A controlled atmosphere system refers to a specialized environment where the composition of gases, such as oxygen, carbon dioxide, nitrogen, and ethylene, is carefully regulated to achieve specific conditions. These systems are widely used in various applications, including storage, transportation, and industrial processes like heat treatment and material fabrication. By controlling the atmosphere, these systems prevent unwanted chemical reactions, such as oxidation or contamination, and ensure precise temperature management. This results in improved product quality, energy efficiency, and environmental safety. Controlled atmosphere systems are essential in industries requiring high precision, such as metallurgy, food preservation, and laboratory research.
Key Points Explained:
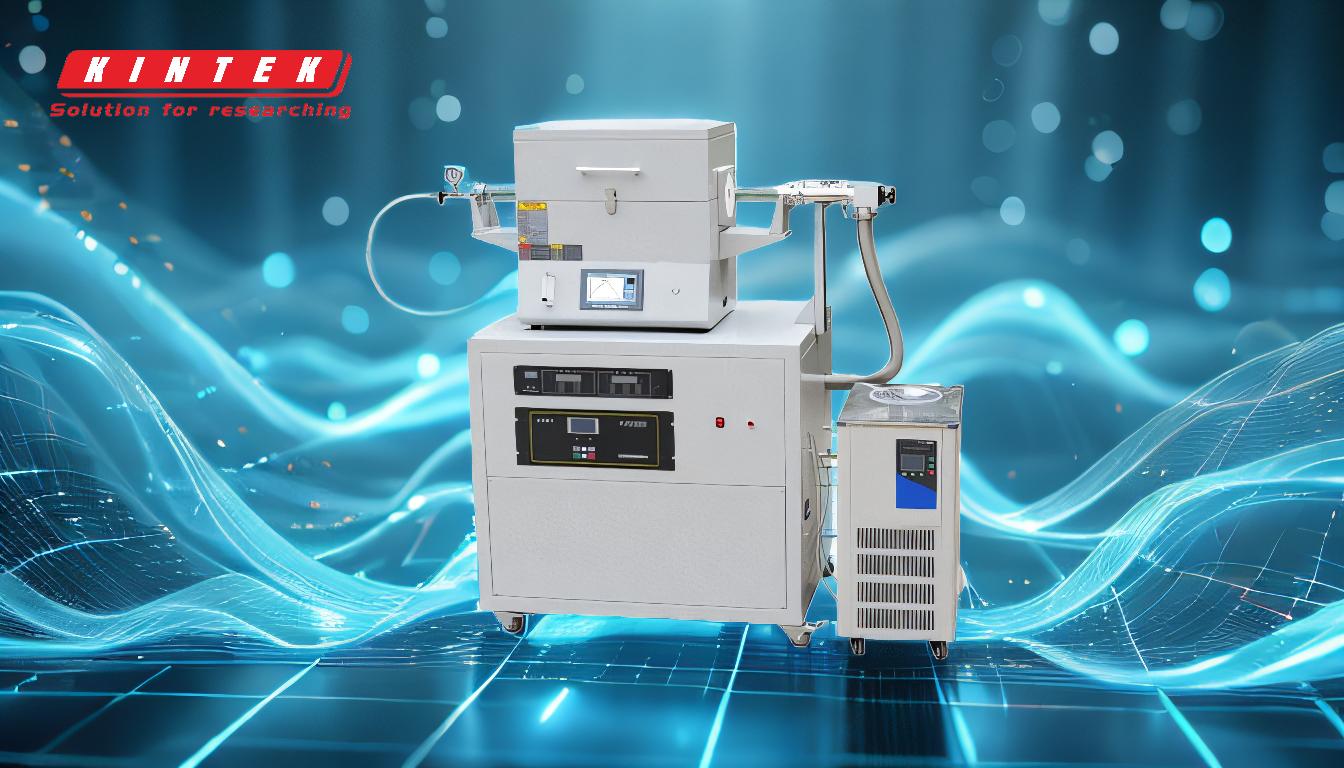
-
Definition and Purpose of Controlled Atmosphere Systems:
- Controlled atmosphere systems involve the manipulation of gas levels (e.g., oxygen, carbon dioxide, nitrogen) to create an environment tailored to specific needs.
- These systems are used to prevent surface reactions, maintain chemical inertness or reactivity, and ensure precise control over temperature and gas composition.
- Applications include storage rooms, transportation containers, laboratory furnaces, and industrial ovens.
-
Types of Controlled Atmosphere Systems:
- Controlled Atmosphere Furnaces: Used in laboratories and industrial settings for heat treatment processes like carburizing, tempering, and material fabrication. They provide precise temperature control and prevent oxidation or decarburization.
- Controlled Atmosphere Ovens: Ensure consistent heating of industrial parts, preventing reactions with air and maintaining product quality.
- Storage and Transportation Systems: Used in food preservation and other industries to extend shelf life and maintain product integrity by regulating gas levels.
-
Key Benefits:
- Improved Product Quality: By controlling the atmosphere, these systems prevent contamination, oxidation, and other surface reactions, resulting in higher-quality outputs.
- Energy Efficiency and Cost Savings: These systems optimize energy use and reduce operating costs through precise control and thermal homogeneity.
- Environmental Safety: They eliminate the need for toxic salts (e.g., cyanides) and reduce waste, making them more environmentally friendly.
- Versatility: Capable of handling parts of any shape or size, making them suitable for a wide range of applications.
-
Applications in Heat Treatment:
- Controlled atmosphere heat treatment involves heating metal parts in a regulated environment and cooling them rapidly. This alters the microstructure of the metal, enhancing properties like strength, toughness, and resistance to wear and corrosion.
- The process is critical in industries requiring high-performance materials, such as aerospace, automotive, and tool manufacturing.
-
Laboratory and Industrial Use:
- In laboratories, controlled atmosphere furnaces are used for precise material fabrication and research, ensuring chemical inertness or reactivity as needed.
- In industrial settings, these systems are essential for producing consistent, high-quality parts and preventing defects caused by uncontrolled atmospheric conditions.
-
Environmental and Operational Advantages:
- Controlled atmosphere systems reduce the risk of land contamination and simplify waste disposal by avoiding toxic byproducts.
- They provide a safer working environment by minimizing exposure to hazardous materials and ensuring consistent, reliable operation.
-
Future Trends and Innovations:
- Advances in gas regulation and temperature control technologies are making these systems more efficient and accessible.
- Increasing demand for high-quality, durable materials in industries like renewable energy and electronics is driving the adoption of controlled atmosphere systems.
In summary, controlled atmosphere systems are critical tools in modern industry and research, offering precise control over environmental conditions to achieve superior results. Their ability to enhance product quality, reduce costs, and minimize environmental impact makes them indispensable in a wide range of applications.
Summary Table:
Key Aspect | Details |
---|---|
Definition | Regulates gas composition (O₂, CO₂, N₂, etc.) for specific conditions. |
Applications | Storage, transportation, heat treatment, material fabrication. |
Types | Furnaces, ovens, storage/transportation systems. |
Benefits | Improved quality, energy efficiency, environmental safety, versatility. |
Industrial Use | Aerospace, automotive, tool manufacturing, food preservation. |
Environmental Advantages | Reduces contamination, simplifies waste disposal, safer operations. |
Future Trends | Advances in gas regulation, temperature control, and high-demand industries. |
Optimize your industrial processes with controlled atmosphere systems—contact our experts today!