A Spark Plasma Sintering (SPS) machine is an advanced sintering tool used in materials science and engineering to compact and sinter powders into dense materials at relatively low temperatures and short processing times. It utilizes a combination of pulsed direct current and uniaxial pressure to achieve rapid heating and densification. This method is particularly effective for creating high-performance ceramics, metals, and composites with fine microstructures and enhanced properties. SPS machines are widely used in research and industrial applications due to their efficiency and ability to produce materials with minimal grain growth and high purity.
Key Points Explained:
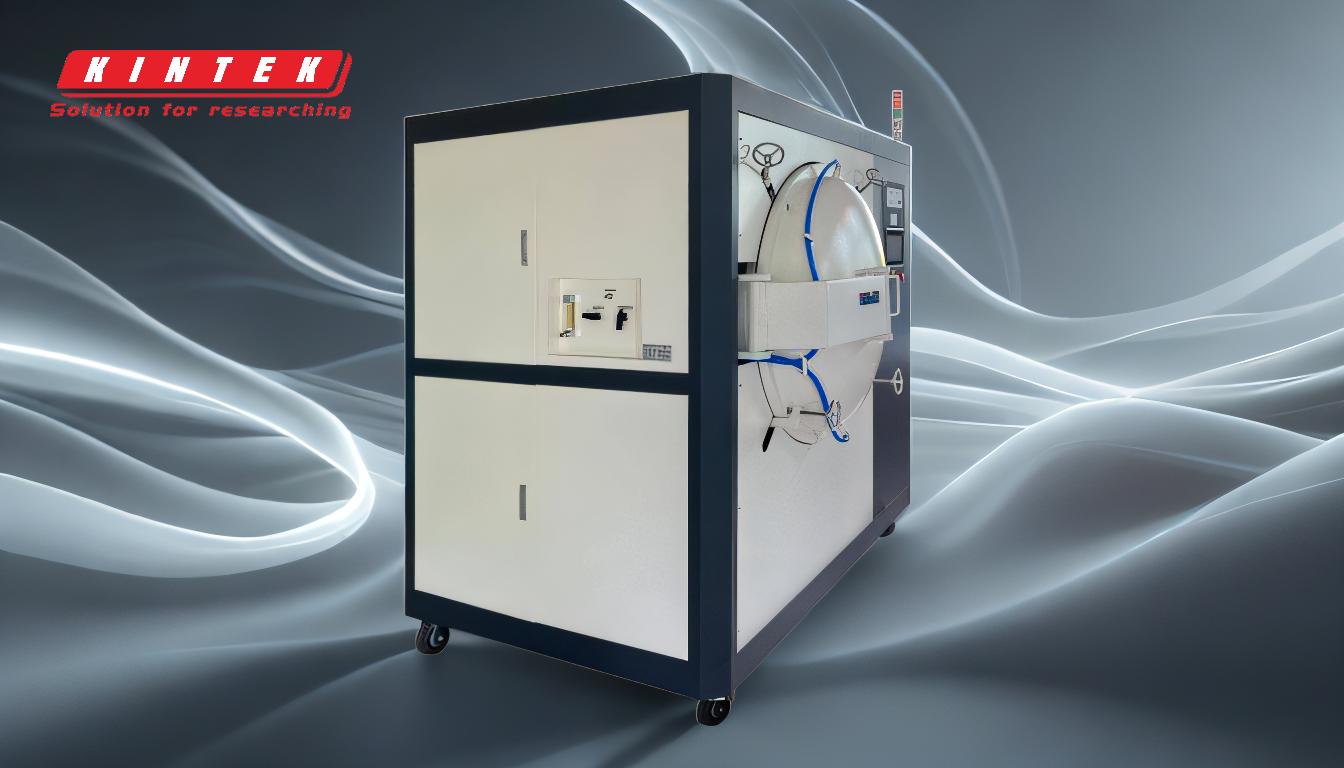
-
Definition and Purpose of SPS Machines:
- SPS machines are specialized equipment designed for sintering powdered materials into dense, high-performance components.
- They are particularly useful for materials that are difficult to sinter using conventional methods, such as ceramics, metals, and composites.
-
Working Principle:
- SPS machines use a combination of pulsed direct current and uniaxial pressure to achieve rapid heating and densification.
- The pulsed current generates plasma between the powder particles, which enhances atomic diffusion and bonding.
- The uniaxial pressure helps in consolidating the powder particles, leading to denser materials.
-
Key Components:
- Pulsed DC Power Supply: Provides the necessary electrical energy to generate plasma and heat the powder.
- Punch and Die System: Applies uniaxial pressure to the powder during sintering.
- Vacuum or Inert Gas Chamber: Prevents oxidation and contamination of the material during the sintering process.
- Control System: Allows precise control over temperature, pressure, and sintering time.
-
Advantages of SPS Technology:
- Rapid Sintering: SPS can achieve densification in minutes, compared to hours or days required by conventional methods.
- Lower Sintering Temperatures: Reduces the risk of grain growth and maintains fine microstructures.
- Enhanced Material Properties: Produces materials with high density, purity, and mechanical properties.
- Versatility: Suitable for a wide range of materials, including ceramics, metals, and composites.
-
Applications:
- Research and Development: Used in laboratories to develop new materials and study sintering mechanisms.
- Industrial Manufacturing: Employed in the production of high-performance components for aerospace, automotive, and electronics industries.
- Nanomaterials: Ideal for sintering nanomaterials due to the ability to maintain nanoscale grain sizes.
-
Comparison with Conventional Sintering Methods:
- Speed: SPS is significantly faster than traditional sintering methods like hot pressing or pressureless sintering.
- Temperature: SPS can achieve densification at lower temperatures, preserving the microstructure.
- Energy Efficiency: The rapid process reduces energy consumption compared to conventional methods.
-
Challenges and Limitations:
- Cost: SPS machines are generally more expensive than conventional sintering equipment.
- Scale-Up: Scaling up the process for large-scale production can be challenging.
- Material Compatibility: Not all materials are suitable for SPS, and some may require specific conditions or modifications.
-
Future Trends:
- Automation: Increasing automation and integration with other manufacturing processes.
- New Materials: Development of new materials and composites using SPS technology.
- Sustainability: Focus on reducing energy consumption and environmental impact.
In conclusion, SPS machines represent a significant advancement in sintering technology, offering numerous advantages over conventional methods. Their ability to produce high-performance materials with fine microstructures makes them invaluable in both research and industrial applications. As technology continues to evolve, SPS machines are expected to play an increasingly important role in the development of advanced materials.
Summary Table:
Aspect | Details |
---|---|
Definition | Advanced sintering tool for compacting and sintering powders into dense materials. |
Working Principle | Combines pulsed direct current and uniaxial pressure for rapid heating and densification. |
Key Components | Pulsed DC power supply, punch and die system, vacuum/inert gas chamber, control system. |
Advantages | Rapid sintering, lower temperatures, enhanced material properties, versatility. |
Applications | Research, industrial manufacturing, nanomaterials. |
Challenges | High cost, scale-up difficulties, material compatibility. |
Future Trends | Automation, new materials, sustainability. |
Unlock the potential of advanced materials with SPS technology—contact us today to learn more!