Brazing is a metal-joining process that offers distinct advantages over other methods, particularly in precision and material integrity. The primary benefits of brazing include the ability to join metals without melting the base materials, which ensures precise control over tolerances and minimizes distortion. This makes brazing ideal for high-precision applications where maintaining the structural integrity of the parent metals is critical. Additionally, brazing uses a filler metal to create strong, durable joints, making it suitable for complex assemblies and dissimilar materials. These advantages make brazing a preferred choice in industries requiring high-quality, reliable joints.
Key Points Explained:
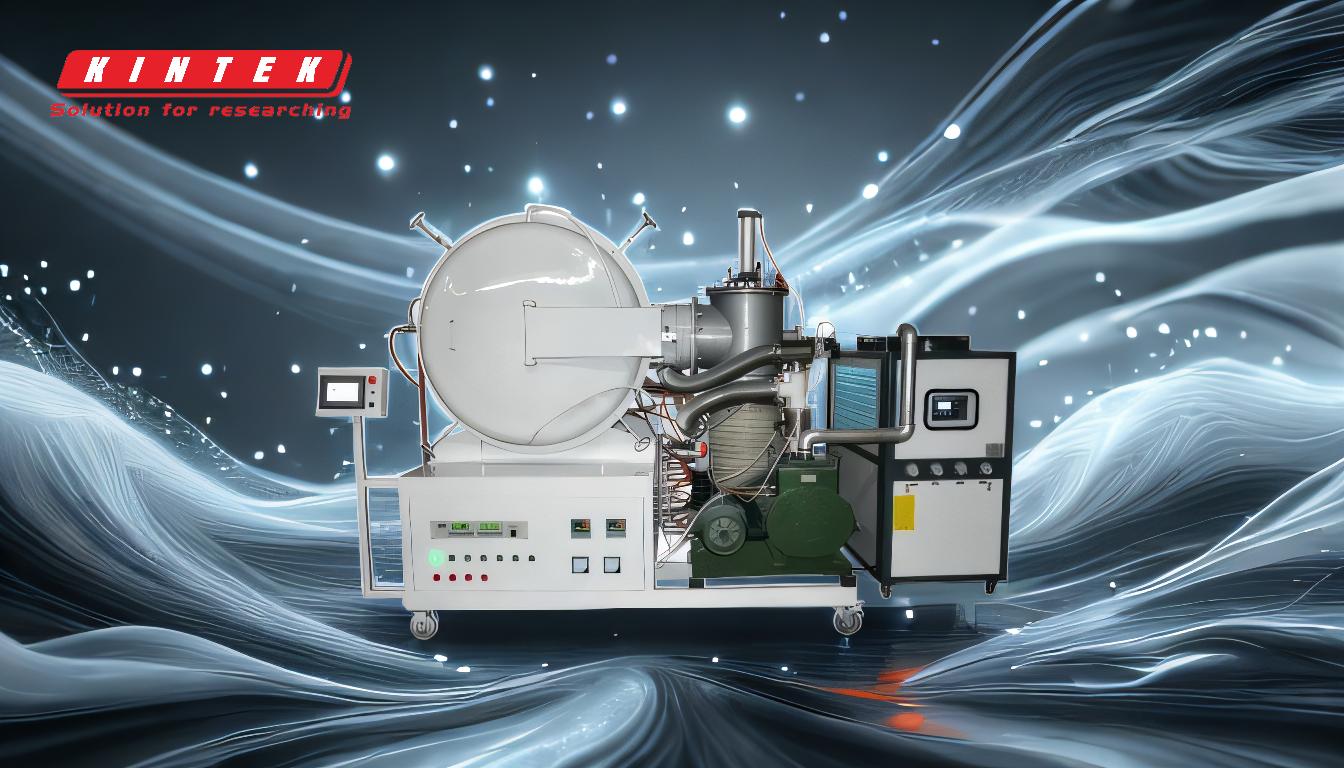
-
Preservation of Parent Metal Integrity
- Explanation: Brazing does not melt the base metals being joined. Instead, it uses a filler metal with a lower melting point to create the bond. This ensures that the parent metals retain their original properties, such as strength and hardness, without being weakened by the joining process.
- Impact: This is particularly beneficial in applications where the structural integrity of the base materials is critical, such as in aerospace or automotive components.
- Example: Joining thin or delicate materials without risking warping or melting.
-
Precise Control of Tolerances and Minimal Distortion
- Explanation: Since the base metals are not melted, brazing allows for tighter control over dimensional tolerances. This precision is crucial in applications where even minor distortions can affect performance or assembly.
- Impact: This advantage makes brazing suitable for high-precision industries, such as electronics or medical device manufacturing, where components must fit together perfectly.
- Example: Assembling intricate parts in electronic circuits or creating leak-proof joints in refrigeration systems.
-
Versatility in Joining Dissimilar Materials
- Explanation: Brazing can effectively join dissimilar metals and even nonmetals, which is often challenging with other joining methods like welding. The filler metal used in brazing can bond materials with different thermal expansion rates or melting points.
- Impact: This versatility expands the range of applications for brazing, making it a cost-effective solution for complex assemblies.
- Example: Joining copper pipes to steel fittings in HVAC systems or bonding ceramics to metals in advanced manufacturing.
-
Reduced Thermal Distortion
- Explanation: Compared to welding, brazing operates at lower temperatures, which reduces the risk of thermal distortion or warping in the joined parts. This is especially important for thin or heat-sensitive materials.
- Impact: Lower thermal stress means less post-processing is required to correct distortions, saving time and resources.
- Example: Joining thin sheets of metal in the production of heat exchangers or radiators.
-
Suitability for High-Volume Production
- Explanation: Brazing is a scalable process that can be automated for high-volume manufacturing. Its consistency and reliability make it ideal for mass production environments.
- Impact: This scalability ensures cost-effectiveness and efficiency in industries requiring large quantities of joined components.
- Example: Automotive assembly lines producing thousands of brazed joints daily for exhaust systems or engine components.
By leveraging these advantages, brazing provides a robust, precise, and versatile solution for metal joining, making it a preferred choice across various industries.
Summary Table:
Advantage | Explanation | Impact | Example |
---|---|---|---|
Preservation of Parent Metal Integrity | Brazing uses a filler metal, not melting base metals, retaining their properties. | Critical for structural integrity in aerospace, automotive, and more. | Joining thin or delicate materials without warping. |
Precise Control of Tolerances | Base metals are not melted, ensuring tight dimensional control. | Ideal for high-precision industries like electronics and medical devices. | Assembling intricate parts in electronic circuits. |
Versatility in Joining Dissimilar Materials | Brazing bonds dissimilar metals and nonmetals effectively. | Expands applications in HVAC, advanced manufacturing, and more. | Joining copper pipes to steel fittings. |
Reduced Thermal Distortion | Lower temperatures minimize warping in heat-sensitive materials. | Reduces post-processing, saving time and resources. | Joining thin sheets in heat exchangers. |
Suitability for High-Volume Production | Scalable and automated for mass production. | Ensures cost-effectiveness and efficiency in industries like automotive. | Producing thousands of brazed joints daily in automotive assembly lines. |
Unlock the full potential of brazing for your projects—contact our experts today to learn more!