Brazing is a widely used joining process in various industries, and the choice of joint type is critical for ensuring strong, reliable, and leak-proof connections. The two most common types of joints used in brazing are lap joints and butt joints. Lap joints involve overlapping the edges of the materials to be joined, providing a larger surface area for the brazing filler metal to bond. Butt joints, on the other hand, involve aligning the edges of the materials end-to-end, which is simpler but requires precise alignment and preparation. Both joint types have their specific applications, advantages, and limitations, depending on the materials, design requirements, and intended use of the brazed assembly.
Key Points Explained:
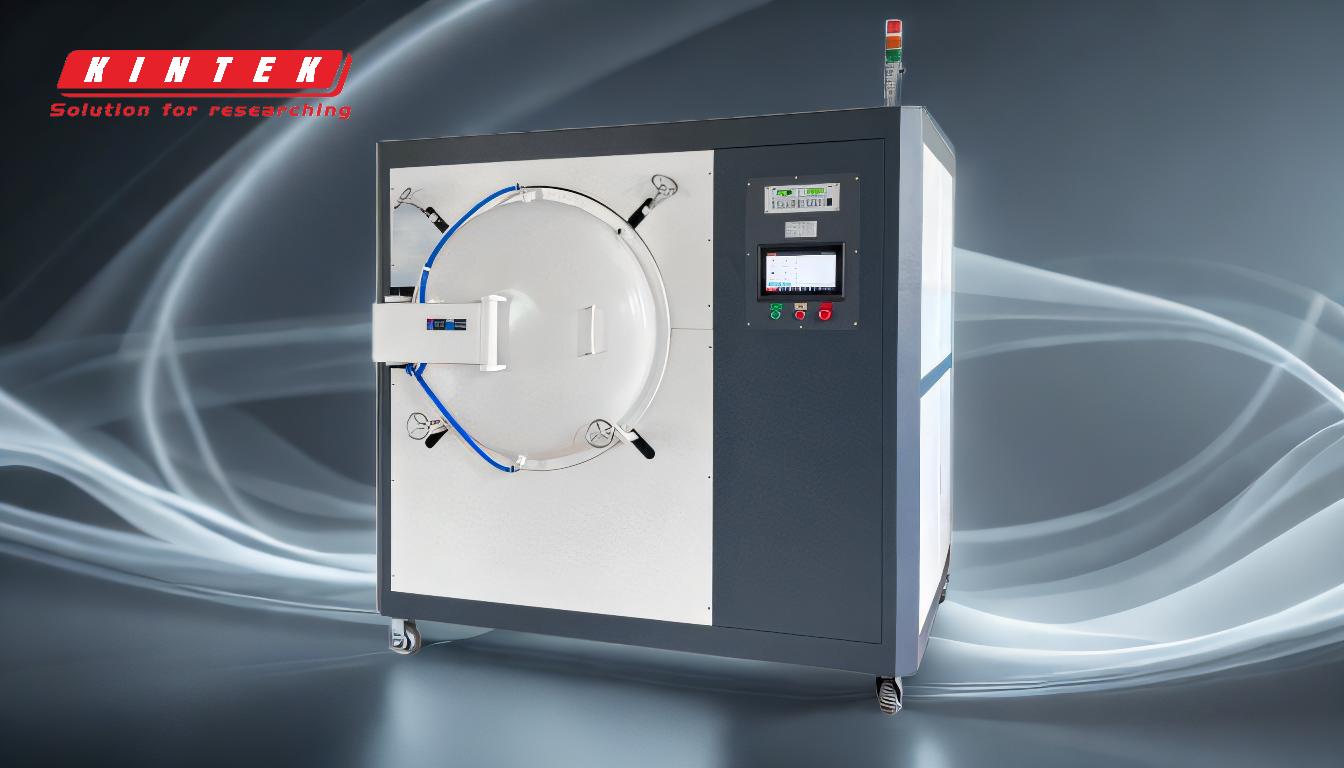
-
Lap Joints:
- Definition: Lap joints are created by overlapping the edges of the materials to be joined. The overlapping area provides a larger surface for the brazing filler metal to flow and bond, resulting in a strong and durable connection.
-
Advantages:
- Increased surface area for bonding, which enhances joint strength.
- Suitable for thin materials or when a high-strength joint is required.
- Can accommodate slight misalignments due to the overlapping design.
-
Applications:
- Commonly used in sheet metal fabrication, HVAC systems, and automotive components.
- Ideal for joining dissimilar materials with different thermal expansion rates.
-
Limitations:
- Requires precise control of overlap length to avoid excessive material usage.
- May not be suitable for applications where space constraints are critical.
-
Butt Joints:
- Definition: Butt joints involve aligning the edges of the materials end-to-end without overlapping. The joint is formed by filling the gap between the edges with brazing filler metal.
-
Advantages:
- Simple and straightforward design, making it easier to prepare and assemble.
- Suitable for applications where a flush surface is required.
- Works well for joining materials of similar thickness.
-
Applications:
- Widely used in plumbing, piping, and structural assemblies.
- Ideal for applications where joint appearance and smoothness are important.
-
Limitations:
- Requires precise alignment and preparation of the edges to ensure a strong bond.
- Smaller bonding area compared to lap joints, which may limit joint strength in some cases.
-
Factors Influencing Joint Selection:
- Material Compatibility: The choice of joint type depends on the materials being joined. For example, lap joints are often preferred for dissimilar materials, while butt joints are suitable for similar materials.
- Design Requirements: The intended use of the brazed assembly, such as load-bearing capacity, thermal cycling, or corrosion resistance, influences the choice of joint type.
- Space Constraints: Lap joints require more space due to the overlapping design, whereas butt joints are more compact and suitable for tight spaces.
- Cost and Efficiency: Butt joints are generally faster and more cost-effective to prepare, while lap joints may require additional material and preparation time.
-
Best Practices for Brazing Joints:
- Surface Preparation: Proper cleaning and surface preparation are essential for both lap and butt joints to ensure good wetting and bonding of the brazing filler metal.
- Joint Clearance: Maintaining the correct joint clearance (typically 0.001 to 0.005 inches) is critical for achieving a strong and uniform bond.
- Filler Metal Selection: Choosing the appropriate brazing filler metal based on the materials and joint type is crucial for optimal performance.
- Heating and Cooling Control: Controlled heating and cooling cycles are necessary to prevent thermal stresses and ensure a reliable joint.
By understanding the characteristics, advantages, and limitations of lap and butt joints, engineers and technicians can make informed decisions when designing and executing brazing processes. The choice of joint type ultimately depends on the specific requirements of the application, including material properties, design constraints, and performance expectations.
Summary Table:
Aspect | Lap Joints | Butt Joints |
---|---|---|
Definition | Overlapping edges for larger bonding area | Aligned edges end-to-end with filler metal in the gap |
Advantages | - Increased surface area for stronger bonds - Suitable for thin materials |
- Simple design - Flush surface - Ideal for similar thickness materials |
Applications | Sheet metal, HVAC, automotive, dissimilar materials | Plumbing, piping, structural assemblies, smooth appearance |
Limitations | - Requires precise overlap control - Not ideal for tight spaces |
- Requires precise alignment - Smaller bonding area |
Need help choosing the right brazing joint for your project? Contact our experts today for personalized advice!