Chemical Vapor Deposition (CVD) coatings are versatile and widely used in high-performance applications due to their durability, environmental friendliness, and ability to produce fine-grained, impervious, and high-purity materials. The types of CVD coatings vary based on the materials used and the specific processes employed. These coatings can range from soft, ductile materials to hard, ceramic-like substances, with thicknesses from a few microns to over 200 mm. Common materials include silicon compounds, carbon, organofluorines, and nitrides like titanium nitride. Additionally, CVD technology enables the production of coatings based on titanium, zirconium, or chromium in the form of nitrides, carbides, and carbonitrides, as well as high-quality aluminum oxide films. The process involves high temperatures and often requires post-coating treatments to restore material hardness.
Key Points Explained:
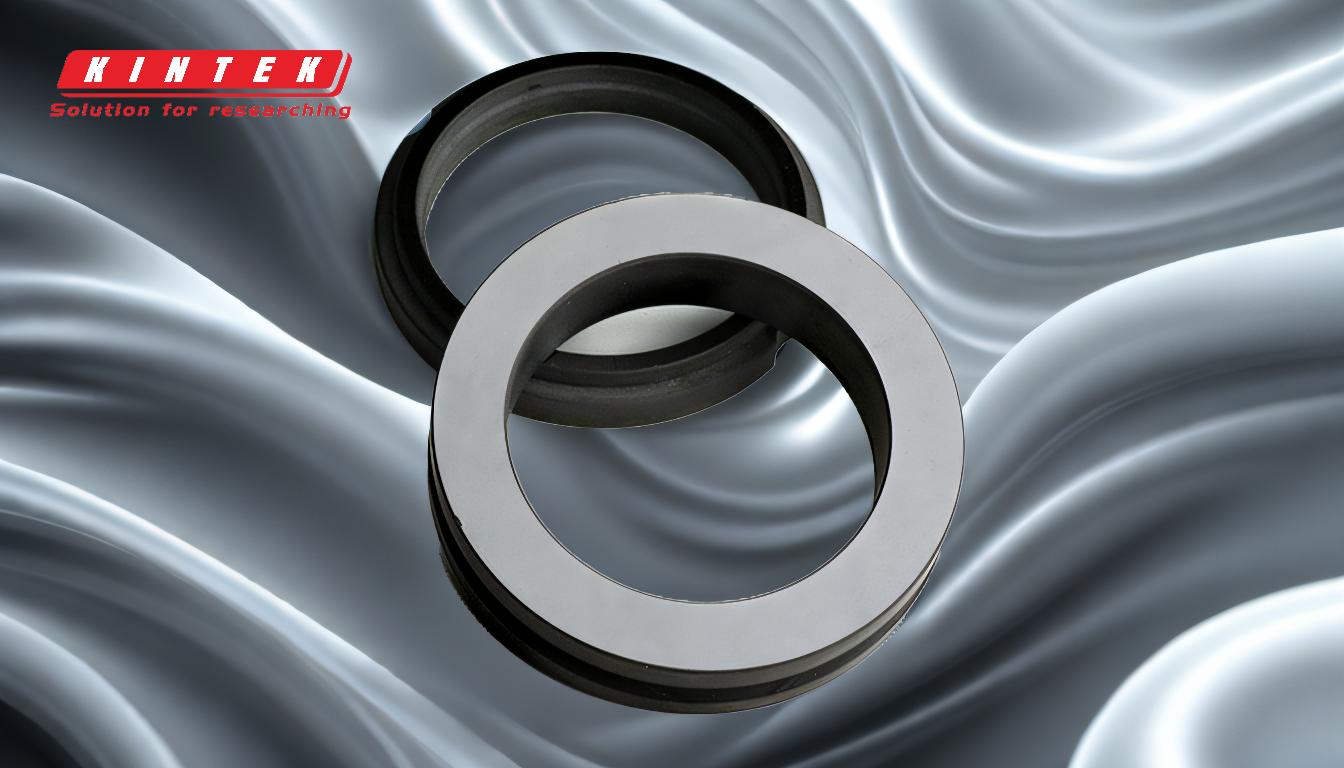
-
Types of Materials Used in CVD Coatings:
- Silicon Compounds: These are commonly used in CVD coatings for their durability and resistance to high temperatures.
- Carbon-Based Coatings: These include diamond-like carbon (DLC) coatings, which are known for their hardness and low friction properties.
- Organofluorines or Fluorocarbons: These coatings provide excellent chemical resistance and are often used in applications requiring inert surfaces.
- Nitrides (e.g., Titanium Nitride): These coatings are known for their hardness and wear resistance, making them ideal for cutting tools and wear components.
-
Properties of CVD Coatings:
- Hardness: CVD coatings can range from 150 to 3000 HV (0.1 Kg), making them suitable for both soft and hard applications.
- Thickness: Coating thickness can vary from a few microns to over 200 mm, depending on the application requirements.
- Purity and Imperviousness: CVD coatings are fine-grained, impervious, and of high purity, which is difficult to achieve with conventional ceramic fabrication processes.
-
CVD Coating Processes:
- Atomic Layer Deposition (ALD): A subset of CVD, ALD allows for precise control over coating thickness at the atomic level, making it ideal for applications requiring ultra-thin, uniform coatings.
- Plasma Enhanced Chemical Vapor Deposition (PECVD): This process uses plasma to enhance the chemical reactions, allowing for lower deposition temperatures and faster coating rates.
-
Applications of CVD Coatings:
- Machine Tools: CVD coatings are used to enhance the durability and performance of cutting tools and other machine components.
- Analytical Flow Path Components: These coatings are used in analytical instruments to ensure chemical resistance and reduce contamination.
- Wear Components: CVD coatings are applied to components that experience high wear to extend their lifespan.
- Instrumentation: The high purity and durability of CVD coatings make them suitable for use in sensitive instrumentation.
-
Post-Coating Treatments:
- Vacuum Heat Treatment: After CVD coating, tools often undergo vacuum heat treatment to restore their hardness, especially when the coating process exceeds the tempering temperature of the base material.
- Surface Roughness: CVD coatings typically result in a slightly rougher surface compared to the substrate, which may require additional finishing processes depending on the application.
-
Advantages of CVD Coatings:
- Durability: CVD coatings are known for their long-lasting performance in harsh environments.
- Environmental Friendliness: The CVD process is relatively clean and produces minimal waste compared to other coating methods.
- Versatility: The ability to deposit a wide range of materials and achieve various properties makes CVD coatings suitable for diverse applications.
In summary, CVD coatings are a critical technology in modern manufacturing and engineering, offering a wide range of materials and properties to meet the demands of high-performance applications. The choice of coating material and process depends on the specific requirements of the application, including hardness, thickness, and environmental resistance.
Summary Table:
Aspect | Details |
---|---|
Types of Materials | Silicon compounds, carbon-based coatings, organofluorines, nitrides |
Properties | Hardness (150-3000 HV), thickness (few microns to 200 mm), high purity |
Processes | Atomic Layer Deposition (ALD), Plasma Enhanced CVD (PECVD) |
Applications | Machine tools, analytical flow path components, wear components, instrumentation |
Post-Coating Treatments | Vacuum heat treatment, surface roughness adjustment |
Advantages | Durability, environmental friendliness, versatility |
Ready to enhance your applications with CVD coatings? Contact our experts today to find the perfect solution for your needs!