Deposition in the semiconductor industry is a critical process where materials are deposited at atomic or molecular levels onto a wafer surface to form thin films with specific electrical properties. This process is essential for creating high-performance semiconductor devices. The two primary methods of deposition are Physical Vapor Deposition (PVD) and Chemical Vapor Deposition (CVD). PVD involves the physical transfer of material, while CVD relies on chemical reactions to deposit materials. Advanced techniques like Low Pressure CVD (LPCVD), Plasma Enhanced CVD (PECVD), and Atomic Layer Deposition (ALD) are commonly used. Materials such as aluminum are often deposited to form the main layer of the substrate, while other techniques like HDP-CVD and CVD tungsten are used for secondary layers. The aerosol deposition method is emerging as an alternative, especially for substrates with low melting points or polymers, offering room-temperature processing advantages. Overall, deposition processes are fundamental to the fabrication of high-quality, high-performance semiconductor devices.
Key Points Explained:
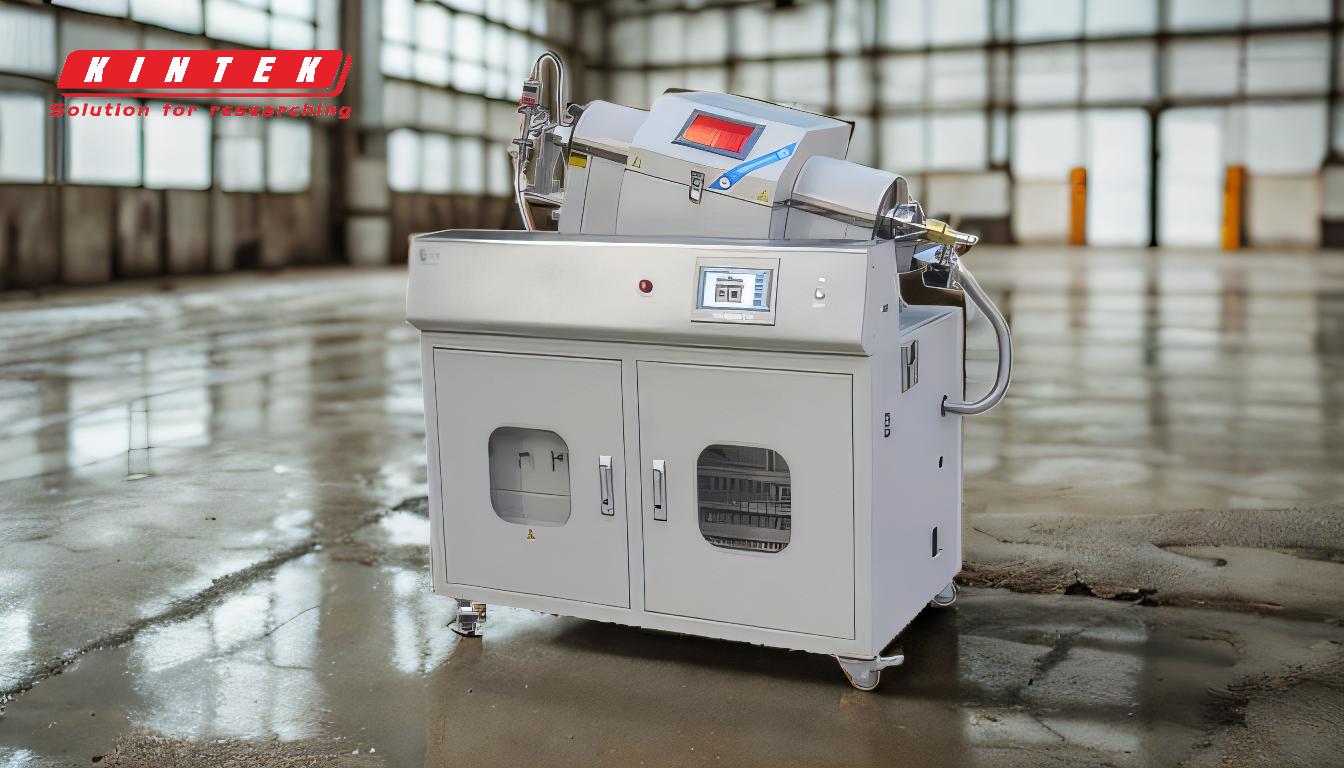
-
Definition of Deposition:
- Deposition in the semiconductor industry refers to the process of depositing materials at atomic or molecular levels onto a wafer surface to create thin films with specific electrical properties. This is crucial for the production of semiconductor devices.
-
Primary Deposition Methods:
- Physical Vapor Deposition (PVD): This method involves the physical transfer of material, typically through processes like evaporation or sputtering. PVD is used to deposit metals and other materials that require precise control over thickness and uniformity.
- Chemical Vapor Deposition (CVD): CVD relies on chemical reactions to deposit materials. It is used for depositing a wide range of materials, including silicon dioxide, silicon nitride, and various metals. CVD processes can be further categorized into techniques like Low Pressure CVD (LPCVD), Plasma Enhanced CVD (PECVD), and Atomic Layer Deposition (ALD).
-
Materials Used in Deposition:
- Aluminum: Often used as the main layer of the substrate due to its excellent electrical conductivity and ease of deposition.
- Secondary Layers: Materials like tungsten, silicon dioxide, and silicon nitride are deposited using specialized techniques such as HDP-CVD, plasma-enhanced CVD, and CVD tungsten.
-
Advanced Deposition Techniques:
- Low Pressure Chemical Vapor Deposition (LPCVD): Operates at reduced pressures to achieve high-quality, uniform films.
- Plasma Enhanced Chemical Vapor Deposition (PECVD): Uses plasma to enhance the chemical reactions, allowing for lower temperature deposition, which is beneficial for temperature-sensitive substrates.
- Atomic Layer Deposition (ALD): Offers precise control over film thickness at the atomic level, making it ideal for applications requiring ultra-thin, uniform layers.
-
Emerging Deposition Techniques:
- Aerosol Deposition Method: An alternative technique particularly useful for substrates with low melting points or polymers. It allows for room-temperature processing, which is advantageous for high-technology semiconductor applications.
-
Applications of Deposition in Semiconductor Fabrication:
- Thin Film Processing: Deposition techniques are used to create thin films that are essential for various electronic devices, including transistors, capacitors, and interconnects.
- High-Quality, High-Performance Materials: The deposition process is key to producing materials with the necessary electrical, thermal, and mechanical properties required for advanced semiconductor devices.
-
Importance of Deposition in Semiconductor Industry:
- Device Performance: The quality of the deposited films directly impacts the performance and reliability of semiconductor devices.
- Manufacturing Efficiency: Advanced deposition techniques improve manufacturing efficiency by allowing for precise control over material properties and film thickness.
In summary, deposition is a fundamental process in the semiconductor industry, enabling the production of high-quality, high-performance materials essential for the fabrication of advanced electronic devices. The choice of deposition method and material depends on the specific requirements of the semiconductor device being produced.
Summary Table:
Aspect | Details |
---|---|
Primary Methods | PVD (Physical Vapor Deposition), CVD (Chemical Vapor Deposition) |
Advanced Techniques | LPCVD, PECVD, ALD |
Common Materials | Aluminum (main layer), Tungsten, Silicon Dioxide, Silicon Nitride |
Emerging Techniques | Aerosol Deposition (room-temperature processing) |
Applications | Thin film processing, transistors, capacitors, interconnects |
Importance | Enhances device performance, improves manufacturing efficiency |
Discover how advanced deposition techniques can optimize your semiconductor production—contact our experts today!