Chemical Vapor Deposition (CVD) is a versatile and widely used method for synthesizing nanomaterials and thin films. It involves the use of volatile precursors that are introduced into a reaction chamber, typically under vacuum or controlled atmospheric conditions. These precursors are heated to specific temperatures, causing them to decompose or react chemically, forming a solid material that deposits onto a substrate. The process is highly controllable and can produce high-quality, uniform coatings with excellent adhesion. CVD is used in various industries, including electronics, optics, and materials science, due to its ability to create precise and high-performance coatings.
Key Points Explained:
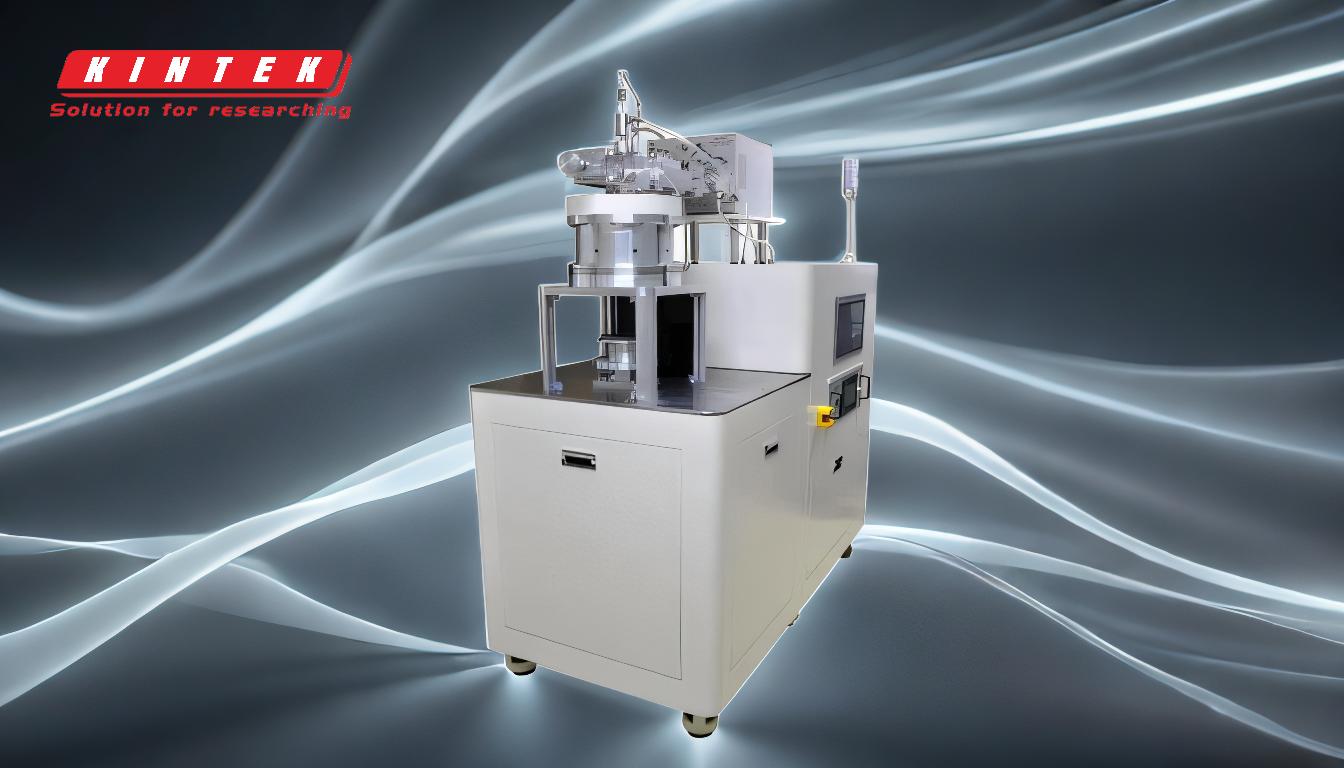
-
Basic Principles of CVD:
- CVD involves the use of volatile precursor gases that are introduced into a reaction chamber. These gases are heated to a specific temperature, causing them to decompose or react chemically.
- The resulting atoms or molecules form a thin film that deposits onto a substrate, which acts as a catalyst for the reaction.
- The process is highly controllable, allowing for the creation of uniform and high-quality coatings.
-
Steps in the CVD Process:
- Vaporization: The precursor material is vaporized and introduced into the reaction chamber.
- Decomposition: The vaporized precursor decomposes into atoms or molecules due to heat or other energy sources.
- Deposition: The decomposed atoms or molecules deposit onto the substrate, forming a thin film.
- Adhesion: The film adheres to the substrate, creating a strong bond.
-
Types of CVD:
- Thermal Chemical Vapor Deposition (TCVD): Uses high temperatures to activate chemical reactions. Common types include metal organic chemical vapor deposition, chloride chemical vapor deposition, and hydride chemical vapor deposition.
- Hot Filament Chemical Vapor Deposition (HFCVD): Involves the use of a heated filament to dissociate precursor gases. The filament is typically made of refractory metals like tungsten, rhenium, or tantalum.
- High Density Plasma Chemical Vapor Deposition (HDP-CVD): Utilizes an inductively coupled plasma (ICP) source to produce higher plasma density and quality at lower deposition temperatures. This method is particularly useful for filling trenches or holes in substrates.
-
Advantages of CVD:
- High-Quality Coatings: CVD produces dense, high-performance coatings with excellent adhesion.
- Precision and Control: The process allows for precise control over the thickness and composition of the deposited films.
- Versatility: CVD can be used to deposit a wide range of materials, including metals, semiconductors, and polymers.
- Scalability: The process can be scaled up for industrial applications, making it suitable for large-scale production.
-
Applications of CVD:
- Electronics: CVD is widely used in the semiconductor industry to deposit thin films for integrated circuits, solar cells, and other electronic components.
- Optics: The method is used to create anti-reflective coatings, mirrors, and other optical components.
- Materials Science: CVD is employed to produce advanced materials such as graphene, carbon nanotubes, and other nanomaterials.
- Protective Coatings: The process is used to apply wear-resistant and corrosion-resistant coatings to various materials.
-
Challenges and Considerations:
- Precursor Selection: The choice of precursor is critical, as it affects the quality and properties of the deposited film.
- Temperature Control: Precise temperature control is necessary to ensure proper decomposition and deposition of the precursor.
- Equipment Costs: CVD equipment can be expensive, particularly for advanced methods like HDP-CVD.
- Filament Degradation: In methods like HFCVD, the filament can degrade over time, requiring maintenance or replacement.
In summary, CVD is a powerful and versatile method for synthesizing nanomaterials and thin films. Its ability to produce high-quality, uniform coatings with excellent adhesion makes it a valuable tool in various industries. Understanding the principles, types, and applications of CVD can help in selecting the right method for specific needs and optimizing the process for desired outcomes.
Summary Table:
Aspect | Details |
---|---|
Basic Principles | Uses volatile precursors, heated to decompose and deposit thin films. |
Steps in CVD Process | Vaporization, Decomposition, Deposition, Adhesion. |
Types of CVD | TCVD, HFCVD, HDP-CVD. |
Advantages | High-quality coatings, precision, versatility, scalability. |
Applications | Electronics, optics, materials science, protective coatings. |
Challenges | Precursor selection, temperature control, equipment costs, filament degradation. |
Discover how CVD can revolutionize your material synthesis—contact our experts today!