An isostatic press is a versatile piece of equipment used in various industries to compact and shape materials through the application of uniform pressure from all directions. This process is essential for creating high-density, uniform components with minimal defects. Isostatic presses are categorized into three types based on temperature: cold isostatic pressing (CIP), warm isostatic pressing (WIP), and hot isostatic pressing (HIP). Each type serves specific applications, ranging from powder metallurgy and ceramics to advanced materials like lithium batteries and artificial bones. The process ensures consistent material properties, making it ideal for industries requiring precision and reliability.
Key Points Explained:
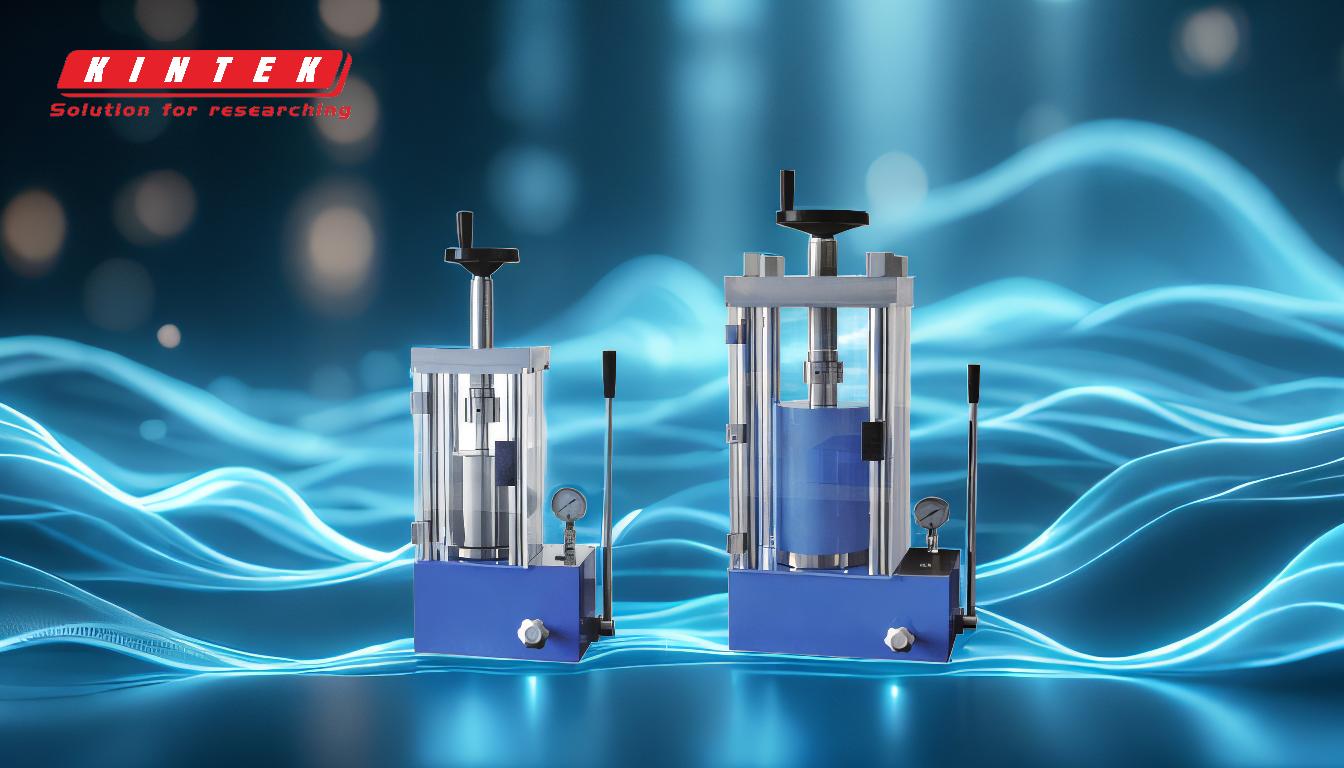
-
Types of Isostatic Pressing:
-
Cold Isostatic Pressing (CIP):
- Used for compacting green parts at ambient temperatures.
- Ideal for materials like refractory materials, insulators, isotropic graphite, high-melting-point metals, cemented carbides, and tool steel.
- Commonly used for wear and metal-forming tools, as well as large parts that do not require high precision in the sintered state.
-
Warm Isostatic Pressing (WIP):
- Heated to the temperature of the liquid medium, ensuring accurate temperature control.
- Used in applications like lithium battery production, where compression and static heating are required.
-
Hot Isostatic Pressing (HIP):
- Involves heating parts in a chamber with inert argon gas, applying high pressure and temperature.
- Used to eliminate porosity and improve mechanical properties in materials like aerospace components and medical implants.
-
Cold Isostatic Pressing (CIP):
-
Applications of Isostatic Pressing:
-
Powder Metallurgy:
- Used to form complex shapes from metal powders, ensuring uniform density and minimal defects.
-
Ceramics and Refractories:
- Ideal for producing high-density ceramic components with consistent properties.
-
Advanced Materials:
- Used in the production of lithium batteries, artificial bones, and sintered filters.
-
Food Processing:
- Applied in compacting food powders for specific applications.
-
Powder Metallurgy:
-
Process Mechanics:
- Products are placed in a closed container filled with liquid and subjected to equal pressure on all surfaces.
- This uniform pressure increases material density and shapes the product under high pressure.
- The process is closely monitored for temperature, pressure, and time to ensure optimal results.
-
Material Characterization:
- The properties of the metal powder or raw material significantly affect the final component's properties.
- Careful characterization of materials ensures the final product meets desired specifications, such as strength, density, and durability.
-
Advantages of Isostatic Pressing:
- Uniform Density: Ensures consistent material properties throughout the component.
- Complex Shapes: Capable of forming intricate geometries that are difficult to achieve with other methods.
- Reduced Defects: Minimizes porosity and improves mechanical properties.
- Versatility: Suitable for a wide range of materials and industries.
For more detailed information on isostatic press, you can explore its applications and benefits in various industrial processes.
Summary Table:
Aspect | Details |
---|---|
Types | Cold (CIP), Warm (WIP), Hot (HIP) |
Applications | Powder metallurgy, ceramics, lithium batteries, artificial bones, food processing |
Key Advantages | Uniform density, complex shapes, reduced defects, versatility |
Process Mechanics | Equal pressure on all surfaces, monitored temperature, pressure, and time |
Ready to enhance your material processing? Contact us today to learn more about isostatic presses!