An overheated brazed joint can compromise the integrity and performance of the joint, leading to potential failures in the application. Overheating during brazing can result in various visual, structural, and metallurgical indicators. These include discoloration, grain growth, weakened mechanical properties, and potential cracking. Understanding these signs is critical for ensuring the quality and reliability of brazed joints in industrial and manufacturing processes.
Key Points Explained:
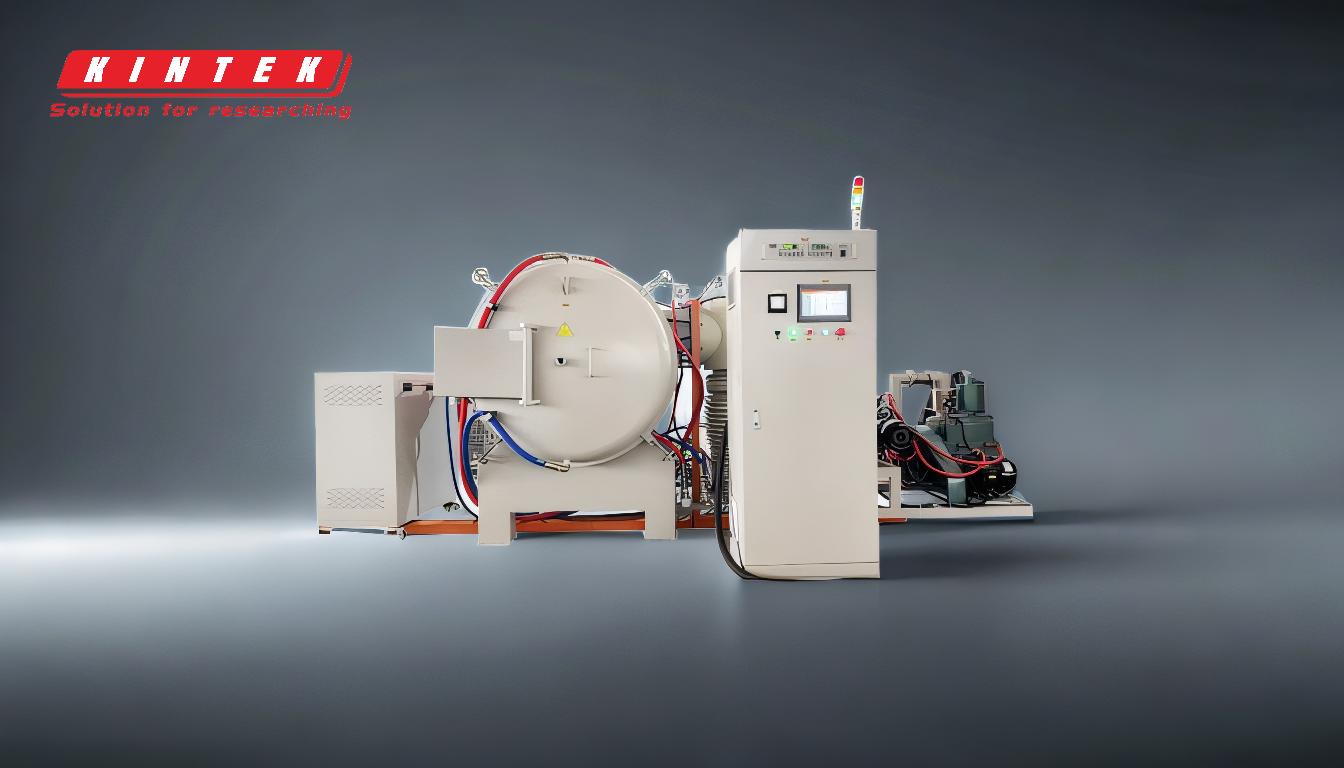
-
Discoloration:
- Overheating often causes the brazed joint to exhibit unusual discoloration. This can range from a bluish or blackened appearance to a burnt or charred look, depending on the materials involved.
- Discoloration is a clear visual indicator that the joint has been exposed to excessive heat, which can alter the metallurgical properties of the base materials and filler metal.
-
Grain Growth:
- Prolonged exposure to high temperatures can lead to excessive grain growth in the base metal. This results in a coarser grain structure, which weakens the mechanical properties of the joint.
- Grain growth reduces the joint's strength, ductility, and fatigue resistance, making it more susceptible to failure under stress.
-
Weakened Mechanical Properties:
- Overheating can cause the filler metal to become brittle or improperly bonded to the base materials. This results in a joint that lacks the necessary strength and durability.
- The joint may exhibit reduced tensile strength, shear strength, and impact resistance, which are critical for its performance in demanding applications.
-
Cracking or Fractures:
- Excessive heat can induce thermal stresses in the joint, leading to cracking or fractures. These defects may be visible on the surface or hidden within the joint.
- Cracking compromises the structural integrity of the joint and can lead to catastrophic failure during operation.
-
Oxidation or Scaling:
- Overheating can cause oxidation or scaling on the surface of the joint, particularly in materials prone to oxidation, such as stainless steel or titanium.
- Oxide layers can interfere with the bonding process, reducing the joint's effectiveness and creating weak points.
-
Poor Wetting and Flow of Filler Metal:
- Overheating can disrupt the proper wetting and flow of the filler metal, leading to incomplete or uneven joint formation.
- Poor wetting results in gaps or voids in the joint, which can act as stress concentrators and reduce the joint's load-bearing capacity.
-
Metallurgical Changes:
- Excessive heat can alter the microstructure of the base materials and filler metal, leading to undesirable phases or intermetallic compounds.
- These changes can negatively impact the joint's corrosion resistance, thermal stability, and overall performance.
-
Inspection and Prevention:
- Regular inspection of brazed joints for signs of overheating is essential. Techniques such as visual inspection, dye penetrant testing, and ultrasonic testing can help identify defects.
- To prevent overheating, it is crucial to follow proper brazing procedures, including controlling the heating rate, maintaining the correct temperature, and using appropriate shielding gases.
By recognizing these indicators and understanding their implications, manufacturers and engineers can take corrective actions to ensure the quality and reliability of brazed joints in their applications.
Summary Table:
Indicator | Description |
---|---|
Discoloration | Bluish, blackened, or burnt appearance due to excessive heat exposure. |
Grain Growth | Coarser grain structure, weakening mechanical properties. |
Weakened Mechanical Properties | Brittle filler metal, reduced tensile and shear strength. |
Cracking or Fractures | Thermal stresses causing visible or hidden cracks. |
Oxidation or Scaling | Surface oxidation, especially in stainless steel or titanium. |
Poor Wetting and Flow | Incomplete or uneven joint formation due to improper filler metal flow. |
Metallurgical Changes | Altered microstructure, leading to undesirable phases or intermetallic compounds. |
Inspection and Prevention | Use visual inspection, dye penetrant, or ultrasonic testing to detect defects. |
Ensure the quality of your brazed joints—contact our experts today for guidance and solutions!