Furnace brazing is a highly controlled metal-joining process where a filler metal is heated above its melting point and distributed between two or more close-fitting parts by capillary action. This process is particularly advantageous in industrial applications due to its ability to produce strong, clean, and precise joints. Vacuum brazing, a specialized form of furnace brazing, is conducted under vacuum conditions to prevent oxidation and contamination, making it ideal for high-precision industries like aerospace and metallurgical research. The process involves sophisticated equipment, such as a vacuum brazing furnace, which ensures uniform heating and precise temperature control, critical for achieving high-quality brazed joints.
Key Points Explained:
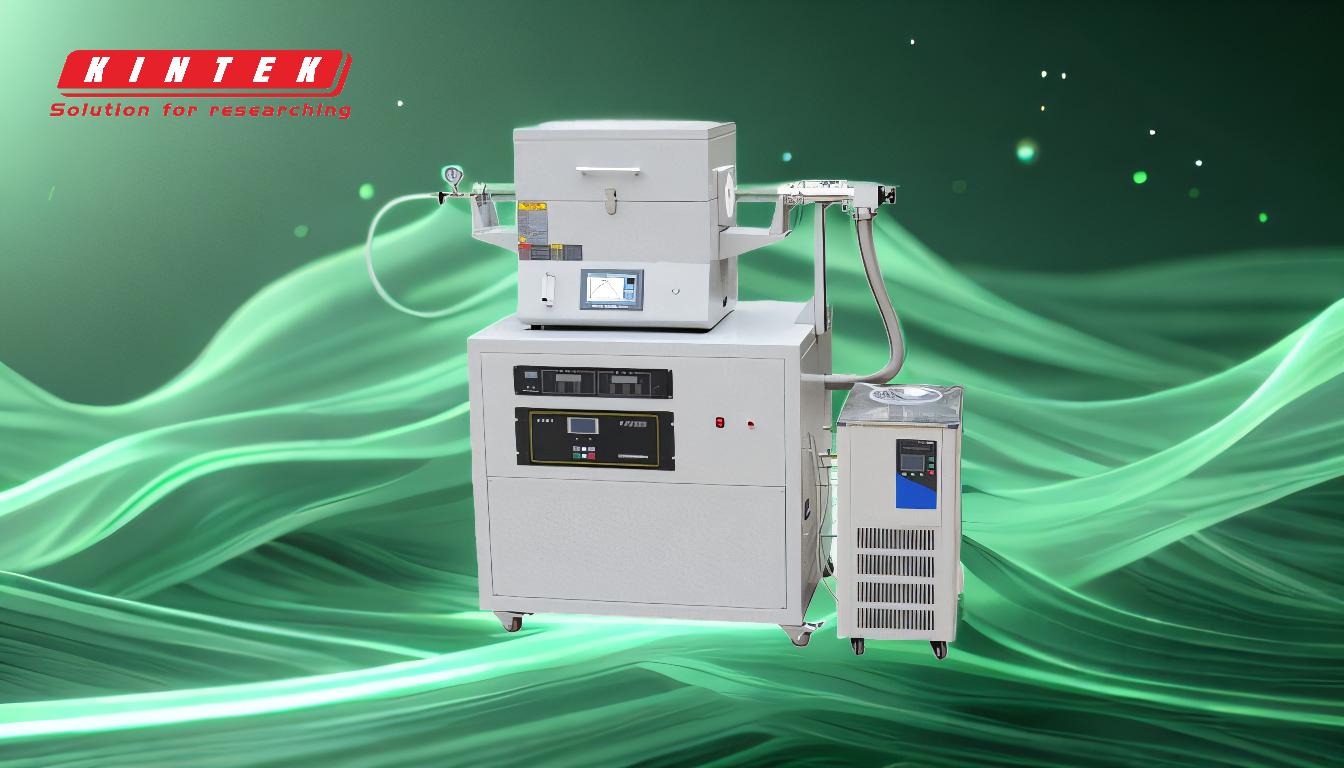
-
Definition and Process of Furnace Brazing:
- Furnace brazing is an industrial technique where metallic materials are joined using a molten filler metal. The filler metal, which has a lower melting point than the base metals, flows into the joint through capillary action, creating a strong bond upon cooling.
- This method is suitable for high-volume production and is widely used in industries requiring precise and repeatable results.
-
Vacuum Brazing and Its Advantages:
- Vacuum brazing is a subset of furnace brazing conducted in a vacuum environment. This eliminates the need for flux, prevents oxidation, and ensures contamination-free joints.
- The process is ideal for joining unweldable materials and producing parts with minimal distortion. It is extensively used in aerospace, particle physics, and metallurgical research due to its precision and reliability.
-
Key Features of a Vacuum Brazing Furnace:
- A vacuum brazing furnace ensures high temperature uniformity, enabling consistent heating cycles for multiple loads or large assemblies.
- It operates at temperatures higher than oxide formation, allowing oxidized workpieces to lose their oxide layer before brazing.
- The furnace can recognize workpieces via barcode-linked cycle programs, ensuring precise and repeatable heating cycles for each piece.
-
Components and Operation of a Vacuum Brazing Furnace:
- The furnace consists of a vacuum system (including vacuum valves, mechanical pumps, diffusion pumps, and Roots pumps) and a heating system.
- The vacuum system reduces the pressure inside the chamber to below atmospheric pressure, preventing oxidation and decarburization of the workpiece surface.
- The heating system melts the brazing material, and the process is automatically controlled by a temperature control instrument.
-
Steps in the Vacuum Brazing Process:
- The assembled workpiece is placed in the vacuum chamber.
- The mechanical vacuum pump is started, followed by the diffusion pump once a certain vacuum level is achieved.
- The workpiece is heated while maintaining the vacuum, and the brazing material melts and flows into the joint.
- After brazing, the workpiece is cooled to a safe temperature before removal to avoid oxidation.
-
Benefits of Vacuum Brazing:
- Eliminates part distortion and thermal stress.
- Joins materials that are difficult or impossible to weld.
- Produces smooth, dense brazing seams with excellent mechanical properties.
- Reduces production cycles, costs, and environmental impact by eliminating the need for flux and expensive fixtures.
-
Applications of Vacuum Brazing:
- Aerospace: Used for joining critical components that require high strength and precision.
- Particle Physics: Ideal for creating complex assemblies with minimal contamination.
- Metallurgical Research: Enables the study of material properties under controlled conditions.
By leveraging the capabilities of a vacuum brazing furnace, industries can achieve high-quality, reliable, and repeatable brazed joints, making it a cornerstone of modern manufacturing and research.
Summary Table:
Aspect | Details |
---|---|
Definition | A metal-joining process using a molten filler metal via capillary action. |
Key Advantages | Produces strong, clean, and precise joints; suitable for high-volume production. |
Vacuum Brazing Benefits | Prevents oxidation, eliminates flux, and ensures contamination-free joints. |
Applications | Aerospace, particle physics, metallurgical research. |
Equipment | Uses vacuum brazing furnaces for uniform heating and precise temperature control. |
Interested in enhancing your industrial processes with furnace brazing? Contact us today to learn more!