Chemical Vapor Deposition (CVD) is a versatile and widely used technique for fabricating thin films and coatings with precise control over thickness, composition, and properties. It is particularly valuable in industries such as semiconductors, optics, and solar energy. The process involves the deposition of materials from a vapor phase onto a substrate, often facilitated by heat or plasma. CVD is used to create materials like polysilicon for solar panels, silicon dioxide for electronics, and advanced coatings for semiconductors. Plasma-enhanced methods, such as microwave plasma chemical vapor deposition, further enhance the process by enabling lower-temperature deposition and improved film quality. This makes CVD indispensable for modern technology fabrication.
Key Points Explained:
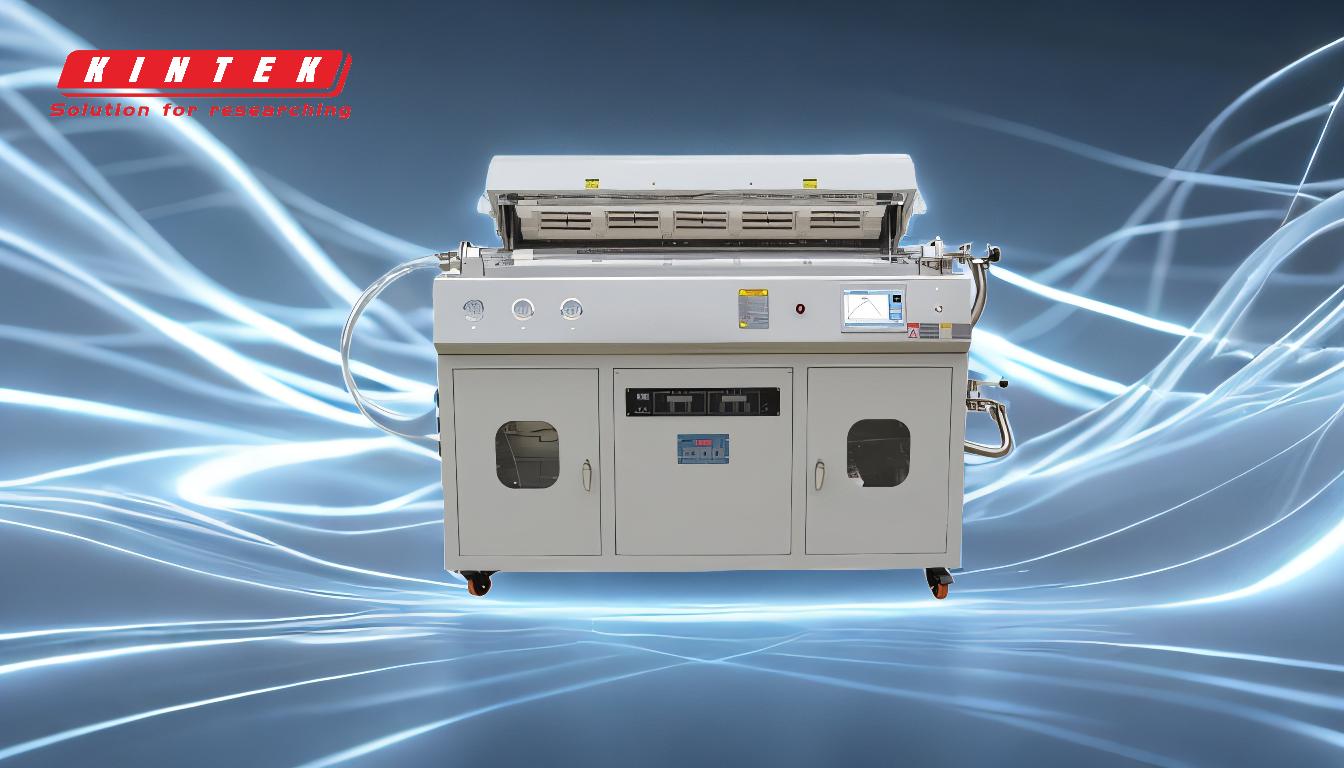
-
Overview of Chemical Vapor Deposition (CVD):
- CVD is a process where volatile compounds are vaporized and then decomposed to form thin films on a substrate.
- It involves multiple steps, including transport of gaseous species, adsorption, surface reactions, and desorption of byproducts.
- This method is highly controlled, allowing for precise fabrication of materials with specific properties.
-
Applications in Semiconductor Fabrication:
- CVD is critical for producing semiconductor components, such as transistors and integrated circuits.
- It deposits functional thin films like silicon (Si) and silicon dioxide (SiO₂), which are essential for electronic devices.
- Techniques like Plasma-Enhanced Chemical Vapor Deposition (PECVD) are particularly useful for depositing high-quality films at lower temperatures.
-
Role in Solar Energy:
- Polysilicon, a key material in solar photovoltaic (PV) cells, is often fabricated using CVD.
- The process ensures high purity and uniformity, which are crucial for efficient solar energy conversion.
- Low Pressure Chemical Vapor Deposition (LPCVD) is commonly used for depositing silicon dioxide layers in solar panels.
-
Plasma-Based CVD Methods:
- Plasma-enhanced methods, such as microwave plasma chemical vapor deposition, use plasma instead of heat to drive the deposition process.
- This allows for lower processing temperatures, reducing thermal stress on substrates and enabling the use of temperature-sensitive materials.
- These methods are particularly valuable for depositing advanced materials in semiconductor and optical applications.
-
Materials Fabricated Using CVD:
- Polysilicon: Widely used in the solar PV supply chain due to its high purity and uniformity.
- Silicon Dioxide (SiO₂): Deposited by LPCVD for use in electronics and optics.
- Poly(paraxylene): A polymer deposited via CVD for applications in coatings and encapsulation.
-
Advantages of CVD:
- Precise control over film thickness, composition, and properties.
- Ability to deposit a wide range of materials, including metals, ceramics, and polymers.
- Suitable for large-scale production and complex geometries.
-
Future Trends and Innovations:
- Ongoing research focuses on improving deposition rates, reducing costs, and expanding the range of materials that can be deposited.
- Advances in plasma-based methods, such as microwave plasma chemical vapor deposition, are expected to play a key role in next-generation technologies.
In summary, CVD is a foundational technology for fabricating advanced materials and devices across multiple industries. Its ability to produce high-quality, precise coatings and films makes it indispensable for modern manufacturing and innovation.
Summary Table:
Key Applications | Materials Fabricated | Benefits |
---|---|---|
Semiconductor Fabrication | Silicon (Si), Silicon Dioxide (SiO₂) | High precision, uniform coatings for electronics |
Solar Energy | Polysilicon | High purity, efficient energy conversion |
Advanced Coatings | Poly(paraxylene) | Encapsulation, protective layers |
Plasma-Based Methods | Microwave Plasma CVD | Lower temperature, improved film quality |
Learn how CVD can elevate your material fabrication—contact our experts today!