A cold isostatic press (CIP) is a specialized manufacturing tool used to compact powdered materials into high-density, uniform shapes by applying equal pressure from all directions. This process is achieved by immersing a flexible mold containing the powder in a pressurized liquid medium, typically water with a corrosion inhibitor. The uniform pressure ensures that the final product has consistent density and strength, making it ideal for applications requiring complex shapes, close tolerances, and high mechanical performance. CIP is widely used in industries such as powder metallurgy, refractory materials, and advanced ceramics due to its ability to produce parts with minimal internal stresses, cracks, or deformations. Additionally, it is a cost-effective method for creating high-quality components.
Key Points Explained:
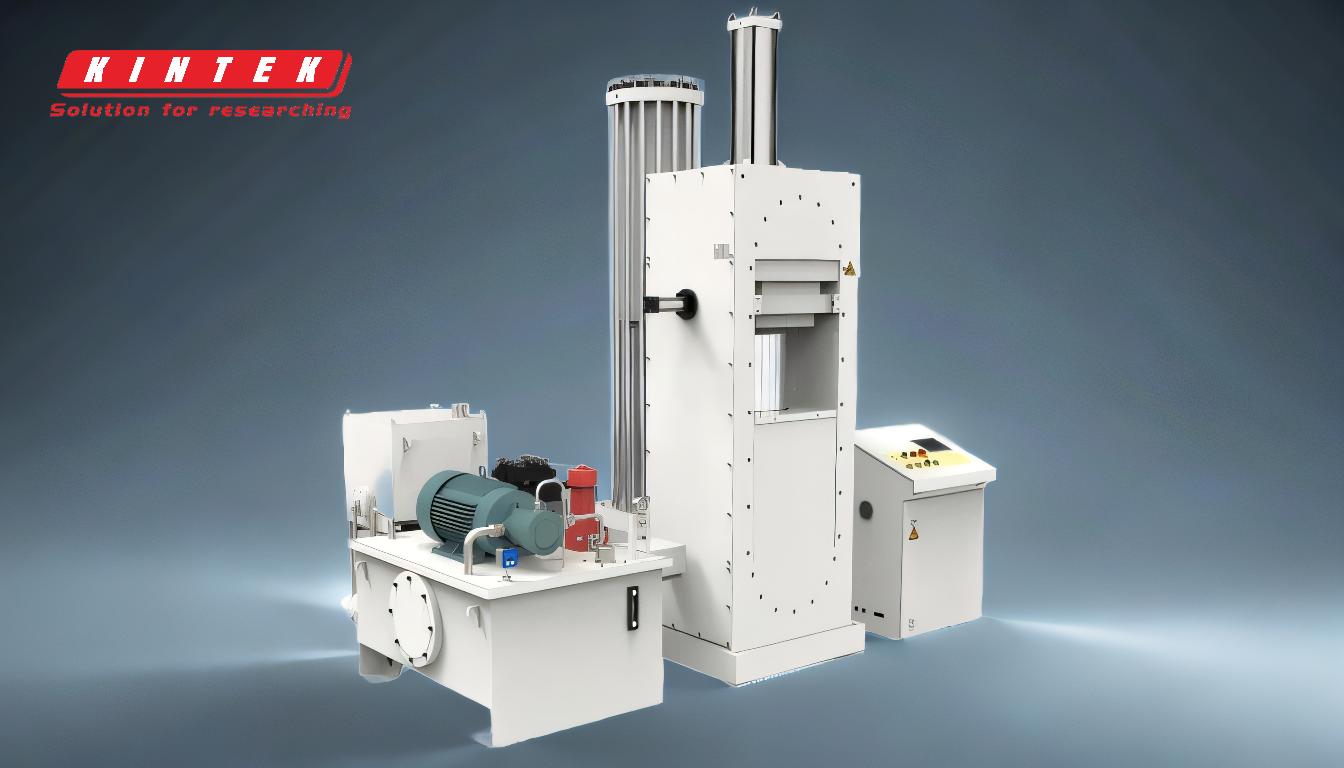
-
What is a Cold Isostatic Press (CIP)?
- A cold isostatic press is a device that uses hydrostatic pressure applied uniformly from all directions to compact powdered materials into dense, uniform shapes. The process involves placing the powder in a flexible mold, which is then immersed in a pressurized liquid medium. This method ensures uniform density and minimizes internal stresses, cracks, and deformations in the final product. For more details, see cold isostatic press.
-
How Does CIP Work?
- The CIP process involves the following steps:
- A mold (made of materials like latex, neoprene, or urethane) is filled with the powdered material.
- The mold is placed in a pressure chamber filled with a working fluid, usually water mixed with a corrosion inhibitor.
- An external pump pressurizes the fluid, applying equal pressure to the mold from all directions.
- The mold moves with the powder as it densifies, reducing friction and ensuring uniform compaction.
- The process is completed when the desired pressure and density are achieved.
- The CIP process involves the following steps:
-
Advantages of CIP:
- Uniform Density and Strength: CIP ensures that the final product has consistent density and mechanical properties throughout, reducing internal stresses and eliminating cracks or strains.
- Versatility: It can be used to produce complex shapes and achieve close tolerances, making it suitable for a wide range of materials and applications.
- Improved Mechanical Properties: The process enhances the mechanical performance of the final product, such as strength and corrosion resistance.
- Cost-Effectiveness: CIP is relatively inexpensive compared to other pressing methods, making it an attractive option for manufacturing.
-
Applications of CIP:
- CIP is widely used in industries such as:
- Powder Metallurgy: For producing high-density components from metal powders.
- Refractory Materials: For creating heat-resistant materials used in high-temperature applications.
- Advanced Ceramics: For manufacturing ceramic components with uniform density and strength.
- Isotropic Graphite and High-Melting-Point Metals: For producing materials with consistent properties in all directions.
- Artificial Bones and Medical Implants: For creating biocompatible materials with precise shapes and densities.
- Food Processing: For compacting food powders into uniform shapes.
- CIP is widely used in industries such as:
-
Comparison with Warm Isostatic Pressing (WIP):
- While CIP operates at room temperature, warm isostatic pressing (WIP) involves heating the medium or workpiece to temperatures typically below 500°C. This heating promotes additional processes like material densification, diffusion, or phase changes, while still applying uniform pressure. WIP is used when specific temperature conditions are required to achieve desired material properties.
-
Electrical vs. Manual CIP:
- Electrical CIP systems offer better pressure control compared to manual systems. This improved control ensures more precise and consistent results, making electrical CIP the preferred choice for high-precision applications.
-
Limitations of CIP:
- The size of the components produced by CIP is limited by the size of the pressure vessel. Additionally, the height-to-diameter ratio of the parts must be considered to ensure uniform compaction.
In summary, a cold isostatic press is a versatile and cost-effective tool for producing high-density, uniform components from powdered materials. Its ability to apply uniform pressure from all directions makes it ideal for applications requiring complex shapes, close tolerances, and consistent mechanical properties.
Summary Table:
Aspect | Details |
---|---|
Process | Applies uniform hydrostatic pressure from all directions using a liquid medium. |
Key Advantages | Uniform density, minimal internal stresses, versatility, cost-effectiveness. |
Applications | Powder metallurgy, refractory materials, advanced ceramics, medical implants. |
Comparison with WIP | CIP operates at room temperature; WIP involves heating below 500°C. |
Limitations | Component size limited by pressure vessel; height-to-diameter ratio matters. |
Ready to enhance your manufacturing process with a cold isostatic press? Contact us today to learn more!