Brazing in heat treatment is a metal-joining process where two or more metal items are joined together by melting and flowing a filler metal into the joint. The filler metal has a lower melting point than the adjoining metal, allowing it to flow into the joint by capillary action. This process is typically performed at temperatures above 840°F (450°C) but below the melting point of the base metals. Brazing is widely used in various industries due to its ability to create strong, leak-proof, and durable joints without significantly altering the properties of the base materials. It is particularly useful for joining dissimilar metals and complex assemblies.
Key Points Explained:
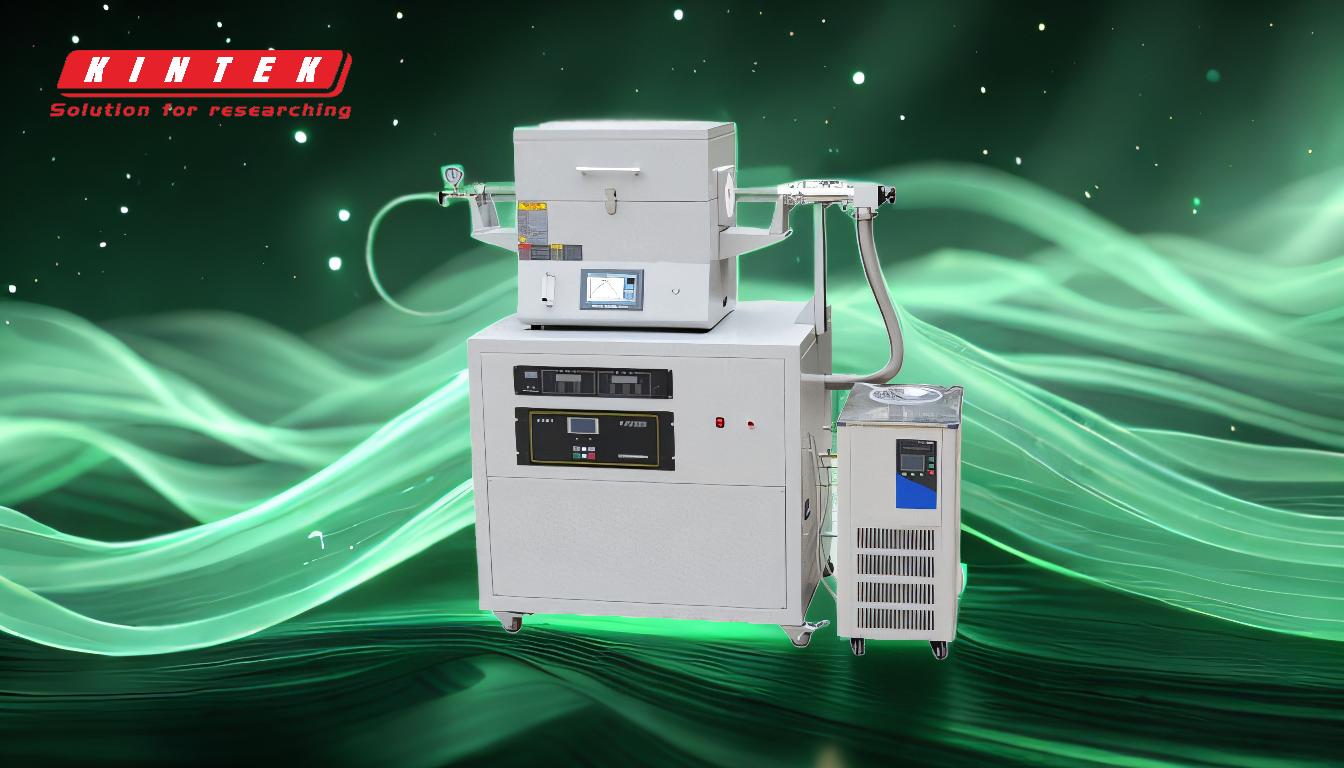
-
Definition of Brazing:
- Brazing is a metal-joining process where a filler metal is melted and flowed into the joint between two or more base metals. The filler metal has a lower melting point than the base metals, allowing it to create a strong bond without melting the base materials.
-
Temperature Range:
- Brazing is typically performed at temperatures above 840°F (450°C) but below the melting point of the base metals. This temperature range ensures that the filler metal melts and flows into the joint while the base metals remain solid.
-
Capillary Action:
- The process relies on capillary action, where the molten filler metal is drawn into the joint by the narrow gaps between the base metals. This ensures a strong and uniform bond throughout the joint.
-
Filler Metals:
- Common filler metals used in brazing include silver, copper, aluminum, and nickel-based alloys. The choice of filler metal depends on the base metals being joined and the desired properties of the joint, such as strength, corrosion resistance, and thermal conductivity.
-
Fluxes and Atmospheres:
- Fluxes are often used in brazing to prevent oxidation and to promote wetting of the filler metal. In some cases, brazing is performed in a controlled atmosphere or vacuum to further protect the joint from contamination.
-
Applications:
- Brazing is used in a wide range of industries, including automotive, aerospace, electronics, and HVAC. It is particularly useful for joining dissimilar metals and complex assemblies where welding or other joining methods may not be feasible.
-
Advantages:
- Brazing offers several advantages, including the ability to join dissimilar metals, create strong and leak-proof joints, and maintain the integrity of the base materials. It also allows for the joining of complex geometries and thin-walled components.
-
Disadvantages:
- Some disadvantages of brazing include the need for precise temperature control, the potential for joint contamination if fluxes are not properly used, and the requirement for clean and well-prepared surfaces.
-
Comparison to Other Joining Methods:
- Compared to welding, brazing typically results in less thermal distortion and stress in the base materials. It also allows for the joining of dissimilar metals, which can be challenging with welding. However, brazed joints may not have the same strength as welded joints, depending on the application.
-
Quality Control:
- Quality control in brazing involves ensuring proper joint design, surface preparation, and temperature control. Non-destructive testing methods, such as X-ray or ultrasonic testing, may be used to inspect the integrity of brazed joints.
Brazing is a versatile and effective method for joining metals in heat treatment processes, offering a range of benefits for various industrial applications. Understanding the principles and techniques of brazing can help in selecting the appropriate method for specific joining needs.
Summary Table:
Aspect | Details |
---|---|
Definition | Metal-joining process using a filler metal with a lower melting point. |
Temperature Range | Above 840°F (450°C) but below the melting point of base metals. |
Key Mechanism | Capillary action draws molten filler metal into the joint. |
Common Filler Metals | Silver, copper, aluminum, nickel-based alloys. |
Applications | Automotive, aerospace, electronics, HVAC, and more. |
Advantages | Joins dissimilar metals, creates leak-proof joints, maintains base material integrity. |
Disadvantages | Requires precise temperature control and clean surfaces. |
Discover how brazing can enhance your metal-joining processes—contact our experts today!