Diffusion bonding is a solid-state welding technique that joins materials without melting them, relying on atomic diffusion at the interface under high temperature and pressure. It is particularly useful for joining similar or dissimilar metals that are difficult to weld using conventional methods. An example of a diffusion bond involves joining dissimilar metals, such as copper to titanium or copper to aluminum, which are challenging to bond through traditional welding due to their differing thermal and mechanical properties. This process is widely used in industries like aerospace, nuclear, and electronics, where high-strength, leak-tight joints are required.
Key Points Explained:
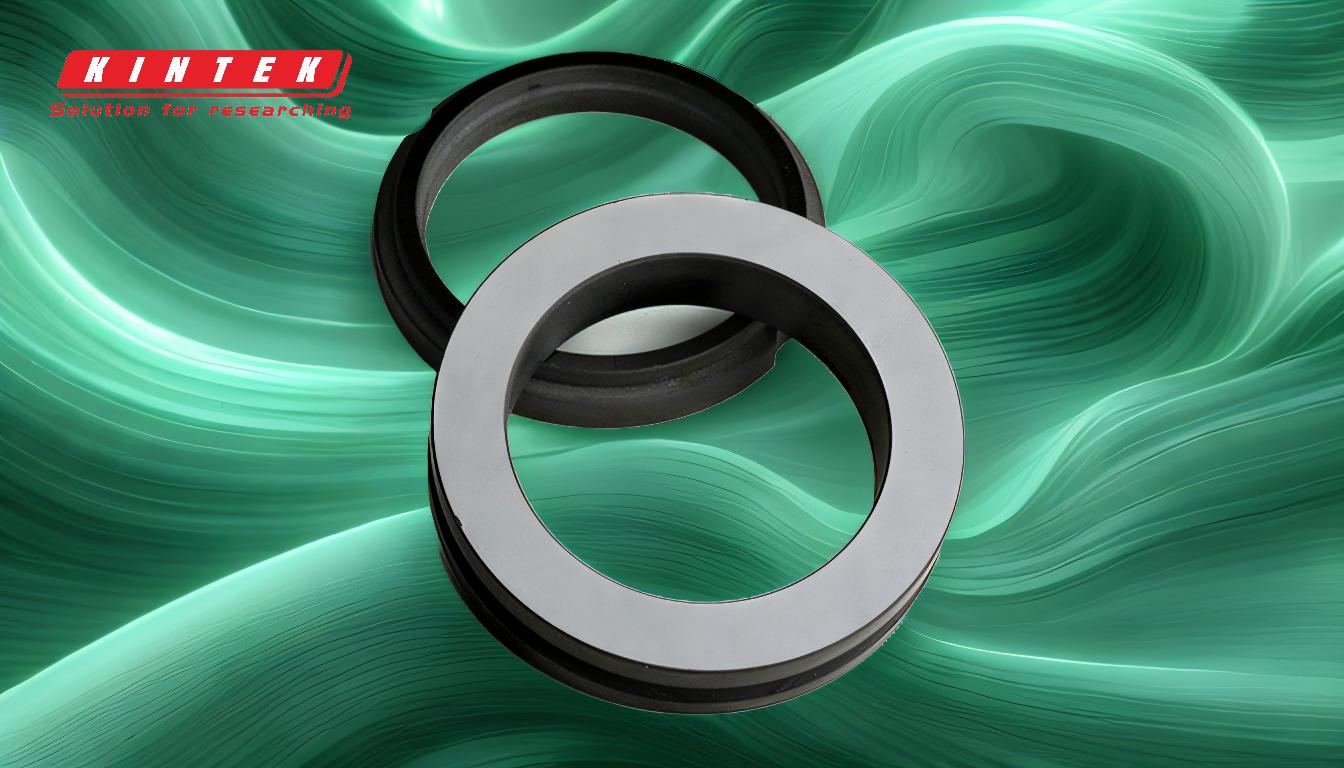
-
Definition of Diffusion Bonding:
- Diffusion bonding is a solid-state welding process where two materials are joined by applying heat and pressure, causing atoms to diffuse across the interface. This method avoids melting the materials, preserving their properties and minimizing defects.
-
Common Materials Used:
- The process is suitable for a wide range of materials, including:
- Stainless steel
- Titanium
- Zirconium
- Beryllium
- High-alloyed aluminum
- Inconel
- Tungsten
- These materials are chosen for their high strength, corrosion resistance, and ability to withstand extreme environments.
- The process is suitable for a wide range of materials, including:
-
Joining Dissimilar Metals:
- Diffusion bonding is particularly effective for joining dissimilar metals, such as:
- Copper to titanium
- Copper to aluminum
- Copper to tungsten
- Molybdenum to aluminum
- These combinations are challenging to weld using traditional methods due to differences in thermal expansion coefficients, melting points, and chemical compatibility.
- Diffusion bonding is particularly effective for joining dissimilar metals, such as:
-
Process Conditions:
- The bonding process typically requires:
- High temperatures (usually 50-70% of the melting point of the materials)
- High pressure to ensure intimate contact between surfaces
- A controlled atmosphere (often vacuum or inert gas) to prevent oxidation
- The bonding process typically requires:
-
Applications:
- Diffusion bonding is used in industries requiring high-performance joints, such as:
- Aerospace: For components like turbine blades and heat exchangers
- Nuclear: For fuel rods and reactor components
- Electronics: For heat sinks and interconnects
- The process is valued for creating leak-tight, high-strength joints with minimal distortion.
- Diffusion bonding is used in industries requiring high-performance joints, such as:
-
Advantages:
- Preserves material properties by avoiding melting
- Enables joining of dissimilar materials
- Produces high-strength, defect-free joints
- Suitable for complex geometries and thin sections
-
Challenges:
- Requires precise control of temperature, pressure, and atmosphere
- Surface preparation is critical to ensure clean, flat interfaces
- Longer processing times compared to conventional welding methods
In summary, diffusion bonding is a versatile and reliable method for joining materials, especially dissimilar metals, in demanding applications. Its ability to create strong, leak-tight joints without melting the materials makes it indispensable in industries where performance and reliability are critical.
Summary Table:
Aspect | Details |
---|---|
Definition | Solid-state welding using heat and pressure to join materials without melting. |
Common Materials | Stainless steel, titanium, zirconium, beryllium, aluminum, Inconel, tungsten. |
Dissimilar Metal Pairs | Copper to titanium, copper to aluminum, copper to tungsten, molybdenum to aluminum. |
Process Conditions | High temperature, high pressure, controlled atmosphere (vacuum or inert gas). |
Applications | Aerospace (turbine blades, heat exchangers), nuclear (fuel rods), electronics (heat sinks). |
Advantages | Preserves material properties, enables dissimilar metal joining, defect-free joints. |
Challenges | Precise control of temperature/pressure, surface preparation, longer processing times. |
Interested in diffusion bonding solutions for your industry? Contact us today to learn more!