The resistance of a heating element is influenced by several factors, including the material properties, temperature, and design characteristics. Understanding these factors is crucial for selecting the right heating element for specific applications, ensuring efficient heat generation, and maintaining durability. Key considerations include the material's resistivity, temperature coefficient, cross-sectional area, length, and environmental conditions such as oxygen reactivity. By analyzing these factors, one can optimize the heating element's performance and longevity.
Key Points Explained:
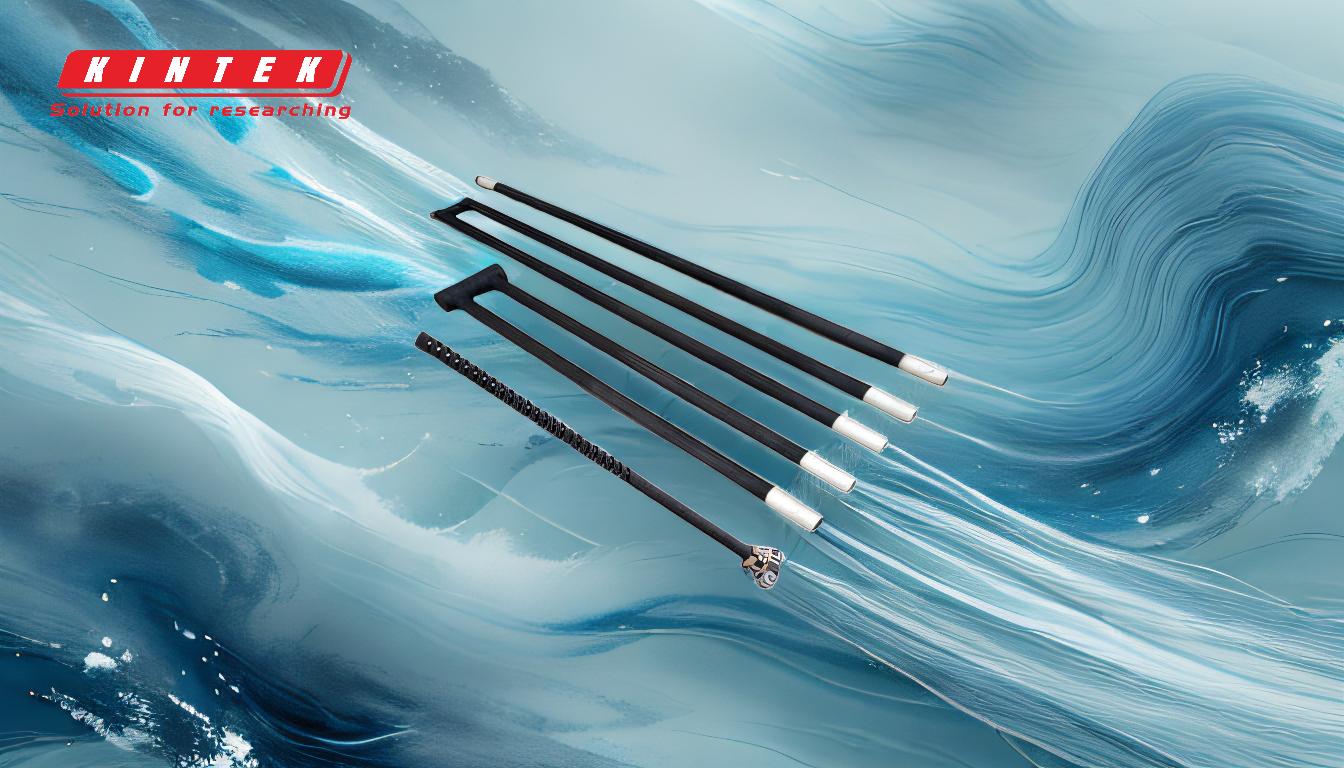
-
Material Properties:
- Resistivity: The intrinsic resistance of a material to electric current flow. Materials with higher resistivity are better suited for heating elements as they generate more heat when current passes through them.
- Temperature Coefficient: Some materials exhibit changes in resistance with temperature. For example, metals like nichrome have a positive temperature coefficient, meaning their resistance increases with temperature, which can affect performance.
- Reactivity to Oxygen: Materials must be chosen based on their ability to withstand oxidation at high temperatures. For instance, materials like Kanthal are oxidation-resistant, making them ideal for high-temperature applications in the presence of oxygen.
-
Design Characteristics:
- Cross-Sectional Area: A larger cross-sectional area reduces resistance, allowing more current to flow and generating more heat. However, this must be balanced with the desired heat output and material cost.
- Length: Longer heating elements have higher resistance, which increases heat generation. However, excessive length can lead to inefficient heat distribution.
- Geometry: The shape and configuration of the heating element (e.g., coiled, straight, or ribbon) can influence resistance and heat distribution.
-
Temperature Effects:
- Operating Temperature: As the temperature of the heating element increases, its resistance may change depending on the material's temperature coefficient. This can impact power consumption and heat output.
- Heat Dissipation: Efficient heat dissipation ensures the heating element operates within its optimal temperature range, preventing overheating and material degradation.
-
Environmental Conditions:
- Atmosphere: The presence of reactive gases like oxygen can affect the material's performance and lifespan. For example, materials like tungsten require protective atmospheres to prevent oxidation.
- Thermal Insulation: Proper insulation minimizes heat loss and ensures uniform temperature distribution, which indirectly affects resistance by maintaining stable operating conditions.
-
Electrical Parameters:
- Voltage and Current: At a constant voltage, lower resistance leads to higher current, increasing power consumption and heat generation. This relationship is governed by Ohm's Law (P = V²/R).
- Power Rating: The desired power output of the heating element influences the choice of resistance, as higher power requirements may necessitate lower resistance materials.
By carefully considering these factors, one can select or design a heating element that meets specific application requirements, ensuring efficient and reliable performance.
Summary Table:
Factor | Key Considerations |
---|---|
Material Properties | Resistivity, temperature coefficient, reactivity to oxygen (e.g., Kanthal, nichrome). |
Design Characteristics | Cross-sectional area, length, geometry (coiled, straight, or ribbon). |
Temperature Effects | Operating temperature, heat dissipation. |
Environmental Conditions | Atmosphere (oxygen reactivity), thermal insulation. |
Electrical Parameters | Voltage, current, power rating (Ohm's Law: P = V²/R). |
Need help selecting the right heating element for your application? Contact our experts today!