Brazing is a joining process that uses heat to melt a filler metal, which then flows into the joint between two or more closely fitted materials. The choice of heat source is critical to the success of the brazing process, as it affects the quality, efficiency, and application suitability of the joint. Three commonly used heat sources for brazing are torch brazing, furnace brazing, and induction brazing. Each method has its unique advantages, making it suitable for specific applications and materials.
Key Points Explained:
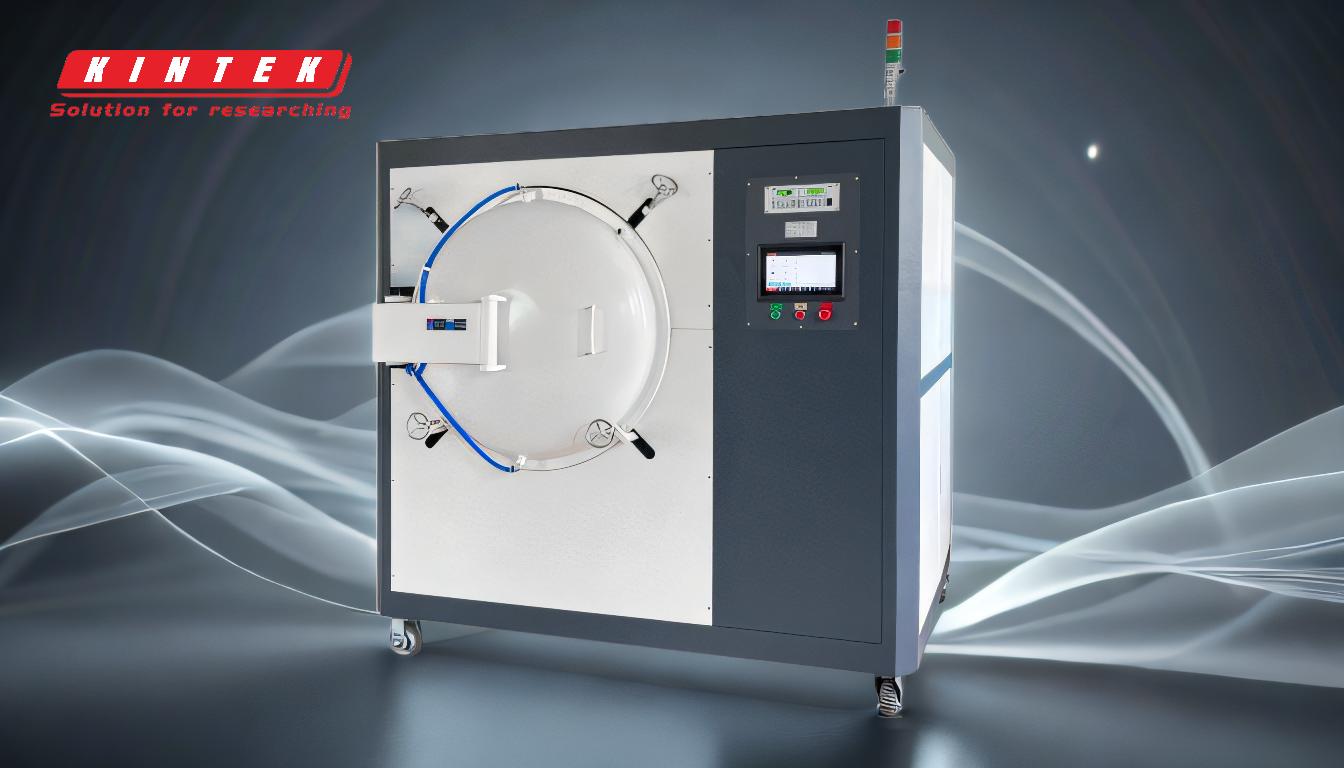
-
Torch Brazing:
- Description: Torch brazing involves using a gas-fueled torch to apply localized heat to the joint area. The torch can be manually operated or automated, depending on the application.
-
Advantages:
- Portability: Torch brazing is highly portable, making it ideal for on-site repairs or small-scale operations.
- Flexibility: It can be used on a wide range of materials and joint configurations.
- Cost-Effectiveness: Requires minimal equipment and setup, making it cost-effective for small batches or custom jobs.
- Applications: Commonly used in HVAC systems, plumbing, and automotive repairs.
-
Furnace Brazing:
- Description: Furnace brazing involves heating the entire assembly in a furnace, which can be controlled to provide a uniform temperature. Furnaces can operate in various atmospheres, including exothermic, hydrogen, argon, and vacuum, to prevent oxidation and contamination.
-
Advantages:
- Uniform Heating: Ensures even heat distribution, which is crucial for complex or large assemblies.
- High Volume Production: Suitable for mass production due to its ability to handle multiple parts simultaneously.
- Controlled Atmosphere: Reduces oxidation and improves joint quality.
- Applications: Widely used in aerospace, automotive, and electronics industries for components like heat exchangers, sensors, and electrical contacts.
-
Induction Brazing:
- Description: Induction brazing uses electromagnetic induction to generate heat directly within the workpiece. An induction coil creates a high-frequency alternating magnetic field, which induces eddy currents in the conductive materials, heating them rapidly.
-
Advantages:
- Precision: Provides precise and localized heating, minimizing heat-affected zones.
- Speed: Rapid heating cycles increase production efficiency.
- Energy Efficiency: Direct heating of the workpiece reduces energy loss.
- Applications: Ideal for high-precision applications such as medical devices, jewelry, and small electronic components.
These three heat sources—torch brazing, furnace brazing, and induction brazing—are widely used in various industries due to their unique capabilities. The choice of heat source depends on factors such as the materials being joined, the complexity of the assembly, production volume, and specific application requirements. Understanding these methods helps in selecting the most appropriate brazing technique for optimal results.
Summary Table:
Heat Source | Advantages | Applications |
---|---|---|
Torch Brazing | Portable, flexible, cost-effective | HVAC systems, plumbing, automotive repairs |
Furnace Brazing | Uniform heating, high volume production, controlled atmosphere | Aerospace, automotive, electronics (heat exchangers, sensors, electrical contacts) |
Induction Brazing | Precision, speed, energy efficiency | Medical devices, jewelry, small electronic components |
Need help choosing the right brazing method for your project? Contact our experts today!