To achieve a good brazing process, several critical factors must be considered, including the choice of heating method, temperature control, base-metal cleanliness, joint design, and filler metal properties. Efficient heat transfer, proper alloying, and wetting action are essential for ensuring strong and durable brazed joints. Additionally, the geometry of the joint, cleanliness of surfaces, and precise mechanical processing play significant roles in achieving high-quality results. Below, we break down these considerations into actionable key points.
Key Points Explained:
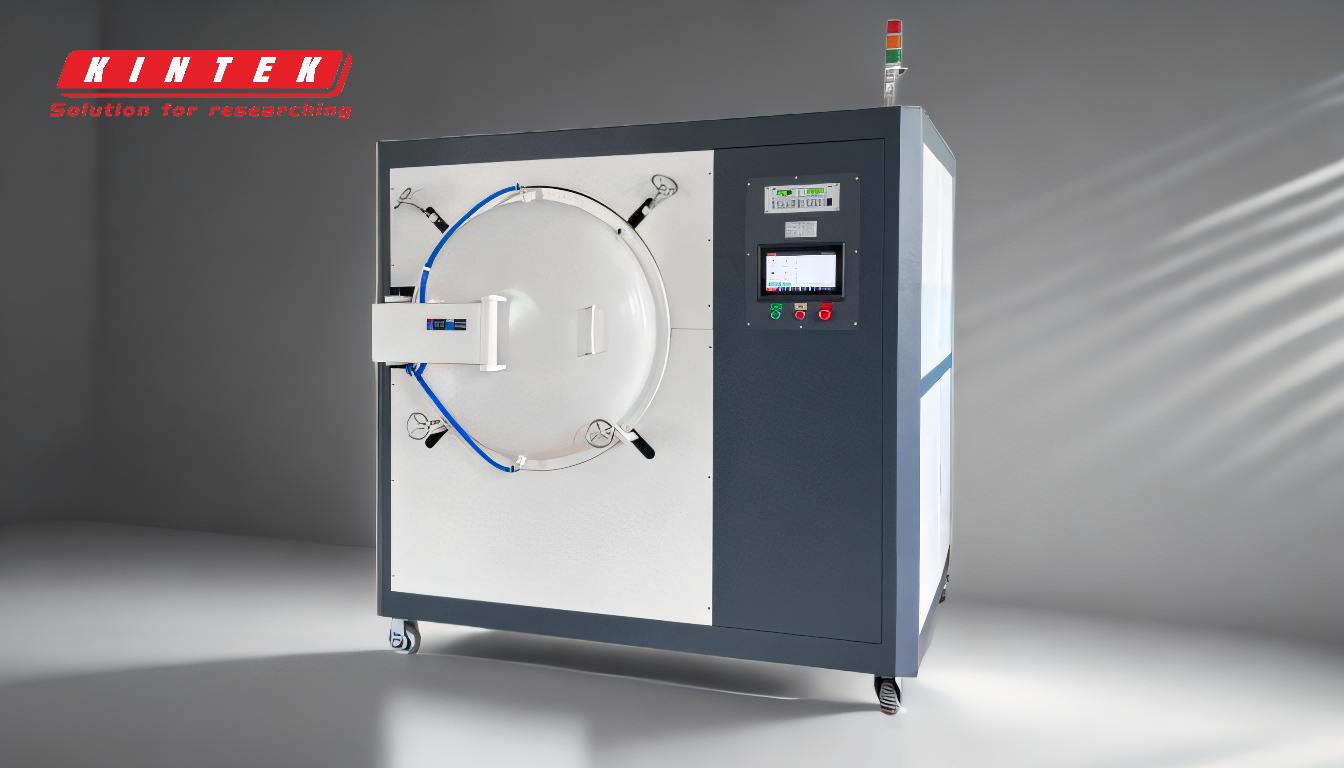
-
Heating Method Selection
- The heating method must ensure efficient heat transfer throughout the joint to achieve uniform heating and cooling.
- It should stay within the heat capacity of the base metals to avoid distortion or damage.
- The geometry of the braze joint influences the choice of heating method, as complex shapes may require localized or specialized heating techniques.
- Production rate and volume requirements also dictate the heating method, with high-volume processes often favoring automated or continuous heating systems.
-
Temperature and Time Control
- The brazing temperature must exceed the melting point of the filler metal to ensure proper alloying and wetting action.
- Overheating can damage the base metals, while insufficient heat may result in incomplete bonding.
- The time spent at the brazing temperature must be carefully controlled to allow adequate wetting and spreading of the filler metal without excessive diffusion into the base metals.
-
Base-Metal Cleanliness
- Joint surfaces must be free of contaminants such as oils, greases, oxides, or dirt to ensure proper wetting and bonding.
- Cleaning methods such as degreasing, pickling, or abrasive cleaning may be necessary depending on the base metals and contaminants.
- Maintaining cleanliness during the brazing process is equally important to prevent recontamination.
-
Joint Design and Gap Dimensions
- The joint design must allow for proper capillary action, which is critical for the filler metal to flow and fill the joint cavity.
- Precise mechanical processing is required to achieve the correct gap dimensions, as gaps that are too wide or too narrow can compromise joint strength.
- The design should also consider thermal expansion and contraction to minimize stress during heating and cooling.
-
Filler Metal Properties
- The filler metal must have a melting temperature significantly lower than that of the base metals to avoid damaging them during brazing.
- It should exhibit good wettability, spreading, and bonding characteristics to form a strong joint.
- The mechanical properties of the filler metal, such as strength and corrosion resistance, must align with the application requirements.
-
Production Considerations
- The rate and volume of production influence the choice of brazing equipment and process parameters.
- High-volume production may require automated systems for consistent quality and efficiency.
- Low-volume or custom applications may benefit from manual or semi-automated processes for greater flexibility.
By addressing these factors systematically, you can ensure a robust and reliable brazing process that produces high-quality joints tailored to your specific application.
Summary Table:
Key Factor | Key Considerations |
---|---|
Heating Method Selection | - Efficient heat transfer, uniform heating, and cooling |
- Avoid distortion or damage to base metals | |
- Consider joint geometry and production volume | |
Temperature and Time Control | - Exceed filler metal melting point, avoid overheating or insufficient heat |
- Control time for proper wetting and spreading | |
Base-Metal Cleanliness | - Remove contaminants (oils, oxides, dirt) |
- Use degreasing, pickling, or abrasive cleaning | |
Joint Design and Gap Dimensions | - Ensure proper capillary action for filler metal flow |
- Precise gap dimensions and thermal expansion considerations | |
Filler Metal Properties | - Lower melting temperature than base metals |
- Good wettability, spreading, and bonding characteristics | |
Production Considerations | - Match equipment and process to production rate and volume |
Optimize your brazing process for high-quality results—contact our experts today for tailored solutions!