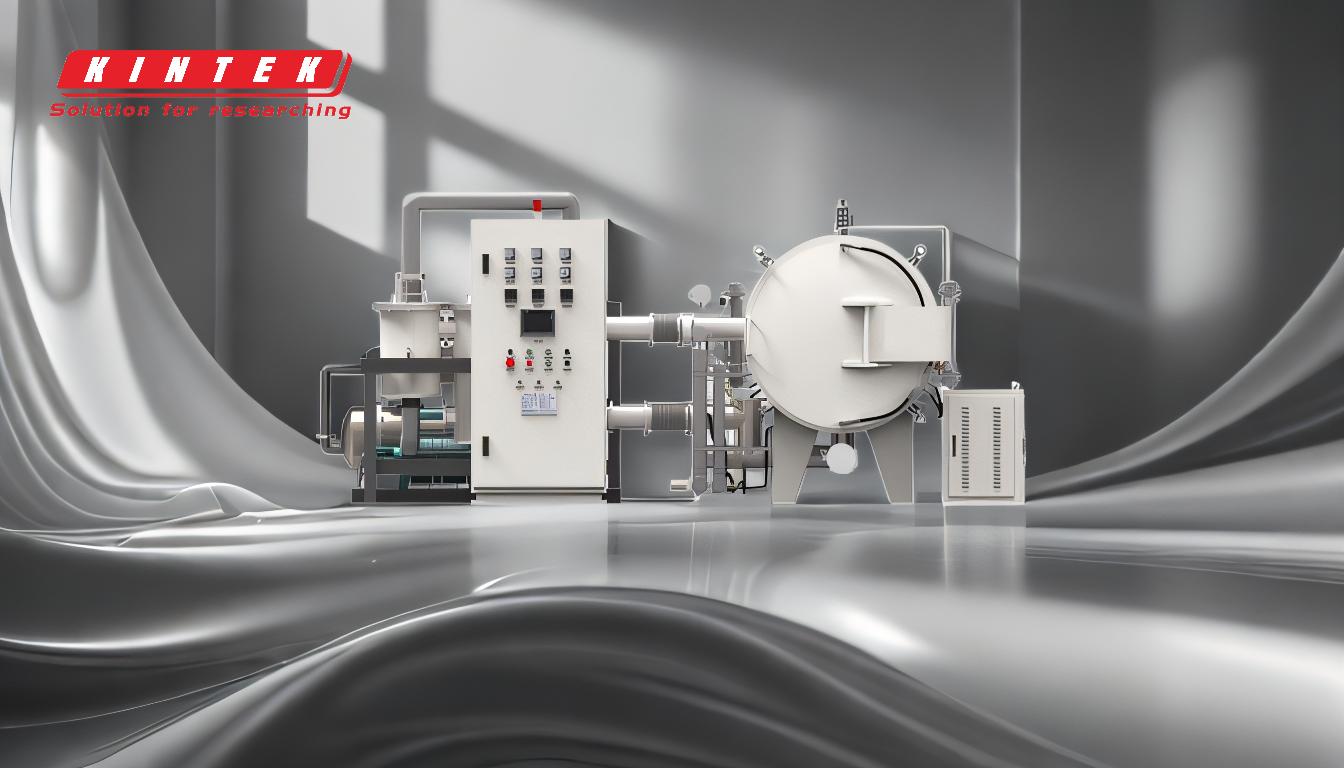
-
Integrated Blast Furnace (BF) and Basic Oxygen Furnace (BOF)
- Description: This is a two-step process involving a blast furnace and a basic oxygen furnace. The blast furnace reduces iron ore into molten iron, which is then refined in the basic oxygen furnace to produce steel.
-
Key Features:
- The blast furnace uses coke (a form of coal) as a reducing agent to extract iron from iron ore.
- The basic oxygen furnace uses oxygen to remove impurities from the molten iron, resulting in high-quality steel.
- Applications: This method is widely used in large-scale steel production, particularly for producing carbon steel. It is ideal for integrated steel plants that handle raw materials like iron ore and coal.
- Advantages: High production capacity, efficient for large-scale operations, and produces high-quality steel.
- Disadvantages: High capital and operational costs, significant environmental impact due to carbon emissions.
-
Electric Arc Furnace (EAF)
- Description: The EAF uses electric arcs to melt scrap steel or other raw materials. It is a more flexible and environmentally friendly alternative to the BF-BOF method.
-
Key Features:
- Generates heat through an electric arc between electrodes and the scrap metal.
- Can operate with 100% scrap metal, making it highly sustainable.
- Applications: Commonly used in mini-mills and for producing specialty steels, such as stainless steel and alloy steels.
- Advantages: Lower capital and operational costs, reduced environmental impact, and flexibility in raw material usage.
- Disadvantages: Limited to scrap-based production, which may not always be available in sufficient quantities.
-
Direct Reduced Iron (DRI) with Electric Arc Furnaces
- Description: This method involves producing direct reduced iron (DRI) from iron ore using natural gas or coal, which is then melted in an electric arc furnace to produce steel.
-
Key Features:
- DRI is produced by reducing iron ore without melting it, using a reducing gas derived from natural gas or coal.
- The DRI is then fed into an electric arc furnace for further processing.
- Applications: Suitable for regions with abundant natural gas resources and limited access to scrap metal.
- Advantages: Lower carbon emissions compared to the BF-BOF method, flexibility in raw material usage, and efficient for smaller-scale operations.
- Disadvantages: Higher energy consumption compared to traditional EAF methods and dependency on natural gas availability.
Summary of Key Differences:
Furnace Type | Primary Raw Materials | Energy Source | Environmental Impact | Production Scale |
---|---|---|---|---|
BF-BOF | Iron ore, coke | Coal, oxygen | High carbon emissions | Large-scale |
EAF | Scrap steel | Electricity | Lower emissions | Medium to large |
DRI with EAF | Iron ore, natural gas | Natural gas, electricity | Moderate emissions | Small to medium |
Conclusion:
The choice of furnace for steel production depends on factors such as the availability of raw materials, production scale, environmental considerations, and cost. The BF-BOF method is ideal for large-scale, integrated steel plants, while the EAF offers flexibility and sustainability for scrap-based production. The DRI with EAF method bridges the gap by providing a lower-emission alternative for regions with abundant natural gas. Understanding these furnace types is crucial for equipment and consumable purchasers to make informed decisions based on their specific operational needs and goals.
Summary Table:
Furnace Type | Primary Raw Materials | Energy Source | Environmental Impact | Production Scale |
---|---|---|---|---|
BF-BOF | Iron ore, coke | Coal, oxygen | High carbon emissions | Large-scale |
EAF | Scrap steel | Electricity | Lower emissions | Medium to large |
DRI with EAF | Iron ore, natural gas | Natural gas, electricity | Moderate emissions | Small to medium |
Need help choosing the right furnace for your steel production? Contact our experts today for personalized advice!