Carburizing is a heat treatment process used to enhance the surface properties of low-carbon steel alloys by introducing carbon into the surface layer. This process increases the hardness and wear resistance of the steel while maintaining a ductile and tough core. Carburizing is achieved by heating the steel below its melting point in a carbon-rich environment, allowing carbon atoms to diffuse into the surface. After diffusion, the steel is quenched in oil to harden the carbon-enriched surface. Typical case depths range from 0.020″ to 0.050″, making it ideal for applications requiring a hard, wear-resistant exterior and a resilient core.
Key Points Explained:
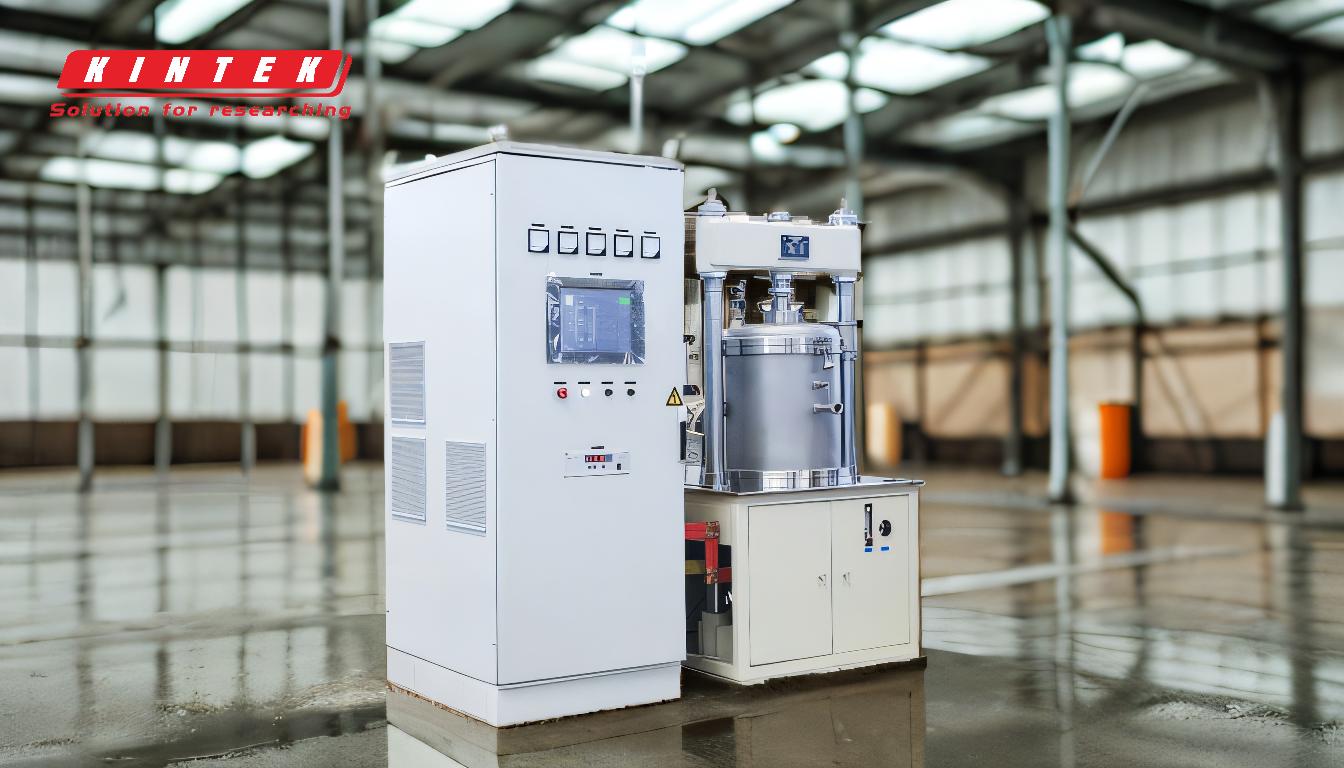
-
Definition and Purpose of Carburizing:
- Carburizing is a surface hardening process applied to low-carbon steel alloys.
- The primary purpose is to enrich the steel's surface with carbon, increasing its hardness and wear resistance while maintaining a soft, ductile core.
- This process is particularly useful for components that require high surface durability, such as gears, shafts, and bearings.
-
Process Mechanism:
- The steel is heated below its melting point in a carbon-rich environment, such as an endothermic atmosphere or a carbon-containing medium.
- Carbon atoms diffuse into the steel's surface, creating a carbon-enriched layer.
- After diffusion, the steel is rapidly quenched in oil or another cooling medium to harden the surface.
-
Benefits of Carburizing:
- Surface Hardness: The carbon-enriched surface becomes significantly harder, improving wear resistance.
- Ductile Core: The core remains soft and malleable, providing toughness and resistance to impact.
- Case Depth Control: The depth of the hardened layer (typically 0.020″ to 0.050″) can be controlled to meet specific application requirements.
-
Applications of Carburized Steel:
- Carburized steel is widely used in industries requiring components with high surface durability and fatigue resistance.
- Common applications include automotive parts (gears, camshafts), industrial machinery (bearings, rollers), and tools.
-
Comparison to Other Heat Treatment Processes:
- Unlike through-hardening, which hardens the entire component, carburizing selectively hardens only the surface.
- This allows for a combination of surface hardness and core toughness, which is not achievable with other processes like quenching and tempering.
-
Endothermic Atmosphere in Carburizing:
- An endothermic atmosphere is often used in carburizing to provide a controlled carbon-rich environment.
- This atmosphere ensures consistent carbon diffusion and prevents oxidation of the steel surface.
-
Importance of Quenching:
- Quenching is a critical step in the carburizing process, as it locks in the carbon atoms and transforms the surface into a hard martensitic structure.
- The choice of quenching medium (e.g., oil, water, or polymer) affects the final hardness and distortion of the component.
-
Material Considerations:
- Carburizing is most effective on low-carbon steels, as they have a higher capacity to absorb carbon.
- High-carbon steels are generally not suitable for carburizing, as they already contain sufficient carbon for hardening.
-
Quality Control and Testing:
- The effectiveness of carburizing is often verified through hardness testing (e.g., Rockwell or Vickers hardness tests) and microstructural analysis.
- Case depth is measured to ensure it meets design specifications.
-
Environmental and Safety Considerations:
- Carburizing processes must be conducted in well-ventilated areas due to the use of carbon-rich gases and quenching oils.
- Proper handling of quenching media and disposal of waste materials are essential to minimize environmental impact.
By understanding these key points, a purchaser of equipment or consumables can make informed decisions about the suitability of carburizing for their specific applications. This process offers a balance of surface hardness and core toughness, making it a versatile and widely used heat treatment method in various industries.
Summary Table:
Aspect | Details |
---|---|
Purpose | Surface hardening for low-carbon steel alloys. |
Process | Heating in a carbon-rich environment, followed by quenching. |
Benefits | Increased surface hardness, wear resistance, and controlled case depth. |
Applications | Gears, shafts, bearings, automotive parts, and industrial machinery. |
Material Suitability | Most effective on low-carbon steels; not suitable for high-carbon steels. |
Key Step | Quenching to lock in carbon and harden the surface. |
Testing | Hardness tests (Rockwell/Vickers) and microstructural analysis. |
Discover how carburizing can improve your steel components—contact us today for expert advice!