Deposition gases are substances that transition directly from a gaseous state to a solid state without passing through a liquid phase. Common examples include camphor, iodine, ammonium chloride, and naphthalene. In industrial processes like sputtering, inert gases such as argon are typically used due to their stability and efficiency in momentum transfer. For specific applications, neon is preferred for light elements, while heavier elements may require krypton or xenon. Reactive gases are also employed when sputtering compounds. Understanding the properties and applications of these gases is crucial for selecting the appropriate deposition gas for a given process.
Key Points Explained:
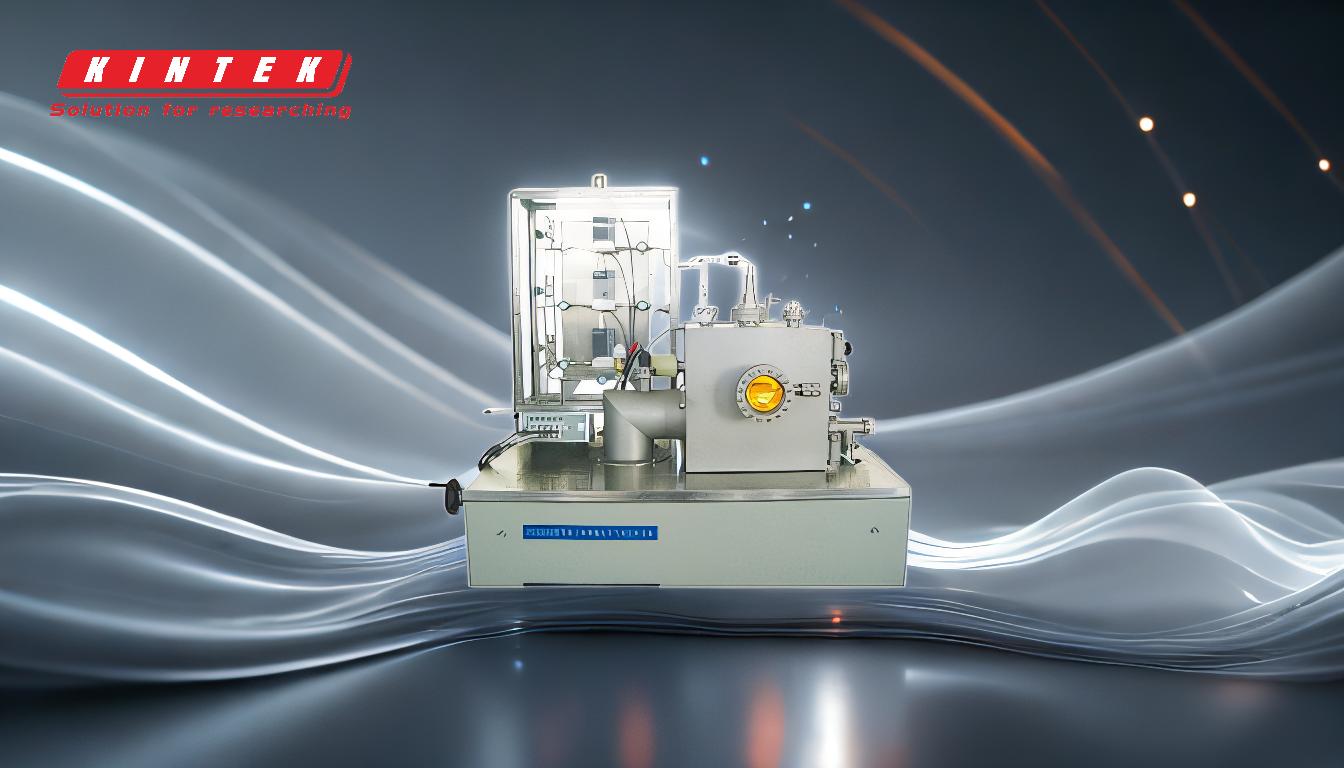
-
Definition of Deposition Gases:
- Deposition gases are substances that transition directly from a gaseous state to a solid state without passing through a liquid phase. This process is known as sublimation.
- Common examples include camphor, iodine, ammonium chloride, and naphthalene.
-
Industrial Applications of Deposition Gases:
- In industrial processes such as sputtering, deposition gases play a critical role.
- Sputtering is a technique used to deposit thin films of materials onto surfaces, commonly used in the manufacturing of semiconductors, optical coatings, and other high-tech applications.
-
Types of Sputtering Gases:
- Inert Gases: Argon is the most commonly used inert gas in sputtering due to its stability and efficiency in momentum transfer.
- Light Elements: Neon is preferred for sputtering light elements because it provides efficient momentum transfer.
- Heavy Elements: Krypton or xenon are used for sputtering heavy elements due to their higher atomic weights, which facilitate better momentum transfer.
- Reactive Gases: These are used when sputtering compounds, as they can react with the target material to form the desired compound on the substrate.
-
Selection Criteria for Deposition Gases:
- Atomic Weight: The atomic weight of the sputtering gas should be close to that of the target material for efficient momentum transfer.
- Reactivity: For compound sputtering, reactive gases are necessary to achieve the desired chemical composition.
- Stability: Inert gases like argon are preferred for their chemical stability, which prevents unwanted reactions during the deposition process.
-
Examples and Practical Considerations:
- Camphor and Iodine: These are classic examples of substances that undergo deposition and are often used in educational demonstrations.
- Ammonium Chloride and Naphthalene: These are also common examples, with naphthalene being widely recognized as mothballs.
- Industrial Use: In semiconductor manufacturing, the choice of deposition gas can significantly affect the quality and properties of the deposited film.
-
Conclusion:
- Understanding the properties and applications of deposition gases is essential for selecting the appropriate gas for a given process.
- The choice of gas can influence the efficiency, quality, and outcome of the deposition process, making it a critical factor in industrial applications.
By considering these key points, one can make informed decisions when selecting deposition gases for various applications, ensuring optimal results in both educational and industrial settings.
Summary Table:
Type | Examples | Applications |
---|---|---|
Inert Gases | Argon | Sputtering for semiconductors, optical coatings |
Light Elements | Neon | Sputtering light elements |
Heavy Elements | Krypton, Xenon | Sputtering heavy elements |
Reactive Gases | Oxygen, Nitrogen | Sputtering compounds to form desired chemical compositions |
Need help selecting the right deposition gas for your process? Contact our experts today!