A burn-off furnace is a specialized type of high-temperature furnace used primarily for the removal of organic materials, such as binders, coatings, or contaminants, from metal, ceramic, or composite parts. This process is achieved by exposing the materials to high temperatures in a controlled environment, causing the organic substances to oxidize and burn off without damaging the underlying material. Burn-off furnaces are commonly used in industries such as powder metallurgy, ceramics, and metal injection molding (MIM) for processes like debinding, sintering, and cleaning. They are essential for ensuring the purity and structural integrity of materials before further processing or final use.
Key Points Explained:
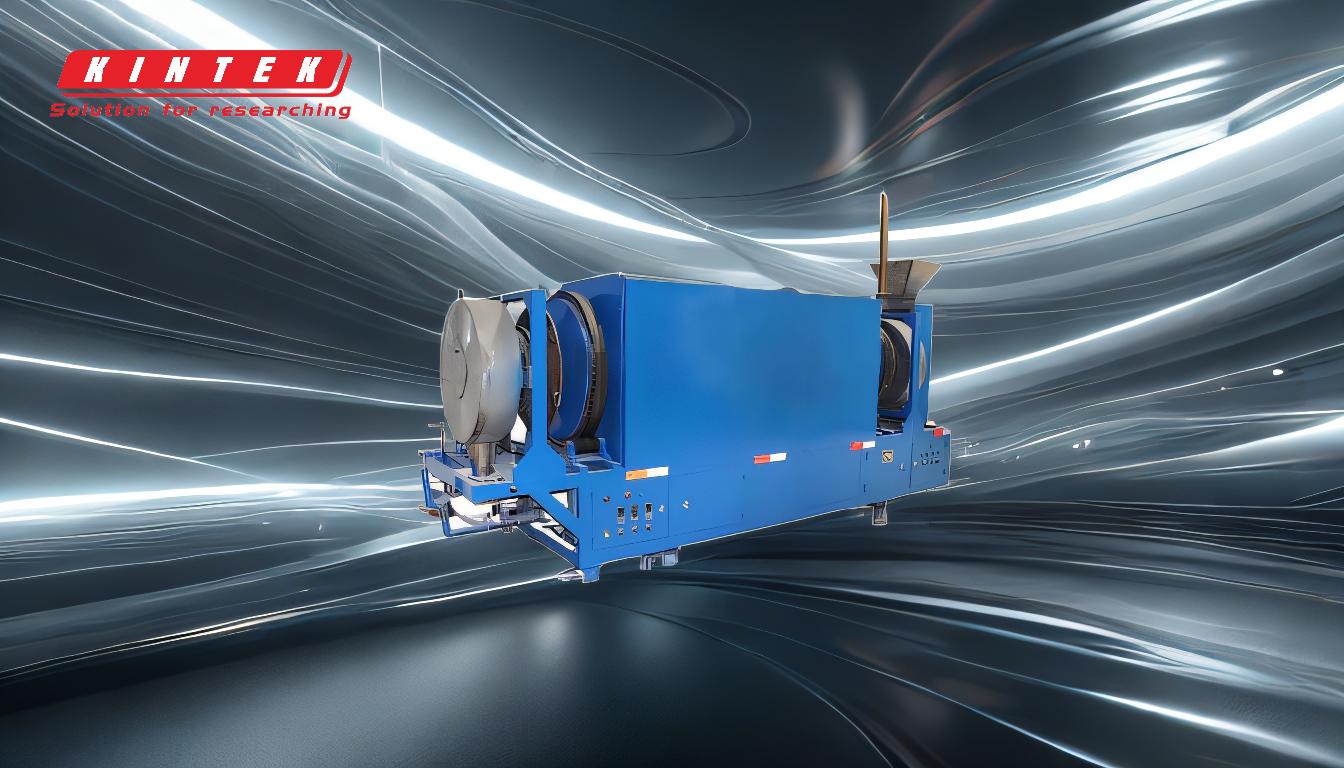
-
Definition and Purpose of a Burn-Off Furnace
- A burn-off furnace is designed to remove organic materials (e.g., binders, coatings, or contaminants) from metal, ceramic, or composite parts through high-temperature oxidation.
- The process ensures the purity and structural integrity of materials, making it a critical step in industries like powder metallurgy, ceramics, and metal injection molding (MIM).
-
Key Applications
- Debinding in Metal Injection Molding (MIM): Burn-off furnaces are used to remove polymer binders from green parts before sintering.
- Cleaning and Surface Preparation: They are used to clean metal parts by burning off oils, paints, or other organic contaminants.
- Powder Metallurgy: Burn-off furnaces help remove lubricants or binders from pressed powder compacts before sintering.
- Ceramics Processing: They are used to eliminate organic binders or coatings from ceramic components.
-
Operating Principles
- Burn-off furnaces operate at high temperatures, typically ranging from 300°C to 800°C, depending on the material and application.
- The furnace environment is carefully controlled to ensure complete oxidation of organic materials without damaging the substrate.
- Air or oxygen is often introduced to facilitate the combustion process.
-
Design Features
- Insulated Chamber: The furnace is designed with high-quality insulation to maintain consistent temperatures and improve energy efficiency.
- Temperature Control: Precise temperature control systems ensure uniform heating and prevent overheating.
- Ventilation and Exhaust Systems: These systems manage the release of gases produced during the burn-off process, ensuring safety and environmental compliance.
-
Industries and Use Cases
- Powder Metallurgy: For debinding and sintering of metal parts.
- Ceramics: For removing organic binders from ceramic components.
- Automotive and Aerospace: For cleaning and preparing metal parts for further processing.
- Research and Development: For testing and developing new materials and processes.
-
Advantages of Using a Burn-Off Furnace
- Efficiency: Quickly and effectively removes organic materials without damaging the substrate.
- Versatility: Suitable for a wide range of materials and applications.
- Precision: Controlled environments ensure consistent results.
- Environmental Safety: Proper ventilation systems minimize harmful emissions.
-
Comparison with Other Furnace Types
- Unlike sintering or annealing furnaces, which focus on altering material properties, burn-off furnaces are specifically designed for material purification.
- They operate at lower temperatures compared to melting or fusion furnaces, making them ideal for delicate processes.
-
Considerations for Purchasing
- Temperature Range: Ensure the furnace can reach the required temperatures for your specific application.
- Chamber Size: Choose a furnace with adequate capacity for your production needs.
- Control Systems: Look for advanced temperature and atmosphere control features.
- Safety Features: Ensure the furnace includes proper ventilation and exhaust systems.
By understanding these key points, purchasers can make informed decisions when selecting a burn-off furnace for their specific industrial or research needs.
Summary Table:
Aspect | Details |
---|---|
Purpose | Removes organic materials (binders, coatings, contaminants) via oxidation. |
Key Applications | Debinding (MIM), cleaning, powder metallurgy, ceramics processing. |
Temperature Range | 300°C to 800°C, depending on material and application. |
Design Features | Insulated chamber, precise temperature control, ventilation systems. |
Industries | Powder metallurgy, ceramics, automotive, aerospace, R&D. |
Advantages | Efficiency, versatility, precision, environmental safety. |
Purchasing Factors | Temperature range, chamber size, control systems, safety features. |
Ready to enhance your material processing? Contact us today to find the perfect burn-off furnace for your needs!