Physical vapor deposition (PVD) equipment is a specialized system used to deposit thin films of material onto a substrate through a physical process. This involves converting a solid precursor material into a vapor phase, typically using high-energy methods such as electrical discharge or laser ablation, and then condensing the vapor onto a substrate to form a thin, uniform coating. PVD is widely used in industries such as semiconductors, aerospace, biomedical, and manufacturing of cutting tools and decorative coatings. The process is known for producing durable, high-performance films with excellent adhesion and the ability to handle materials with high melting points. PVD equipment includes components like vacuum chambers, target materials, substrate holders, and monitoring systems to control film thickness and quality.
Key Points Explained:
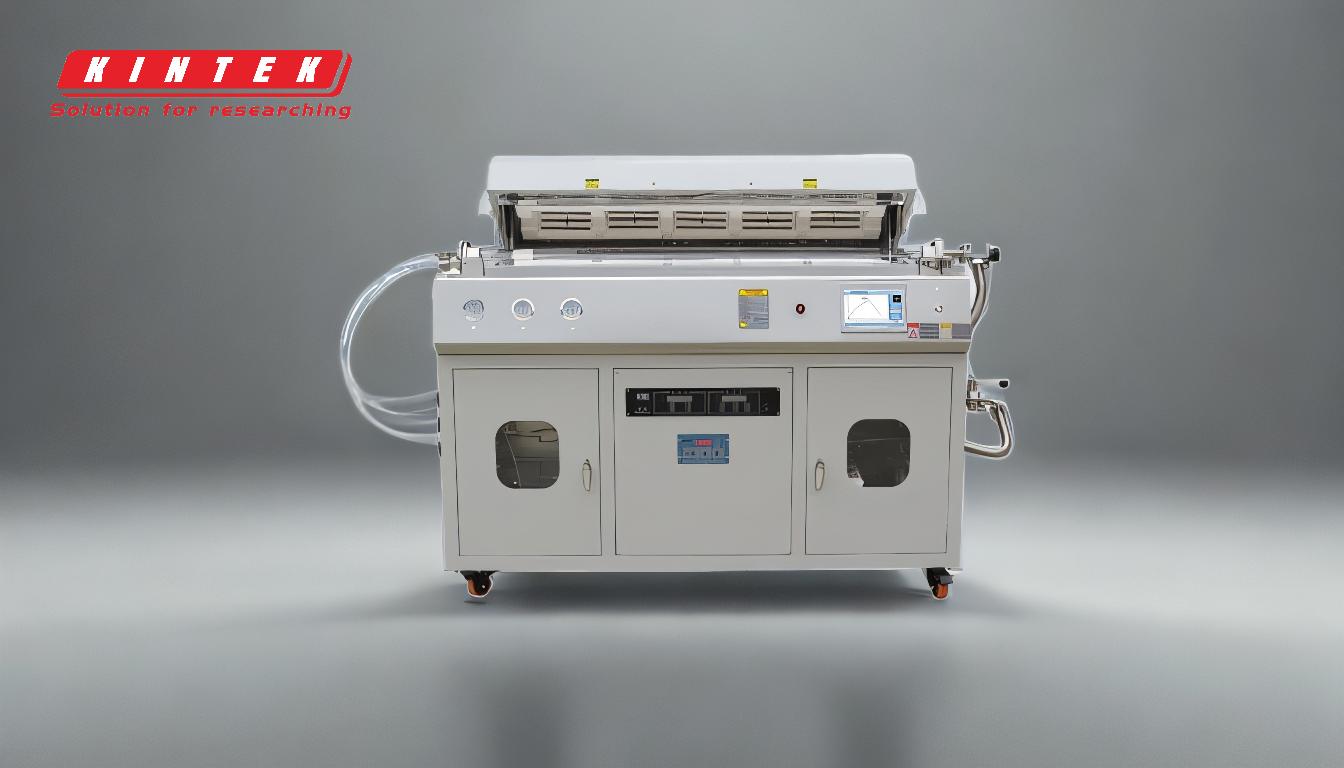
-
Definition and Purpose of PVD Equipment:
- PVD equipment is designed to deposit thin films of material onto a substrate using a physical process.
- It is used to create coatings with specific mechanical, optical, chemical, or electronic properties.
- Applications include semiconductor devices, cutting tools, decorative coatings, and biomedical implants.
-
Core Components of PVD Equipment:
- Vacuum Chamber: Provides a controlled environment with low pressure to minimize contamination and unwanted chemical reactions.
- Target Material: The solid precursor material that is vaporized to form the thin film.
- Substrate Holder: Holds the material to be coated and ensures uniform deposition.
- Energy Source: High-power electricity, lasers, or other methods to vaporize the target material.
- Monitoring Systems: Quartz crystal rate monitors or other sensors to control film thickness and deposition rate.
-
How PVD Works:
- The target material is vaporized using high-energy methods such as thermal evaporation, sputtering, or laser ablation.
- The vaporized atoms travel through the vacuum chamber and condense onto the substrate.
- The process is controlled to ensure precise thickness and uniformity of the deposited film.
-
Types of PVD Techniques:
- Thermal Evaporation: The target material is heated until it vaporizes and then condenses on the substrate.
- Sputtering: High-energy ions bombard the target material, dislodging atoms that then deposit onto the substrate.
- Laser Ablation: A laser is used to vaporize the target material, which then deposits onto the substrate.
-
Advantages of PVD:
- Produces thin films with excellent adhesion and durability.
- Suitable for materials with high melting points.
- Creates corrosion-resistant and high-temperature-tolerant coatings.
- Enables precise control over film thickness and composition.
-
Applications of PVD Equipment:
- Semiconductors: Used to create thin films for solar panels, microchips, and other electronic components.
- Cutting Tools: Coating tools with materials like titanium nitride to enhance durability and performance.
- Aerospace: Producing coatings that withstand extreme conditions.
- Biomedical: Creating biocompatible coatings for implants and medical devices.
- Decorative Coatings: Applying durable and aesthetically pleasing finishes to consumer products.
-
Considerations for Purchasing PVD Equipment:
- Material Compatibility: Ensure the equipment can handle the specific target materials and substrates required for your application.
- Film Quality: Look for systems with advanced monitoring and control features to achieve the desired film properties.
- Scalability: Consider whether the equipment can meet production volume requirements.
- Cost and Maintenance: Evaluate the initial investment and ongoing maintenance needs.
By understanding these key points, potential buyers can make informed decisions about selecting PVD equipment that meets their specific needs and applications.
Summary Table:
Aspect | Details |
---|---|
Purpose | Deposits thin films onto substrates for coatings with specific properties. |
Core Components | Vacuum chamber, target material, substrate holder, energy source, monitoring systems. |
Techniques | Thermal evaporation, sputtering, laser ablation. |
Advantages | Excellent adhesion, durability, corrosion resistance, precise control. |
Applications | Semiconductors, cutting tools, aerospace, biomedical, decorative coatings. |
Buying Considerations | Material compatibility, film quality, scalability, cost, and maintenance. |
Ready to enhance your production with PVD equipment? Contact us today to find the perfect solution for your needs!