CVD (Chemical Vapor Deposition) and ALD (Atomic Layer Deposition) are advanced thin-film deposition techniques used in various industries, including semiconductors, optics, and coatings. Both methods rely on chemical reactions to deposit materials onto substrates, but they differ significantly in their mechanisms, precision, and applications. CVD is a versatile process capable of producing thick films at high deposition rates, making it suitable for applications requiring bulk material deposition. ALD, on the other hand, excels in precision, offering atomic-level control over film thickness and uniformity, making it ideal for ultra-thin films and complex geometries. Understanding the differences between these techniques is crucial for selecting the right method for specific applications.
Key Points Explained:
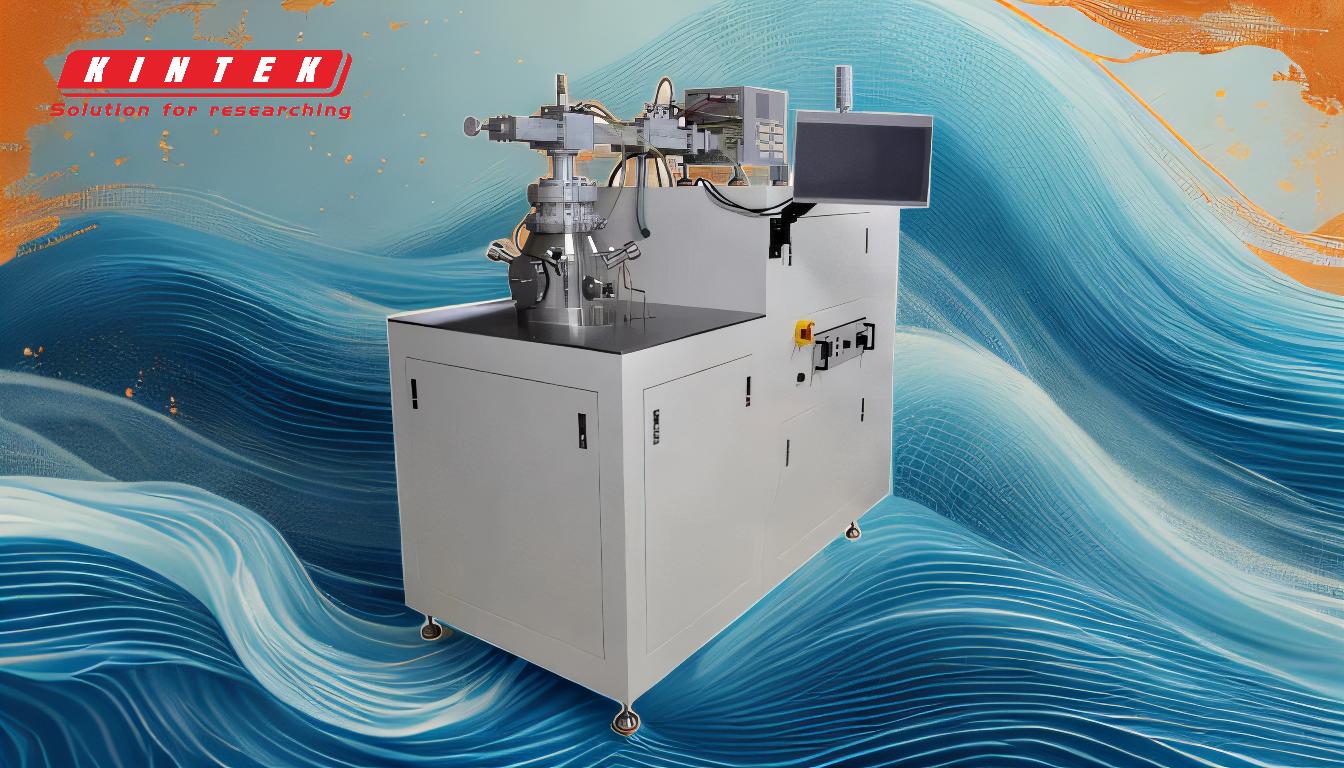
-
Definition and Basic Principles:
- CVD: Chemical Vapor Deposition involves the chemical reaction of gaseous precursors to form a solid material on a substrate. The process typically occurs at high temperatures and pressures, enabling the deposition of thick films at relatively high rates.
- ALD: Atomic Layer Deposition is a specialized form of CVD where the deposition process is broken down into discrete, self-limiting reactions. Each reaction deposits a single atomic layer, allowing for precise control over film thickness and uniformity.
-
Mechanism of Deposition:
- CVD: In CVD, precursor gases are introduced into a reaction chamber where they react or decompose on the substrate surface to form a solid film. The process is continuous, and the film grows as long as the precursors are supplied.
- ALD: ALD operates in a cyclic manner, with each cycle consisting of two or more precursor pulses separated by purge steps. Each pulse results in the deposition of a single atomic layer, ensuring precise control over film thickness and composition.
-
Control and Precision:
- CVD: While CVD offers high deposition rates and is capable of producing thick films, it generally provides less control over film thickness and uniformity compared to ALD. This makes CVD suitable for applications where precise control is less critical.
- ALD: ALD's self-limiting nature allows for atomic-level precision, making it ideal for applications requiring ultra-thin films (10-50 nm) and high-aspect-ratio structures. The layer-by-layer approach ensures excellent conformity and uniformity, even on complex geometries.
-
Applications:
- CVD: CVD is widely used in applications requiring thick films, such as protective coatings, diamond synthesis, and semiconductor device fabrication. Its ability to deposit a wide range of materials at high rates makes it versatile for various industrial applications.
- ALD: ALD is preferred for applications demanding precise control over film properties, such as in the production of advanced semiconductor devices, optical coatings, and nanoscale materials. Its ability to coat high-aspect-ratio structures uniformly makes it invaluable in microelectronics and nanotechnology.
-
Precursor Availability:
- CVD: CVD has a broader range of available precursors, allowing for the deposition of a wide variety of materials, including metals, ceramics, and polymers.
- ALD: While ALD also uses a variety of precursors, the selection is more limited due to the need for precursors that can undergo self-limiting reactions. However, the precision of ALD often outweighs this limitation in applications requiring exact control over film properties.
-
Deposition Rate and Thickness:
- CVD: CVD is characterized by high deposition rates, making it suitable for producing thick films quickly. This is advantageous in applications where time and throughput are critical factors.
- ALD: ALD's deposition rate is significantly slower due to its layer-by-layer approach. However, this slow rate is a trade-off for the ability to produce ultra-thin films with exceptional precision and uniformity.
-
Complexity and Cost:
- CVD: CVD systems can be complex and capital-intensive, especially when dealing with high temperatures and pressures. However, the ability to deposit a wide range of materials at high rates often justifies the investment.
- ALD: ALD systems are also complex and can be expensive, but the precision and control they offer make them indispensable in advanced manufacturing processes, particularly in the semiconductor industry.
-
Comparison with Other Deposition Techniques:
- PVD (Physical Vapor Deposition): Unlike CVD and ALD, PVD methods such as sputtering are line-of-sight processes, meaning only surfaces directly in the path of the source are coated. PVD is suitable for low-temperature processes and simpler substrate geometries but lacks the conformal coating capability of ALD.
In summary, both CVD and ALD are essential techniques in modern material science and engineering, each with its own strengths and ideal applications. CVD's versatility and high deposition rates make it suitable for a wide range of industrial applications, while ALD's precision and control are unmatched for advanced technologies requiring ultra-thin, uniform films. Understanding these differences is key to selecting the appropriate method for specific manufacturing needs.
Summary Table:
Aspect | CVD (Chemical Vapor Deposition) | ALD (Atomic Layer Deposition) |
---|---|---|
Deposition Mechanism | Continuous process with high deposition rates. | Cyclic, layer-by-layer process with atomic-level precision. |
Film Thickness | Thick films (micrometers). | Ultra-thin films (10-50 nm). |
Precision | Less control over thickness and uniformity. | High precision and uniformity, ideal for complex geometries. |
Applications | Protective coatings, diamond synthesis, semiconductor fabrication. | Advanced semiconductors, optical coatings, nanoscale materials. |
Precursor Availability | Wide range of precursors for metals, ceramics, and polymers. | Limited precursors due to self-limiting reaction requirements. |
Deposition Rate | High deposition rates. | Slower deposition rates. |
Complexity & Cost | High complexity and cost, justified by versatility and high throughput. | High complexity and cost, justified by precision and control in advanced applications. |
Need help selecting the right thin-film deposition technique? Contact our experts today for tailored solutions!