Physical chemical vapor deposition (PCVD) is a hybrid process that combines principles from both physical vapor deposition (PVD) and chemical vapor deposition (CVD). It involves the use of physical methods to vaporize a source material, followed by chemical reactions to deposit a thin film onto a substrate. This process leverages the advantages of both PVD and CVD, such as high-quality film deposition, precise control over film properties, and the ability to create complex coatings. PCVD is widely used in industries like semiconductors, optics, and coatings for its ability to produce durable, high-performance materials.
Key Points Explained:
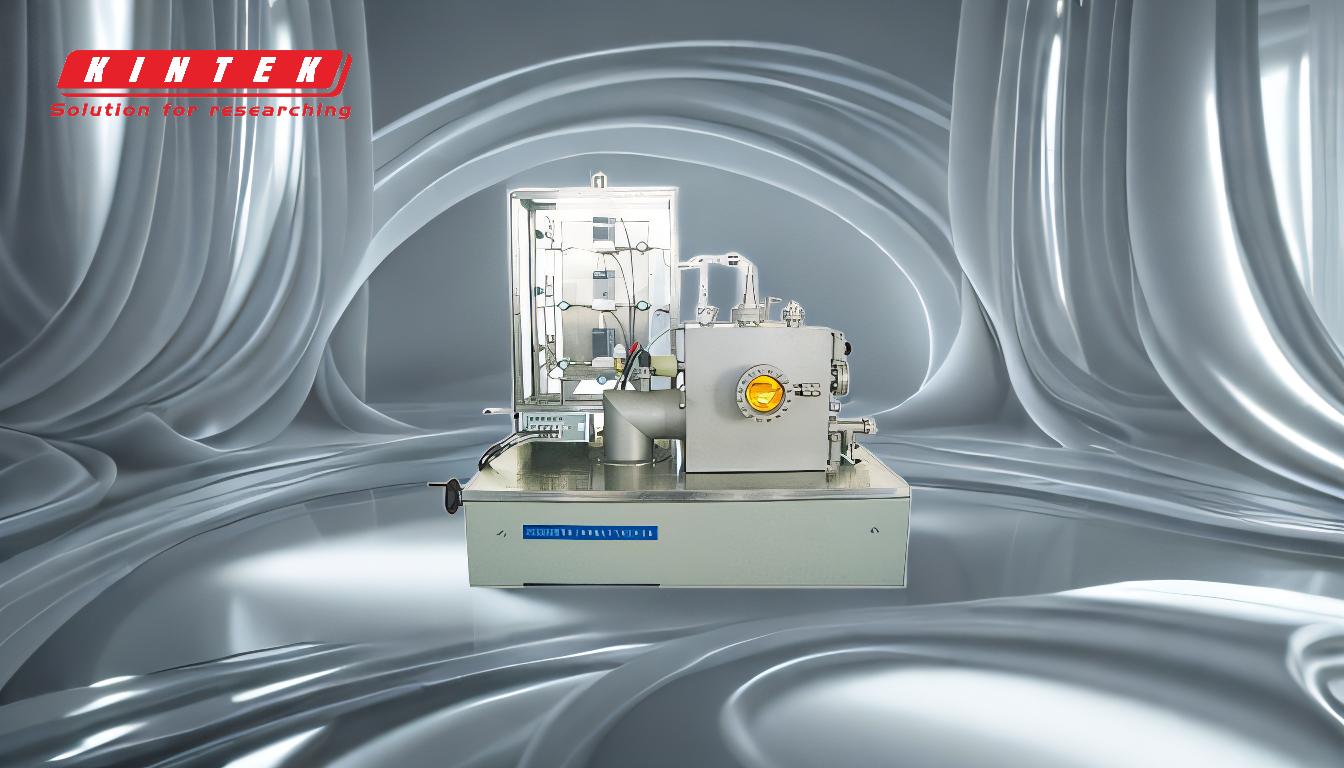
-
Definition of Physical Chemical Vapor Deposition (PCVD):
- PCVD is a hybrid thin-film deposition technique that integrates physical and chemical processes.
- It begins with the physical vaporization of a source material (similar to PVD) and then involves chemical reactions (similar to CVD) to deposit the material onto a substrate.
- This combination allows for the creation of high-quality, uniform, and durable thin films.
-
Key Components of PCVD:
- Source Material: Typically a solid or liquid precursor that is vaporized using physical methods like sputtering or evaporation.
- Reaction Chamber: A controlled environment where the vaporized material undergoes chemical reactions to form the desired coating.
- Substrate: The surface onto which the thin film is deposited, often requiring specific preparation to ensure proper adhesion.
- Reactive Gases: Gases introduced into the chamber to facilitate chemical reactions during the deposition process.
-
Process Steps in PCVD:
- Vaporization: The source material is vaporized using physical methods such as sputtering, thermal evaporation, or laser ablation.
- Transport: The vaporized material is transported to the substrate in a controlled environment, often under vacuum or inert gas conditions.
- Chemical Reaction: Reactive gases are introduced, causing the vaporized material to undergo chemical reactions, forming a thin film on the substrate.
- Deposition: The chemically reacted material deposits onto the substrate, creating a uniform and adherent coating.
- By-product Removal: Volatile by-products are removed from the chamber to maintain the purity and quality of the deposited film.
-
Advantages of PCVD:
- High-Quality Films: PCVD produces films with excellent uniformity, density, and adhesion.
- Versatility: It can deposit a wide range of materials, including metals, ceramics, and polymers.
- Precision: The process allows for precise control over film thickness, composition, and microstructure.
- Complex Coatings: PCVD can create multi-layered or composite coatings with tailored properties.
-
Applications of PCVD:
- Semiconductors: Used for depositing thin films in the fabrication of integrated circuits and microelectronics.
- Optics: Applied in the production of anti-reflective coatings, mirrors, and optical filters.
- Wear-Resistant Coatings: Used to enhance the durability of tools, cutting instruments, and mechanical components.
- Biomedical Devices: Employed to create biocompatible coatings on implants and medical instruments.
-
Comparison with PVD and CVD:
- PVD: Relies solely on physical processes (e.g., sputtering, evaporation) to deposit materials. It is limited in its ability to create complex chemical compositions.
- CVD: Uses chemical reactions to deposit materials but often requires high temperatures and specific precursor gases.
- PCVD: Combines the strengths of both PVD and CVD, offering greater flexibility and control over the deposition process.
-
Challenges and Considerations:
- Complexity: PCVD requires precise control over both physical and chemical parameters, making the process more complex than PVD or CVD alone.
- Cost: The equipment and materials for PCVD can be expensive, particularly for large-scale applications.
- Safety: Handling reactive gases and high-temperature processes requires strict safety protocols.
-
Future Trends in PCVD:
- Nanotechnology: PCVD is increasingly used to deposit nanomaterials with unique properties for advanced applications.
- Sustainability: Efforts are being made to develop eco-friendly precursors and reduce energy consumption in PCVD processes.
- Automation: Advances in automation and process control are improving the efficiency and reproducibility of PCVD.
In summary, physical chemical vapor deposition is a sophisticated and versatile technique that combines the best aspects of PVD and CVD to produce high-performance thin films. Its applications span multiple industries, and ongoing advancements are expanding its capabilities and efficiency.
Summary Table:
Aspect | Details |
---|---|
Definition | Hybrid thin-film deposition combining physical and chemical processes. |
Key Components | Source material, reaction chamber, substrate, reactive gases. |
Process Steps | Vaporization, transport, chemical reaction, deposition, by-product removal. |
Advantages | High-quality films, versatility, precision, ability to create complex coatings. |
Applications | Semiconductors, optics, wear-resistant coatings, biomedical devices. |
Comparison with PVD/CVD | Combines strengths of both, offering greater flexibility and control. |
Challenges | Complexity, cost, safety considerations. |
Future Trends | Nanotechnology, sustainability, automation. |
Interested in leveraging PCVD for your applications? Contact us today to learn more!