Plasma discharge sintering, also known as spark plasma sintering (SPS) or plasma activation sintering, is a rapid sintering process that combines plasma activation, hot pressing, and resistance heating. It involves applying a pulsed direct current (DC) and uniaxial pressure to powder within a die, generating plasma discharge between particles. This process rapidly heats and sinters the material, evaporating impurities and activating particle surfaces. The technology is characterized by fast heating rates, low sintering temperatures, short processing times, and the ability to produce materials with high density and fine, uniform grains. It is widely used for sintering metals, ceramics, nanostructured materials, and composites, making it ideal for research and development of new materials.
Key Points Explained:
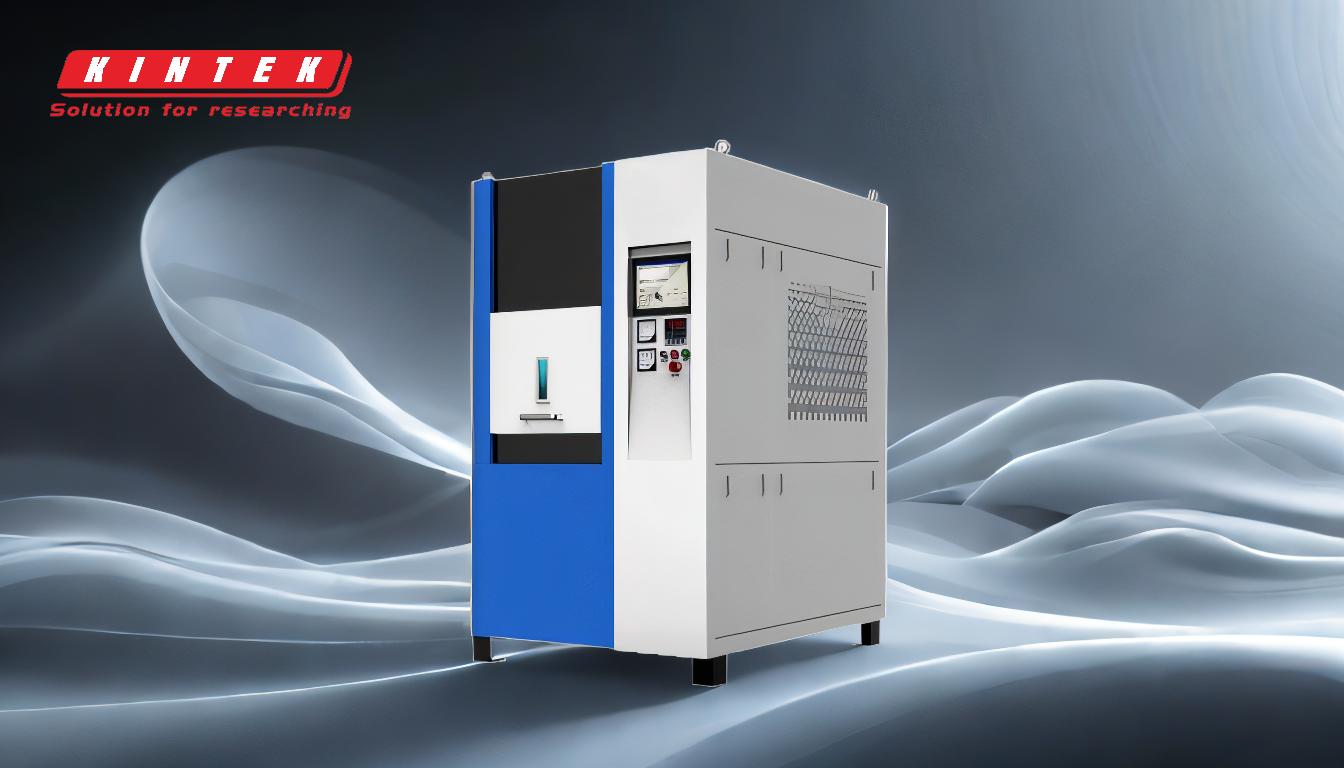
-
Principle of Plasma Discharge Sintering:
- A pulsed DC current is applied to the powder, creating micro-discharges between particles.
- These discharges generate plasma, which rapidly heats the material and evaporates surface impurities like oxide films and absorbed gases.
- The particle surfaces are activated through heat and strain energy accumulation, facilitating sintering.
-
Mechanism of Sintering:
- Joule heat is generated at the contact points of activated particles, causing thermal diffusion.
- Electrical diffusion occurs in parallel due to the applied voltage, enabling sintering to complete in a short time (seconds to minutes).
- High-energy sparks can reach temperatures of up to 10,000°C, melting and fusing particles to form dense structures.
-
Advantages of Plasma Discharge Sintering:
- Fast Heating and Cooling: The process is much faster than traditional sintering methods.
- Low Sintering Temperature: Achieves high-density materials at lower temperatures.
- Short Processing Time: Sintering can be completed in minutes.
- Fine and Uniform Grain Structure: Produces materials with superior mechanical properties.
-
Applications:
- Suitable for sintering metals, ceramics, nanostructured materials, amorphous alloys, and composites.
- Ideal for research and development of new materials, including solid electrolytes and electric thermal materials.
- Used to prepare nanomaterials, bulk amorphous alloys, gradient functional materials, and high-density ceramics.
-
Equipment and Process Parameters:
- Spark Plasma Sintering Furnaces are used for this process.
- Operates at low temperatures (500–1000°C) and high pressures (500–1000 MPa) or high temperatures (1000–2000°C) and low pressures (20–30 MPa).
- Can achieve material densities exceeding 99%.
-
Material Suitability:
- Effective for a wide range of materials, including refractory materials like diamond, cemented carbide, and intermetallic compounds.
- Particularly useful for small-scale production and research due to its versatility and efficiency.
-
Unique Features:
- Combines plasma activation, hot pressing, and resistance heating in a single process.
- Enables rapid prototyping and development of advanced materials with tailored properties.
Plasma discharge sintering is a cutting-edge technology that addresses the limitations of traditional sintering methods, offering faster, more efficient, and higher-quality material processing. Its versatility and ability to produce high-performance materials make it a valuable tool in both industrial and research settings.
Summary Table:
Aspect | Details |
---|---|
Principle | Pulsed DC current generates plasma, evaporates impurities, activates particles. |
Mechanism | Joule heat and electrical diffusion enable rapid sintering in minutes. |
Advantages | Fast heating, low sintering temperatures, short processing, fine grain structure. |
Applications | Metals, ceramics, nanostructured materials, composites, and R&D. |
Equipment | Spark Plasma Sintering Furnaces (500–2000°C, 20–1000 MPa). |
Material Suitability | Refractory materials, diamond, cemented carbide, intermetallic compounds. |
Unique Features | Combines plasma activation, hot pressing, and resistance heating. |
Unlock the potential of plasma discharge sintering for your material research—contact our experts today!