A brazing oven is a specialized piece of equipment used in the brazing process, which involves joining two or more metal parts using a filler metal that melts at a lower temperature than the base metals. The oven provides a controlled environment where precise temperature regulation, uniform heating, and often an inert or reducing atmosphere are maintained to ensure high-quality brazed joints. Brazing ovens are widely used in industries such as automotive, aerospace, electronics, and manufacturing, where strong, reliable, and leak-proof joints are essential. They come in various types, including batch and continuous ovens, and can be customized to meet specific application requirements.
Key Points Explained:
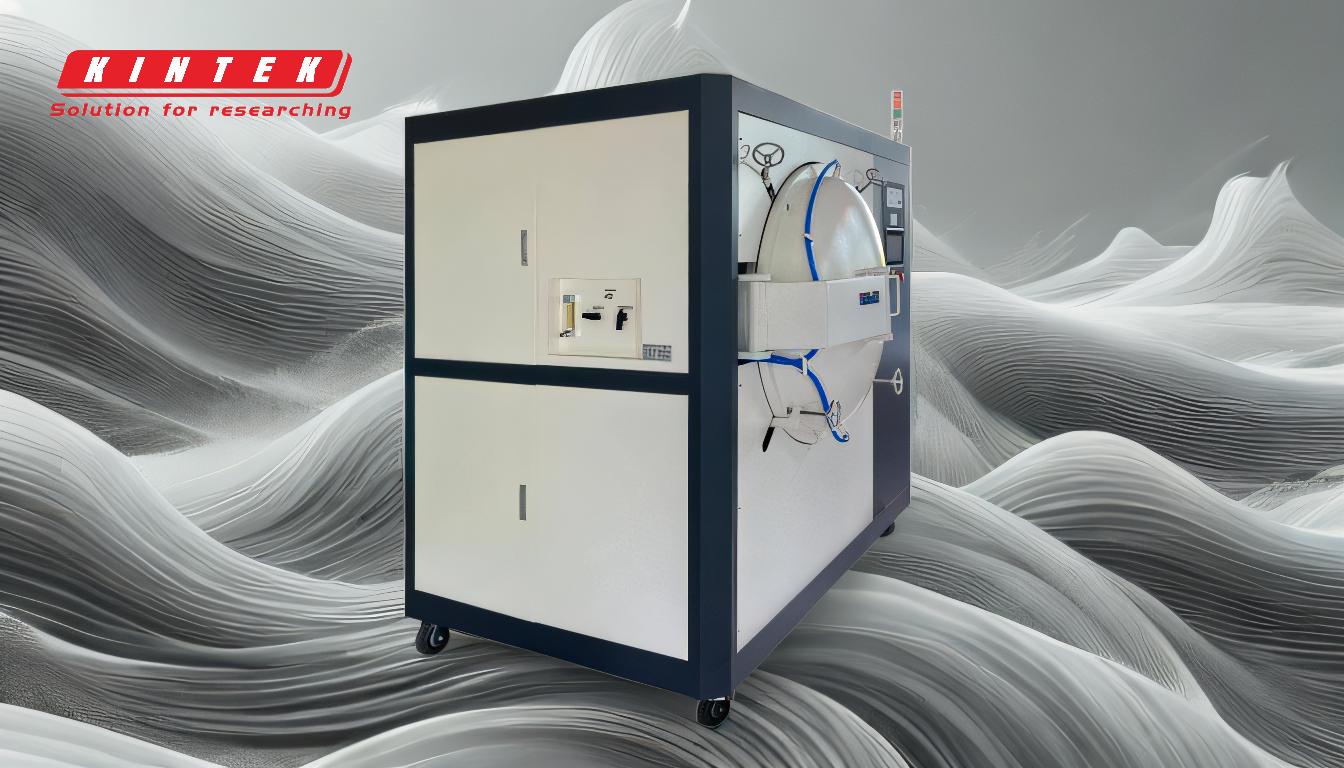
-
Definition and Purpose of a Brazing Oven
- A brazing oven is designed to facilitate the brazing process, which involves heating metal parts and a filler material to create a strong bond without melting the base metals.
- The oven ensures uniform heating, precise temperature control, and often a controlled atmosphere to prevent oxidation and contamination.
-
Key Components of a Brazing Oven
- Heating Elements: These provide the necessary heat to melt the filler metal. Common types include electric resistance heaters, gas burners, or induction coils.
- Temperature Control System: Ensures the oven maintains the exact temperature required for brazing, often with programmable settings for different materials.
- Atmosphere Control: Many brazing ovens use inert gases (e.g., nitrogen or argon) or reducing atmospheres (e.g., hydrogen) to prevent oxidation and improve joint quality.
- Insulation: High-quality insulation materials are used to retain heat and improve energy efficiency.
-
Types of Brazing Ovens
- Batch Ovens: Ideal for small to medium production runs, these ovens process parts in batches and are suitable for complex or large components.
- Continuous Ovens: Designed for high-volume production, these ovens allow parts to move through different heating zones on a conveyor system.
- Vacuum Brazing Ovens: Used for high-precision applications, these ovens operate in a vacuum to eliminate oxidation and produce exceptionally clean joints.
-
Applications of Brazing Ovens
- Automotive Industry: Used for joining components like heat exchangers, fuel injectors, and transmission parts.
- Aerospace Industry: Essential for creating strong, lightweight joints in aircraft engines and structural components.
- Electronics Manufacturing: Used for brazing components in sensors, connectors, and circuit boards.
- General Manufacturing: Applied in the production of tools, machinery, and other metal assemblies.
-
Advantages of Using a Brazing Oven
- Precision and Consistency: The controlled environment ensures uniform heating and high-quality joints.
- Versatility: Can be used with a wide range of metals and alloys, including stainless steel, aluminum, and copper.
- Efficiency: Reduces material waste and energy consumption compared to other joining methods.
- Strong Joints: Produces durable, leak-proof, and corrosion-resistant joints.
-
Considerations for Purchasing a Brazing Oven
- Capacity and Size: Choose an oven that accommodates the size and volume of your parts.
- Temperature Range: Ensure the oven can reach and maintain the temperatures required for your specific brazing process.
- Atmosphere Control: Determine if an inert or reducing atmosphere is necessary for your application.
- Energy Efficiency: Look for ovens with good insulation and energy-saving features to reduce operating costs.
- Customization Options: Some manufacturers offer tailored solutions to meet unique production needs.
-
Maintenance and Safety
- Regular maintenance, such as cleaning heating elements and checking temperature sensors, is essential to ensure optimal performance.
- Safety features like overheat protection, gas leak detectors, and emergency shut-off systems should be prioritized to prevent accidents.
By understanding the functionality, types, and applications of brazing ovens, purchasers can make informed decisions to select the right equipment for their specific needs, ensuring high-quality brazed joints and efficient production processes.
Summary Table:
Aspect | Details |
---|---|
Purpose | Joins metal parts using a filler metal without melting the base metals. |
Key Components | Heating elements, temperature control, atmosphere control, insulation. |
Types | Batch ovens, continuous ovens, vacuum brazing ovens. |
Applications | Automotive, aerospace, electronics, general manufacturing. |
Advantages | Precision, versatility, efficiency, strong and leak-proof joints. |
Considerations | Capacity, temperature range, atmosphere control, energy efficiency. |
Maintenance & Safety | Regular cleaning, safety features like overheat protection and gas detectors. |
Ready to enhance your production process with a brazing oven? Contact us today to find the perfect solution for your needs!