Chemical vapor deposition (CVD) is a sophisticated technique used to create high-purity, high-performance solid materials by depositing thin films onto a substrate. The process involves the use of gaseous precursors that react or decompose on a heated substrate surface, forming a solid layer. This method is widely utilized in industries such as semiconductor manufacturing, optics, and protective coatings due to its ability to produce dense, uniform, and stoichiometric films. The CVD process is characterized by several key steps, including the transport of gaseous species, adsorption, surface reactions, and desorption of by-products. The process can be tailored by adjusting parameters such as temperature, pressure, and precursor composition to achieve specific film properties.
Key Points Explained:
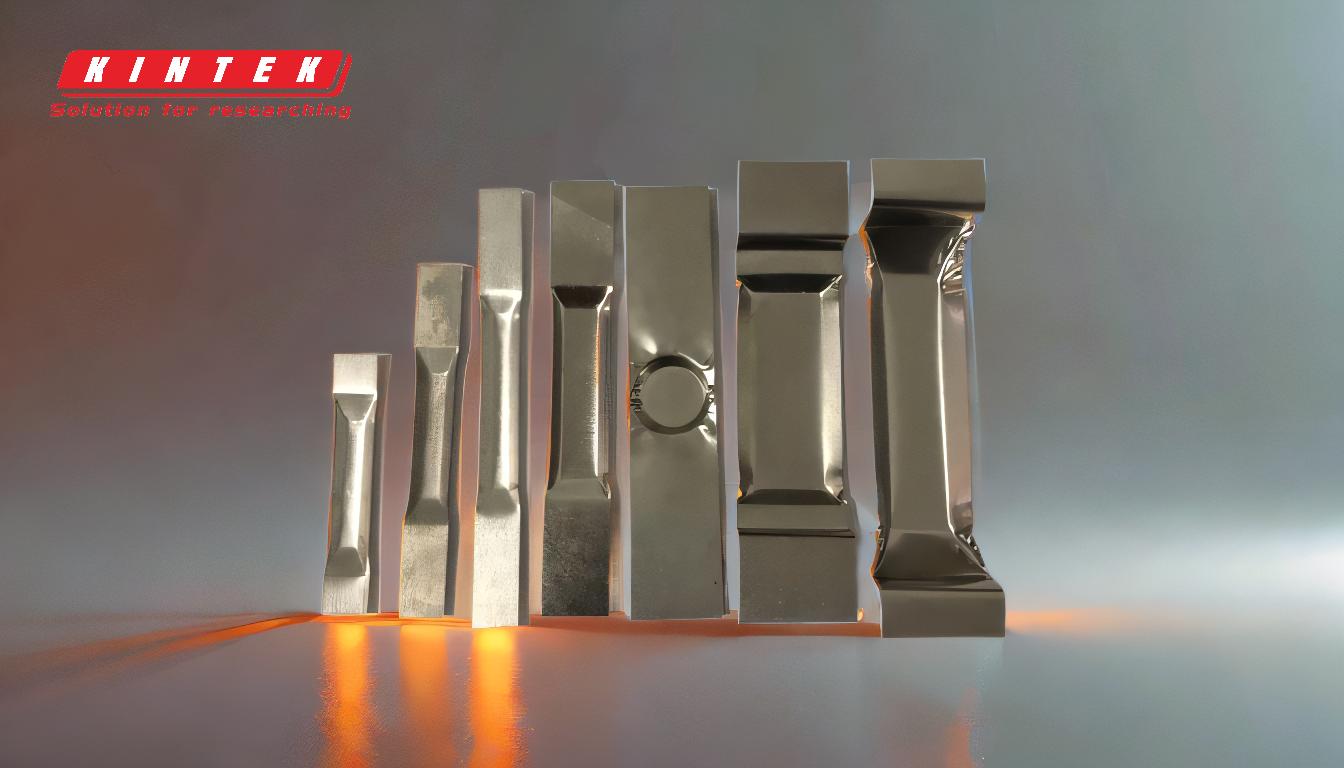
-
Definition and Purpose of CVD:
- Chemical vapor deposition (CVD) is a chemical process used to deposit thin, solid films onto a substrate. The process is essential for creating materials with high purity, uniformity, and performance, making it ideal for applications in electronics, optics, and protective coatings.
-
Steps Involved in CVD:
- Transport of Gaseous Species: The gaseous precursors are introduced into the reaction chamber and transported to the substrate surface.
- Adsorption: The gaseous species adsorb onto the substrate surface.
- Surface Reactions: The adsorbed species undergo chemical reactions, often catalyzed by the surface, leading to the formation of the desired material.
- Surface Diffusion: The reacted species diffuse across the surface to growth sites.
- Nucleation and Growth: The material nucleates and grows into a continuous film.
- Desorption and Removal of By-products: Volatile by-products are desorbed from the surface and removed from the chamber by gas flow.
-
Role of Temperature and Pressure:
- The CVD process typically occurs at high temperatures (often above 500°C) to provide the thermal energy necessary for the decomposition of precursor molecules. Higher pressures can enhance the reproducibility and quality of the deposited films, making them denser and more stoichiometric.
-
Types of Reactions in CVD:
- Decomposition: The precursor molecules break down into atoms or simpler molecules upon heating.
- Chemical Reaction: The decomposed species react with other gases, vapors, or liquids near the substrate to form the desired material.
- Reduction: In some cases, a reducing atmosphere is used to facilitate the deposition process.
-
Advantages of CVD:
- High Purity: CVD produces materials with high purity due to the controlled environment and precise precursor selection.
- Uniformity: The process allows for the deposition of uniform films over large areas and complex geometries.
- Versatility: CVD can be used to deposit a wide range of materials, including metals, semiconductors, and insulators.
- Controlled Film Properties: By adjusting process parameters, the thickness, composition, and structure of the films can be precisely controlled.
-
Applications of CVD:
- Semiconductor Industry: CVD is extensively used for depositing thin films in the fabrication of integrated circuits, solar cells, and LEDs.
- Optics: The process is employed to create anti-reflective coatings, mirrors, and other optical components.
- Protective Coatings: CVD is used to apply wear-resistant and corrosion-resistant coatings on tools and industrial components.
-
Challenges and Considerations:
- High Temperatures: The requirement for high temperatures can limit the types of substrates that can be used.
- Precursor Selection: The choice of precursors is critical, as they must be volatile and capable of decomposing at the process temperature.
- By-product Management: The removal of volatile by-products is essential to maintain the quality of the deposited film and prevent contamination.
In summary, chemical vapor deposition is a versatile and powerful technique for creating high-quality thin films with precise control over their properties. The process involves a series of well-defined steps, from the transport of gaseous precursors to the nucleation and growth of the film. By carefully controlling parameters such as temperature, pressure, and precursor composition, CVD can be tailored to meet the specific requirements of various industrial applications.
Summary Table:
Key Aspect | Details |
---|---|
Definition | A process to deposit thin, solid films onto a substrate using gaseous precursors. |
Steps | 1. Transport of gaseous species 2. Adsorption 3. Surface reactions 4. Nucleation 5. Desorption |
Advantages | High purity, uniformity, versatility, and controlled film properties. |
Applications | Semiconductors, optics, and protective coatings. |
Challenges | High temperatures, precursor selection, and by-product management. |
Discover how CVD can enhance your material production—contact our experts today!