Annealing is a critical heat treatment process used to alter the physical and mechanical properties of materials, primarily metals. It involves heating the material to a specific temperature, holding it at that temperature for a set period, and then cooling it at a controlled rate. This process is widely employed to soften materials, relieve internal stresses, improve machinability, and enhance ductility. By reducing hardness and increasing toughness, annealing makes materials more suitable for further processing, such as machining, cold working, or additional heat treatments. The process can also refine the microstructure of the material, leading to improved mechanical, electrical, or dimensional properties.
Key Points Explained:
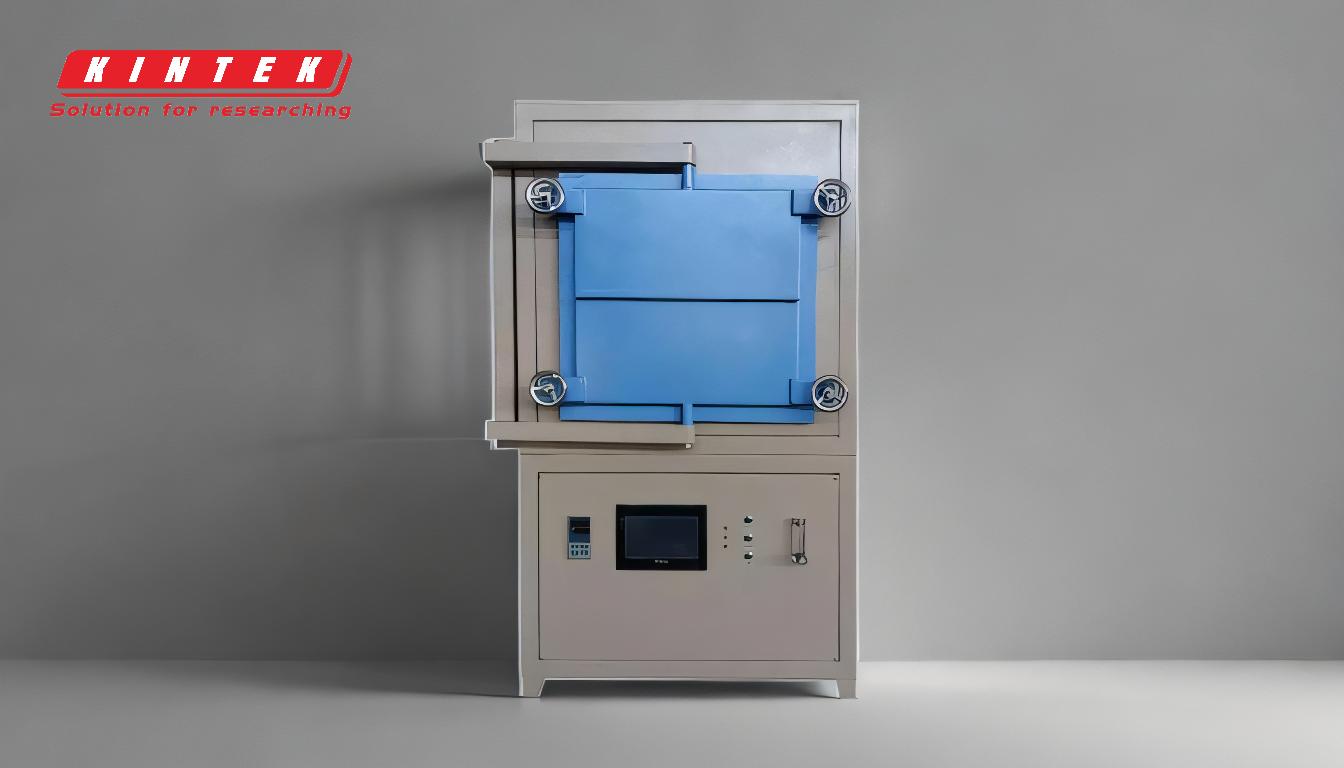
-
Definition and Purpose of Annealing:
- Annealing is a heat treatment process that involves heating a material to a specific temperature, holding it there, and then cooling it slowly.
- The primary purpose is to soften the material, making it easier to work with during manufacturing processes like machining or cold working.
- It also helps in relieving internal stresses caused by prior processing, such as cutting, casting, or cold working.
-
Benefits of Annealing:
- Improved Machinability: By reducing hardness, annealing makes materials easier to cut, shape, or machine.
- Enhanced Ductility: The process increases the material's ability to deform without breaking, which is crucial for processes like cold working.
- Stress Relief: Annealing eliminates residual stresses, reducing the risk of cracking or distortion during further processing.
- Microstructural Changes: It can refine the grain structure, leading to better mechanical properties, such as toughness and uniformity.
-
Types of Annealing:
- Full Annealing: Involves heating the material above its critical temperature (where austenite forms) and then cooling it slowly. This results in a soft, stress-free material with low hardness, ideal for further processing.
- Process Annealing: Used to restore ductility in work-hardened materials without significantly altering their microstructure.
- Stress Relief Annealing: Focuses on reducing internal stresses without major changes to the material's hardness or microstructure.
-
Applications of Annealing:
- Manufacturing: Used in industries like automotive, aerospace, and construction to prepare materials for machining, welding, or forming.
- Electronics: Enhances the electrical properties of metals used in components like wires and circuits.
- Tooling: Improves the durability and performance of tools by reducing brittleness and increasing toughness.
-
Cooling Rates and Their Impact:
- Slow cooling is essential in annealing to allow the material's microstructure to transform uniformly, resulting in reduced hardness and increased ductility.
- Rapid cooling can lead to the formation of undesirable phases, such as martensite, which increases hardness and brittleness.
-
Role in Material Processing:
- Annealing is often a preparatory step before further heat treatments or mechanical processes.
- It ensures that materials are in an optimal state for subsequent operations, reducing the risk of defects or failures.
By understanding the principles and applications of annealing, manufacturers can optimize material properties for specific applications, ensuring better performance and longevity of products.
Summary Table:
Aspect | Details |
---|---|
Definition | Heat treatment process involving heating, holding, and slow cooling. |
Purpose | Softens materials, relieves stress, and enhances ductility and machinability. |
Types | Full annealing, process annealing, stress relief annealing. |
Applications | Manufacturing, electronics, tooling. |
Cooling Rates | Slow cooling ensures uniform microstructure; rapid cooling increases hardness. |
Benefits | Improved machinability, enhanced ductility, stress relief, refined microstructure. |
Discover how annealing can optimize your material processing—contact our experts today!