A PVD (Physical Vapor Deposition) chamber is a specialized vacuum environment used to deposit thin films onto substrates through a physical process. Unlike chemical vapor deposition chamber (CVD), which relies on chemical reactions, PVD involves the physical transformation of a solid or liquid material into a vapor phase, which then condenses onto the target substrate. The process is line-of-sight, meaning the vapor travels directly from the source to the substrate. PVD chambers require high temperatures, vacuum conditions, and precise control mechanisms, including cooling systems to manage heat dissipation. This method is widely used for creating protective coatings with anti-corrosion and wear-resistant properties, making it essential in industries like semiconductors, optics, and tool manufacturing.
Key Points Explained:
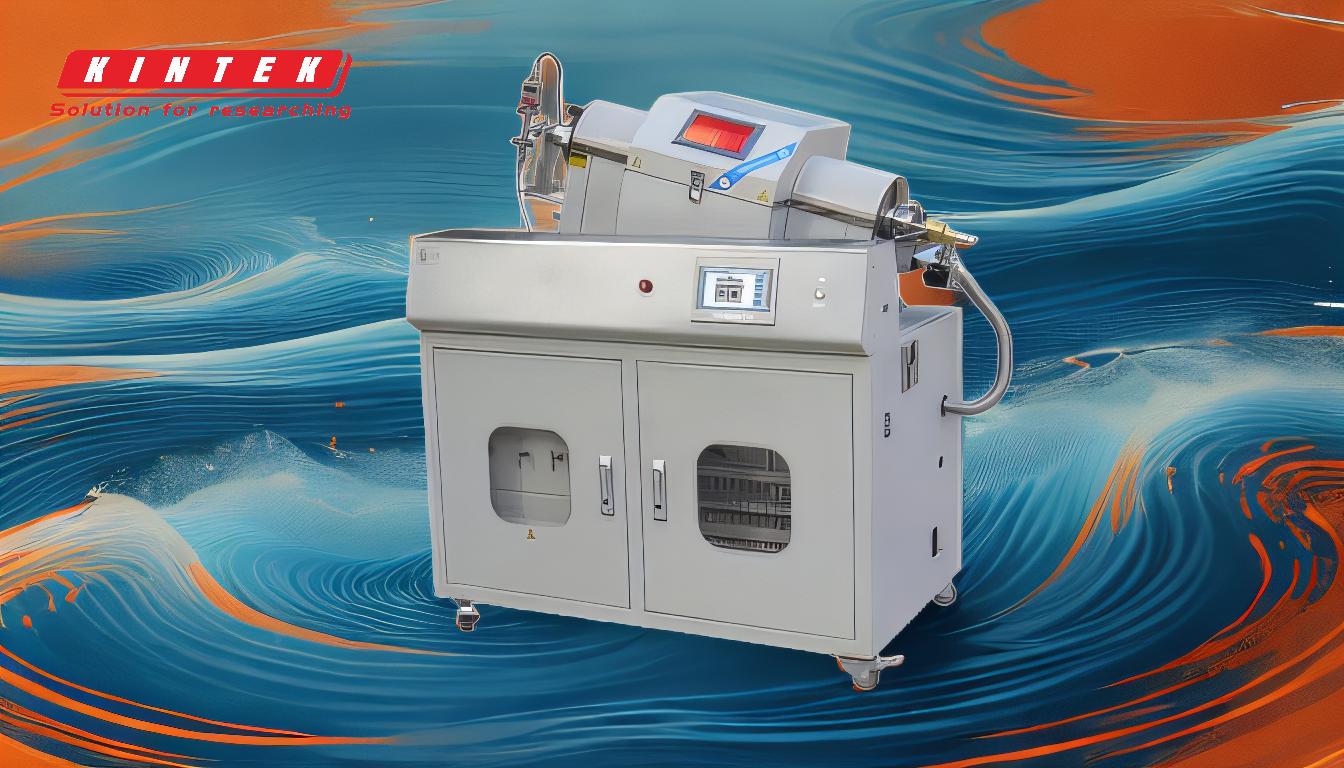
-
Definition and Purpose of a PVD Chamber
- A PVD chamber is a vacuum-sealed environment designed for the deposition of thin films using physical vapor deposition techniques.
- Its primary purpose is to create durable, high-performance coatings on substrates, such as metals, semiconductors, or tools, to enhance properties like corrosion resistance, wear resistance, and electrical conductivity.
-
How PVD Differs from CVD
- PVD is a physical process, while CVD is a chemical process.
- In PVD, material is vaporized from a solid or liquid source and deposited onto the substrate in a line-of-sight manner.
- In contrast, CVD involves chemical reactions in the vapor phase to deposit films, which can occur in multiple directions.
-
Key Components of a PVD Chamber
- Vacuum System: Maintains low pressure to ensure the vaporized material travels unimpeded to the substrate.
- Target Material: The source material (e.g., metals, alloys) that is vaporized.
- Substrate Holder: Holds the material to be coated and can be heated or cooled as needed.
- Energy Source: Provides the energy (e.g., electron beam, sputtering) to vaporize the target material.
- Cooling System: Manages heat generated during the process to maintain optimal conditions.
-
Process Steps in PVD
- Vaporization: The target material is vaporized using an energy source.
- Transport: The vaporized material travels through the vacuum chamber to the substrate.
- Condensation: The vapor condenses on the substrate, forming a thin, dense film.
- Cooling: The system cools the substrate and chamber to stabilize the deposited film.
-
Advantages of PVD
- Produces high-quality, dense films with excellent adhesion.
- Suitable for a wide range of materials, including metals, ceramics, and alloys.
- Environmentally friendly compared to some CVD processes, as it avoids toxic by-products.
-
Applications of PVD Chambers
- Semiconductors: Used to deposit thin films for microelectronics and integrated circuits.
- Optics: Creates reflective or anti-reflective coatings for lenses and mirrors.
- Tool Manufacturing: Enhances the durability and performance of cutting tools and molds.
- Decorative Coatings: Provides scratch-resistant and aesthetically pleasing finishes on consumer products.
-
Challenges and Considerations
- Requires precise control of vacuum pressure, temperature, and energy input.
- High initial cost for equipment and skilled operators.
- Limited to line-of-sight deposition, which can restrict coating uniformity on complex geometries.
-
Comparison with CVD Chambers
- PVD chambers are better suited for applications requiring high-purity films and lower deposition temperatures.
- CVD chambers excel in conformal coatings and complex geometries due to their multi-directional deposition capabilities.
By understanding the function and components of a PVD chamber, purchasers can make informed decisions about its suitability for specific applications, ensuring optimal performance and cost-effectiveness.
Summary Table:
Aspect | Details |
---|---|
Definition | A vacuum-sealed environment for depositing thin films using PVD techniques. |
Key Components | Vacuum system, target material, substrate holder, energy source, cooling. |
Process Steps | Vaporization, transport, condensation, cooling. |
Advantages | High-quality films, wide material compatibility, eco-friendly. |
Applications | Semiconductors, optics, tool manufacturing, decorative coatings. |
Challenges | Precise control required, high initial cost, line-of-sight limitations. |
Discover how a PVD chamber can elevate your manufacturing process—contact us today for expert advice!