Arcing in a vacuum occurs when electrons are emitted from the surfaces of metal electrodes in a vacuum environment. This emission can be triggered by two primary mechanisms: thermionic emission, which is caused by heating the electrode, and field electron emission, which occurs when an electric field of sufficient strength is applied. These processes lead to the creation of a vacuum arc, which is a discharge of electricity across the gap between the electrodes, even in the absence of a gaseous medium. Understanding these mechanisms is crucial for designing and operating vacuum-based electrical systems, such as vacuum interrupters or vacuum tubes, to prevent unwanted arcing and ensure reliable performance.
Key Points Explained:
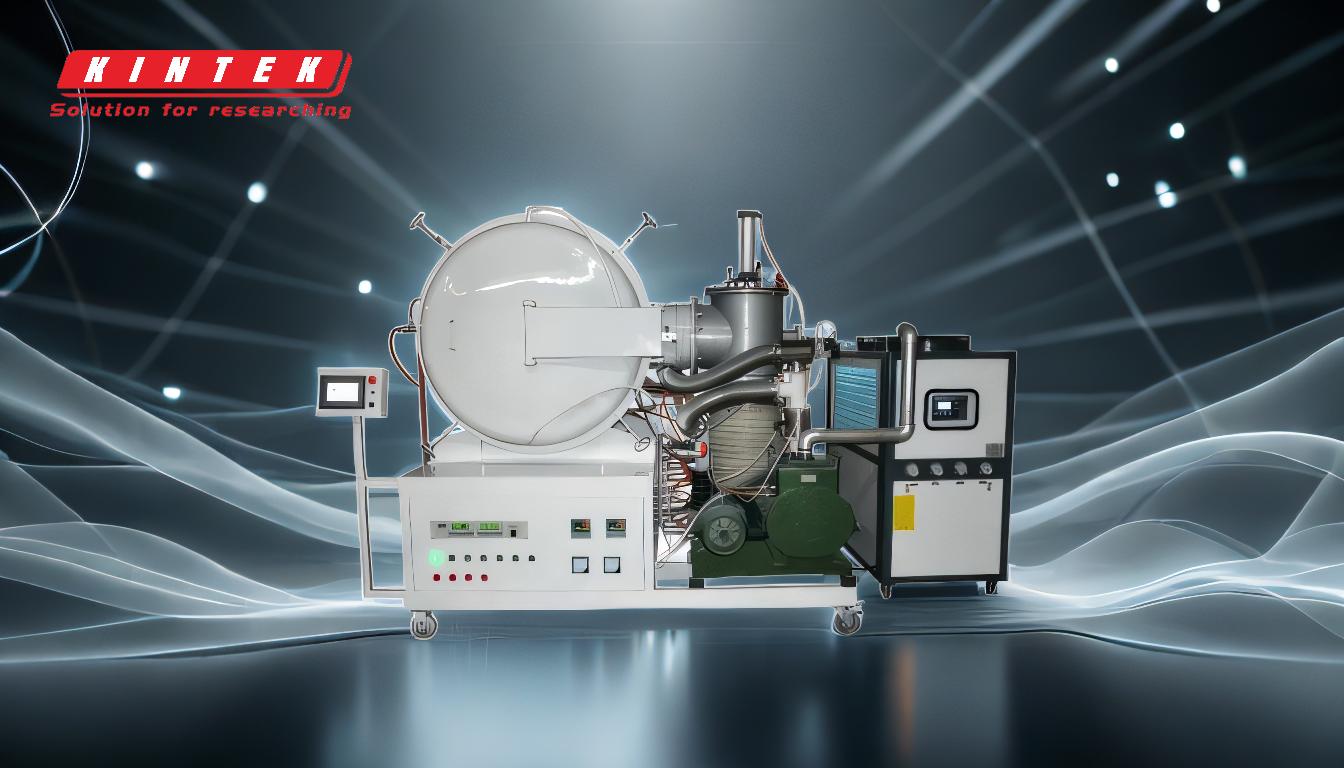
-
Thermionic Emission:
- Mechanism: Thermionic emission occurs when a metal electrode is heated to a high temperature, causing electrons to gain enough thermal energy to overcome the work function of the material and escape from the surface.
- Role in Arcing: In a vacuum, if the electrode temperature rises sufficiently, thermionic emission can lead to a significant electron flow between the electrodes. This electron flow can initiate and sustain a vacuum arc, especially if the electrodes are close enough or the voltage is high enough to maintain the discharge.
- Applications and Implications: Thermionic emission is a critical factor in devices like vacuum tubes and cathode-ray tubes, where controlled electron emission is desired. However, in systems like vacuum interrupters, uncontrolled thermionic emission can lead to arcing and failure.
-
Field Electron Emission:
- Mechanism: Field electron emission, also known as Fowler-Nordheim tunneling, occurs when a strong electric field is applied to a metal surface, reducing the potential barrier at the surface and allowing electrons to tunnel through it into the vacuum.
- Role in Arcing: In a vacuum, if the electric field strength exceeds a certain threshold, field electron emission can cause a rapid release of electrons from the cathode. This electron emission can lead to the formation of a vacuum arc, particularly if the gap between the electrodes is small or the voltage is high.
- Applications and Implications: Field emission is utilized in devices like field emission displays and electron microscopes. However, in high-voltage vacuum systems, it can cause unwanted arcing, leading to equipment damage or failure.
-
Vacuum Environment:
- Importance of Vacuum: In a vacuum, the absence of gas molecules means that traditional gas-based ionization processes (like those in air or other gases) cannot occur. Instead, arcing relies solely on electron emission from the electrode surfaces.
- Challenges: The lack of gas molecules also means that once an arc is initiated, it can be more difficult to extinguish, as there is no medium to deionize or cool the arc. This makes vacuum arcs particularly challenging to manage in high-voltage applications.
-
Electrode Material and Surface Conditions:
- Material Properties: The work function of the electrode material plays a significant role in both thermionic and field electron emission. Materials with lower work functions are more prone to electron emission, making them more susceptible to arcing.
- Surface Roughness and Contaminants: Surface imperfections or contaminants can enhance local electric fields, promoting field electron emission. Similarly, surface roughness can increase the effective surface area, enhancing thermionic emission.
-
Preventing Vacuum Arcing:
- Electrode Design: Designing electrodes with materials that have higher work functions and smoother surfaces can reduce the likelihood of both thermionic and field electron emission.
- Temperature Control: In systems where thermionic emission is a concern, controlling the temperature of the electrodes can help prevent unwanted electron emission.
- Electric Field Management: Ensuring that the electric field strength remains below the threshold for field electron emission is crucial. This can be achieved through careful design of the electrode geometry and spacing.
By understanding these key points, engineers and equipment purchasers can make informed decisions about the design, operation, and maintenance of vacuum-based electrical systems to minimize the risk of arcing and ensure reliable performance.
Summary Table:
Mechanism | Description | Role in Arcing | Applications/Implications |
---|---|---|---|
Thermionic Emission | Electrons escape due to heat overcoming the work function. | Initiates and sustains vacuum arcs under high temperature or voltage. | Used in vacuum tubes; uncontrolled emission can cause arcing in vacuum interrupters. |
Field Electron Emission | Electrons tunnel through a reduced potential barrier under a strong electric field. | Rapid electron release leads to vacuum arcs, especially at high voltages or small gaps. | Utilized in field emission displays; can cause unwanted arcing in high-voltage systems. |
Vacuum Environment | Absence of gas molecules means arcing relies solely on electron emission. | Arcs are harder to extinguish due to lack of deionization or cooling medium. | Critical for vacuum-based systems like vacuum interrupters and tubes. |
Electrode Material | Lower work function materials are more prone to electron emission. | Surface roughness and contaminants enhance emission, increasing arcing risk. | Material selection and surface quality are key to preventing arcing. |
Prevention Strategies | Use higher work function materials, control temperature, and manage electric fields. | Reduces likelihood of both thermionic and field electron emission. | Ensures reliable performance in vacuum-based electrical systems. |
Need help preventing vacuum arcing in your systems? Contact our experts today for tailored solutions!