Chemical vapor deposition (CVD) is a widely used method for synthesizing carbon nanotubes (CNTs), offering advantages such as structural controllability, cost-effectiveness, and scalability. The process involves thermal treatments, gas-phase reactions, and catalyst deposition to grow CNTs on a substrate. CVD is particularly favored for its ability to produce high-quality CNTs with minimal environmental impact when optimized for energy efficiency and reduced greenhouse gas emissions. The process typically includes steps such as gas transport, surface adsorption, chemical reactions, and deposition, making it a versatile and efficient technique for nanomaterial fabrication.
Key Points Explained:
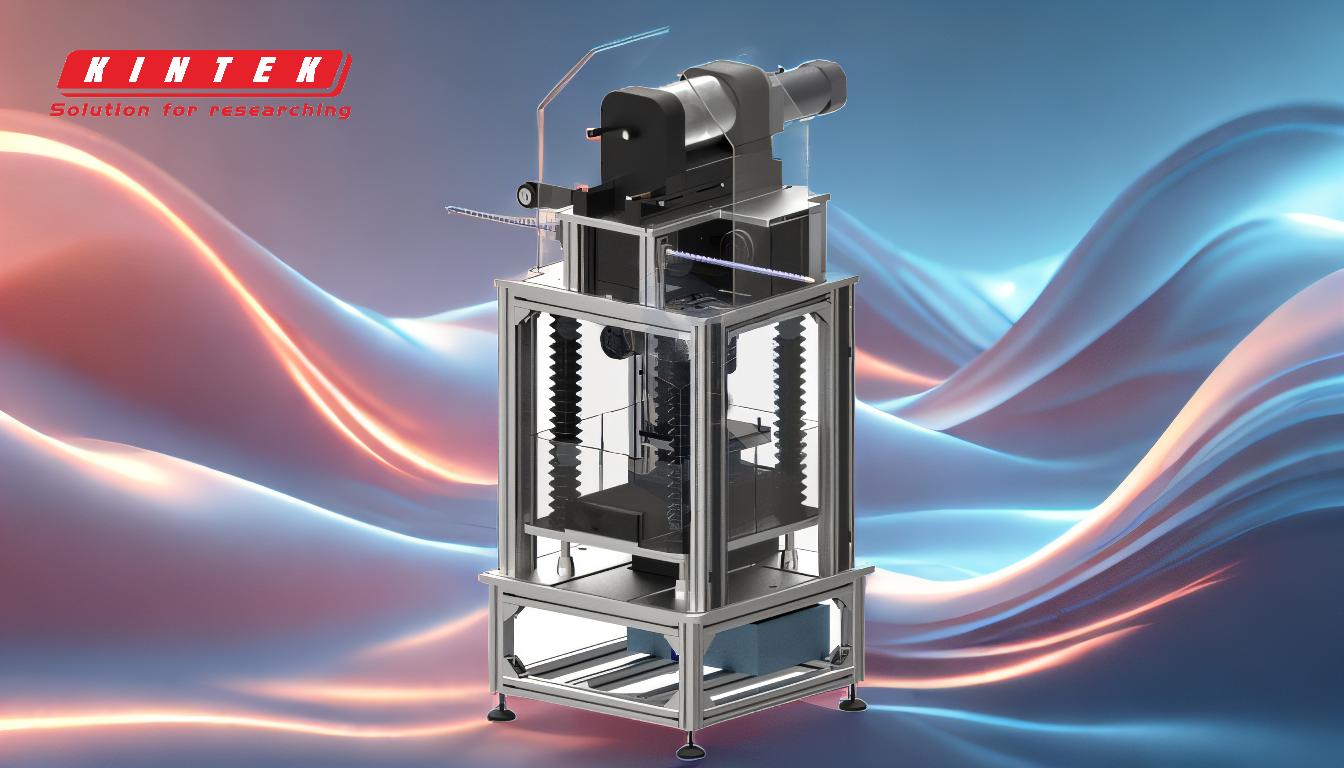
-
Overview of Chemical Vapor Deposition (CVD):
- CVD is a process where gaseous reactants undergo chemical reactions on a heated substrate to form a solid material, such as carbon nanotubes (CNTs).
- It is a key method for synthesizing CNTs due to its ability to control the structure and properties of the resulting material.
- The process is cost-effective and scalable, making it suitable for industrial applications.
-
Steps Involved in CVD for CNT Synthesis:
- Transport of Gaseous Species: Reacting gases are introduced into the reaction chamber and transported to the substrate surface.
- Adsorption: The gaseous species adsorb onto the substrate surface.
- Surface Reactions: Heterogeneous catalytic reactions occur on the substrate surface, facilitated by heat and catalysts.
- Nucleation and Growth: Carbon atoms diffuse to growth sites, where they nucleate and form CNTs.
- Desorption and Removal: Reaction by-products desorb from the surface and are transported away from the reaction zone.
-
Catalytic Chemical Vapor Deposition (CCVD):
- CCVD is the most common CVD method for CNT synthesis, using metal catalysts (e.g., iron, nickel, or cobalt) to facilitate the growth process.
- The catalysts lower the activation energy required for CNT formation, enabling growth at relatively lower temperatures.
- This method allows precise control over CNT diameter, length, and alignment.
-
Environmental and Economic Considerations:
- The synthesis process is a major contributor to the environmental impact of CNTs, particularly in terms of energy consumption and greenhouse gas emissions.
- Optimizing the CVD process to reduce material and energy use can minimize the life cycle ecotoxicity of CNTs.
- Efforts to improve cost-effectiveness and sustainability are critical for scaling up CNT production.
-
Historical Context and Evolution of CVD:
- The concept of CVD dates back to ancient times, with early examples such as soot deposition in caves.
- Modern CVD techniques have evolved significantly, incorporating advanced materials, catalysts, and process controls to achieve high-quality CNT synthesis.
-
Applications and Advantages of CVD-Grown CNTs:
- CVD-grown CNTs are used in a wide range of applications, including electronics, energy storage, composites, and biomedical devices.
- The structural controllability of CVD allows for the production of CNTs with tailored properties, such as conductivity, strength, and thermal stability.
By understanding the principles and steps involved in chemical vapor deposition, researchers and manufacturers can optimize the process to produce high-quality CNTs with minimal environmental impact. This makes CVD a cornerstone technology in the field of nanotechnology and advanced materials.
Summary Table:
Key Aspect | Details |
---|---|
Process Overview | Gaseous reactants form CNTs on a heated substrate via chemical reactions. |
Steps Involved | Gas transport, adsorption, surface reactions, nucleation, and desorption. |
Catalytic CVD (CCVD) | Uses metal catalysts for controlled CNT growth at lower temperatures. |
Environmental Impact | Optimized for energy efficiency and reduced greenhouse gas emissions. |
Applications | Electronics, energy storage, composites, and biomedical devices. |
Discover how CVD can revolutionize your CNT production—contact our experts today!