Calcination and sintering are both thermal processes used in metallurgy and material science, but they serve distinct purposes. Calcination primarily involves heating metal ores or other materials to high temperatures to remove volatile components, such as water, carbon dioxide, or other impurities, without melting the material. This process is often used to decompose carbonates, hydroxides, or other compounds into oxides. On the other hand, sintering involves heating powdered metal or ceramic materials to a temperature below their melting point to bond particles together, creating a solid mass with improved mechanical properties. While both processes involve heating, calcination is focused on purification, whereas sintering is focused on consolidation and strengthening.
Key Points Explained:
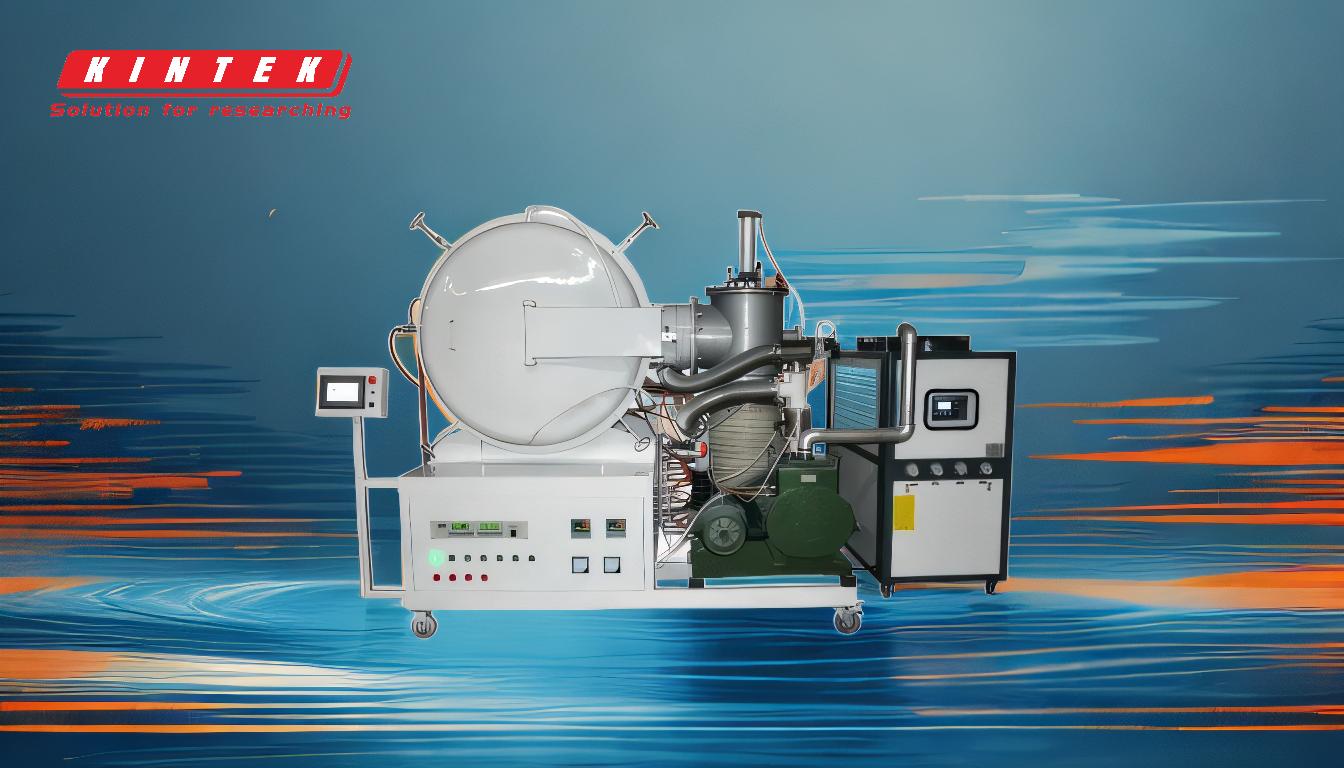
-
Definition and Purpose:
- Calcination: A thermal process where materials, typically metal ores, are heated to high temperatures to remove volatile substances like water, carbon dioxide, or impurities. The goal is to decompose compounds (e.g., carbonates into oxides) and purify the material.
- Sintering: A process where powdered materials, such as metals or ceramics, are heated to a temperature below their melting point to bond particles together. The aim is to create a solid, cohesive structure with enhanced mechanical properties.
-
Temperature Range:
- Calcination: Typically occurs at temperatures high enough to decompose compounds but below the melting point of the material. For example, calcium carbonate decomposes into calcium oxide at around 825°C.
- Sintering: Occurs at temperatures below the melting point of the material but high enough to allow particle bonding through diffusion. The exact temperature depends on the material but is generally lower than calcination temperatures.
-
Chemical vs. Physical Changes:
- Calcination: Primarily involves chemical changes, such as the decomposition of carbonates or hydroxides into oxides, releasing gases like CO₂ or H₂O.
- Sintering: Primarily involves physical changes, such as the bonding of particles through diffusion, leading to densification and improved mechanical strength.
-
Applications:
- Calcination: Used in industries like cement production (to produce lime from limestone), metal refining (to remove impurities from ores), and catalyst preparation (to activate materials by removing volatile components).
- Sintering: Widely used in powder metallurgy to produce metal parts, in ceramic manufacturing to create strong, dense components, and in additive manufacturing (3D printing) to fuse powdered materials.
-
Outcome:
- Calcination: Results in a purified material, often in the form of an oxide, with reduced mass due to the removal of volatile components.
- Sintering: Results in a denser, stronger material with improved mechanical properties, such as hardness, strength, and wear resistance.
-
Material State:
- Calcination: Typically starts with a solid material (e.g., ore or compound) and ends with a solid product after the removal of impurities.
- Sintering: Begins with powdered materials and ends with a solid, cohesive structure after particle bonding.
-
Industrial Significance:
- Calcination: Critical for producing high-purity materials required in various industrial processes, such as steelmaking, glass production, and chemical manufacturing.
- Sintering: Essential for manufacturing components with precise shapes and properties, such as gears, bearings, and cutting tools, particularly in industries like automotive, aerospace, and electronics.
In summary, while both calcination and sintering involve heating materials to high temperatures, they differ in their objectives, mechanisms, and outcomes. Calcination is a purification process focused on removing impurities and decomposing compounds, whereas sintering is a consolidation process aimed at bonding particles to create strong, dense materials. Understanding these differences is crucial for selecting the appropriate process for specific industrial applications.
Summary Table:
Aspect | Calcination | Sintering |
---|---|---|
Purpose | Purification by removing volatile components (e.g., water, CO₂) | Consolidation and strengthening by bonding particles |
Temperature Range | High enough to decompose compounds (e.g., 825°C for CaCO₃) | Below melting point to allow particle bonding |
Changes | Chemical (decomposition of compounds) | Physical (particle bonding and densification) |
Applications | Cement production, metal refining, catalyst preparation | Powder metallurgy, ceramic manufacturing, additive manufacturing (3D printing) |
Outcome | Purified material (e.g., oxides) with reduced mass | Denser, stronger material with improved mechanical properties |
Material State | Starts and ends as solid | Starts as powder, ends as solid cohesive structure |
Industrial Use | Steelmaking, glass production, chemical manufacturing | Automotive, aerospace, electronics industries |
Need help choosing the right thermal process for your application? Contact our experts today!