Chemical Vapor Deposition (CVD) is a widely used technique in nanotechnology for synthesizing nanomaterials and thin films. It involves the deposition of materials from gas-phase precursors onto a substrate at elevated temperatures, allowing for the creation of high-purity, precise nanostructures with tailored properties. CVD is versatile, enabling the production of materials like carbon nanotubes, graphene, and nanocomposite coatings, and is applied across various industries, including semiconductors, aerospace, and telecommunications. The process is highly controllable, with parameters such as temperature, gas composition, and substrate type influencing the final material properties. CVD is a bottom-up synthesis method, contrasting with high-temperature, short-duration techniques like electric arc discharge.
Key Points Explained:
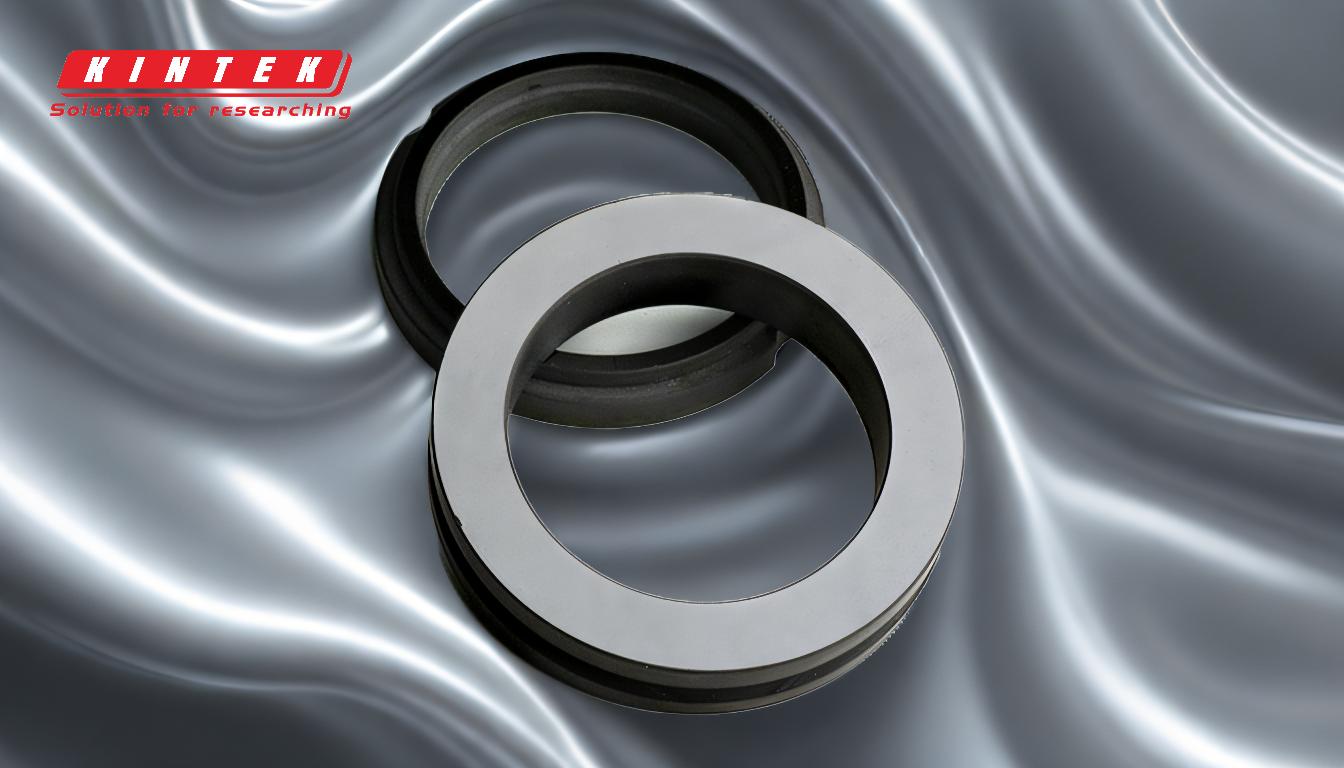
-
Definition and Process of CVD:
- CVD is a thin-film deposition technique where gas-phase precursors react at elevated temperatures to form nanomaterials on a substrate.
- It is a medium-temperature process (500–1100°C), making it suitable for producing materials like carbon nanotubes (CNTs) without the extreme conditions required by methods like electric arc discharge (> 3000°C).
-
Versatility and Applications:
- CVD is used to synthesize a wide range of nanomaterials, including single-walled nanotubes, graphene, and nanocomposite coatings.
- Applications span industries such as semiconductors (integrated circuits, sensors), aerospace (wear-resistant coatings), telecommunications (optical fibers), and catalysis.
-
Control Over Material Properties:
- By adjusting parameters like substrate type, temperature, and gas composition, CVD allows for the creation of materials with specific properties, such as high purity, abrasion resistance, and thermal stability.
- For example, CVD is used to grow large-area, monolayer graphene sheets on metal foil substrates, which can then be transferred to other substrates for various applications.
-
Types of CVD:
- Thermal CVD: Relies on heat to drive the chemical reactions for material deposition.
- Plasma-Enhanced CVD (PECVD): Uses plasma to lower the reaction temperature, enabling the deposition of materials at lower temperatures, which is beneficial for temperature-sensitive substrates.
-
Advantages Over Other Techniques:
- CVD is a bottom-up synthesis method, allowing for precise control over the growth of nanomaterials at the atomic or molecular level.
- It can deposit conformal films and modify substrate surfaces in ways traditional techniques cannot, making it essential for applications like atomic layer deposition and the creation of super-thin coatings with unique properties (e.g., lubricity, hydrophobicity).
-
Industrial Significance:
- CVD is critical in producing strategic components for aerospace, military, and nuclear industries, where materials must withstand extreme conditions.
- It is also used in the production of catalysts and nanomachines, highlighting its importance in advancing nanotechnology.
-
Comparison with Other Methods:
- Unlike high-temperature, short-duration methods (e.g., electric arc discharge), CVD operates at lower temperatures and allows for more controlled and scalable production of nanomaterials.
- CVD's ability to produce large-area, high-quality materials makes it a preferred choice for industrial applications.
-
Future Potential:
- CVD continues to evolve, with ongoing research focused on improving its efficiency, scalability, and the range of materials it can produce.
- Its role in emerging technologies, such as gas sensing and low-κ dielectrics, underscores its importance in the future of materials science and nanotechnology.
In summary, CVD is a foundational technique in nanotechnology, enabling the precise synthesis of nanomaterials with tailored properties for a wide range of applications. Its versatility, controllability, and industrial relevance make it a cornerstone of modern materials engineering.
Summary Table:
Aspect | Details |
---|---|
Definition | Thin-film deposition using gas-phase precursors at elevated temperatures. |
Temperature Range | Medium-temperature process (500–1100°C). |
Key Applications | Semiconductors, aerospace, telecommunications, catalysis. |
Materials Produced | Carbon nanotubes, graphene, nanocomposite coatings. |
Advantages | High purity, precise control, scalability, and versatility. |
Types of CVD | Thermal CVD, Plasma-Enhanced CVD (PECVD). |
Industrial Significance | Critical for aerospace, military, and nuclear industries. |
Future Potential | Emerging applications in gas sensing, low-κ dielectrics, and nanotechnology. |
Discover how CVD can revolutionize your material synthesis process—contact our experts today!