Induction heating is a highly efficient and precise method of heating conductive materials using electromagnetic induction. It requires a combination of key components and understanding of the underlying principles to ensure effective operation. The essential elements include an RF power supply to generate alternating current, a copper coil (inductor) to create an alternating magnetic field, and the material to be heated. Additional components like a chiller, vacuum unit, and cooling systems are often necessary to maintain optimal conditions. The process relies on eddy currents and hysteresis losses to generate heat within the material, making it suitable for applications such as metal melting and alloy creation.
Key Points Explained:
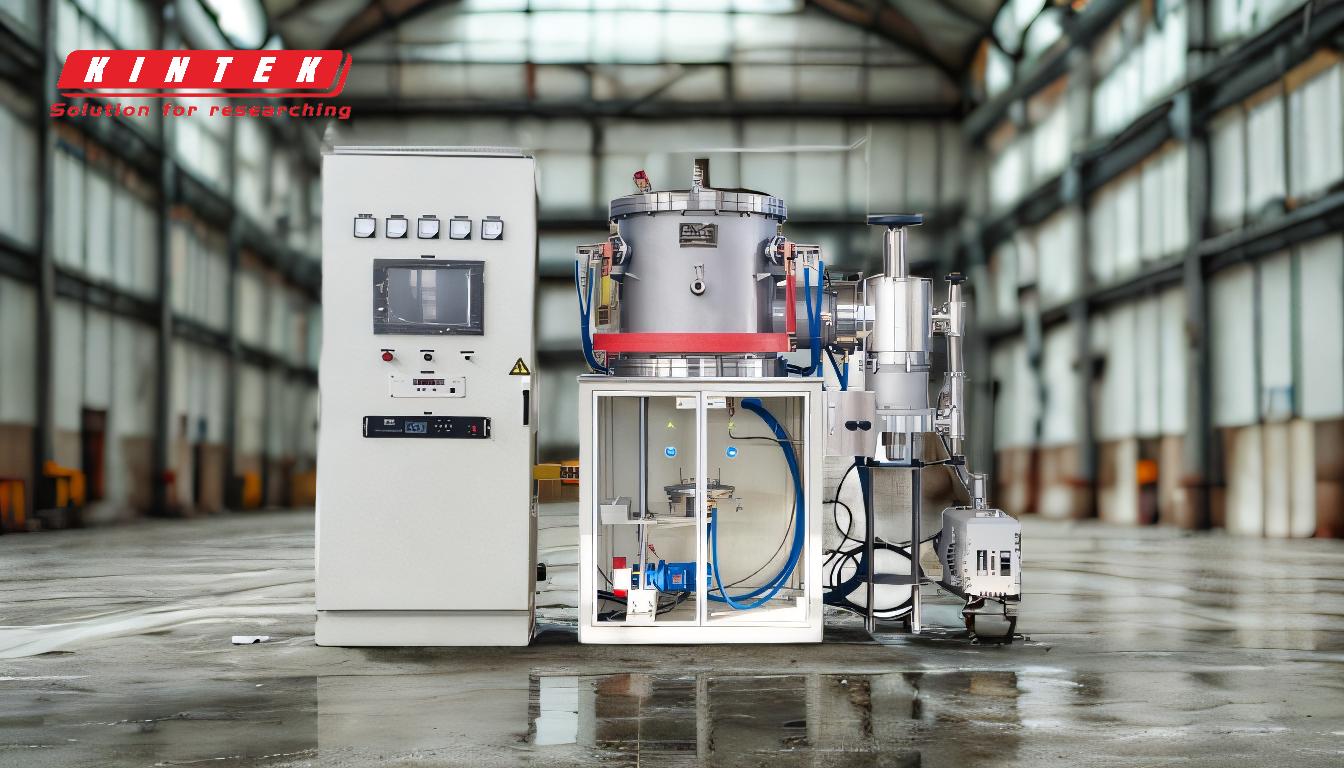
-
RF Power Supply:
- The RF power supply is the heart of the induction heating system. It provides the alternating current (AC) required to generate the alternating magnetic field.
- The frequency of the AC current can vary depending on the application, with higher frequencies typically used for smaller or more precise heating tasks.
- The power supply must be capable of delivering sufficient power to achieve the desired heating effect without overheating or damaging the system.
-
Induction Coil (Inductor):
- The induction coil, usually made of copper, is responsible for generating the alternating magnetic field when AC current flows through it.
- The design of the coil (e.g., shape, size, and number of turns) is critical to ensure efficient heat generation in the target material.
- Proper cooling of the coil is essential to prevent overheating and maintain system performance.
-
Material to be Heated:
- The material must be conductive (e.g., metals) to allow the induction of eddy currents, which generate heat through resistance.
- Magnetic materials also experience hysteresis losses, contributing to the heating process.
- The size, shape, and properties of the material influence the efficiency and uniformity of heating.
-
Chiller System:
- A chiller is used to cool the induction coil and other components of the system to prevent overheating and ensure consistent operation.
- Cooling is particularly important in high-power applications or when the system operates for extended periods.
-
Vacuum Unit (if applicable):
- In some applications, a vacuum unit is used to create a controlled environment, reducing oxidation and contamination during the heating process.
- This is especially important in processes like metal melting or alloy creation, where purity and quality are critical.
-
Eddy Currents and Hysteresis Losses:
- Eddy currents are induced in the conductive material by the alternating magnetic field, generating heat due to electrical resistance.
- Hysteresis losses occur in magnetic materials, where the repeated alignment and realignment of magnetic domains during the alternating magnetic field cycle produce heat.
- These two mechanisms work together to heat the material efficiently and uniformly.
-
Control and Monitoring Systems:
- Modern induction heating systems often include sensors and control systems to monitor and adjust parameters like temperature, power output, and cooling rates.
- These systems ensure precision and repeatability in industrial applications.
-
Applications of Induction Heating:
- Induction heating is widely used in industries such as metalworking, automotive, aerospace, and electronics for tasks like melting, hardening, brazing, and annealing.
- Its ability to provide localized and controlled heating makes it ideal for precision applications.
In summary, an induction heating system requires a well-coordinated setup of components, including an RF power supply, induction coil, chiller, and optional vacuum unit. Understanding the principles of electromagnetic induction, eddy currents, and hysteresis losses is crucial for optimizing the system's performance. With proper design and control, induction heating offers a versatile and efficient solution for a wide range of industrial heating applications.
Summary Table:
Component | Role |
---|---|
RF Power Supply | Generates alternating current for the magnetic field. |
Induction Coil | Creates an alternating magnetic field to heat conductive materials. |
Material to be Heated | Must be conductive; eddy currents and hysteresis losses generate heat. |
Chiller System | Cools the coil and system to prevent overheating. |
Vacuum Unit (if needed) | Reduces oxidation and contamination in controlled environments. |
Control Systems | Monitors and adjusts temperature, power, and cooling for precision. |
Applications | Metal melting, hardening, brazing, annealing, and more. |
Ready to optimize your industrial heating process? Contact us today to learn more about induction heating solutions!