Magnetron sputtering is a highly efficient physical vapor deposition (PVD) technique that utilizes magnetic fields to control the behavior of charged particles, particularly ions, in a plasma. This process occurs in a high-vacuum environment where argon gas is ionized to create a plasma. Positive argon ions are accelerated toward a negatively charged target material, causing atoms to be ejected from the target and deposited onto a substrate, forming a thin film. The inclusion of a magnetic field increases plasma density, enhancing the deposition rate and protecting the substrate from excessive ion bombardment. This method is widely used for creating insulating or metallic coatings for optical, electrical, and other industrial applications.
Key Points Explained:
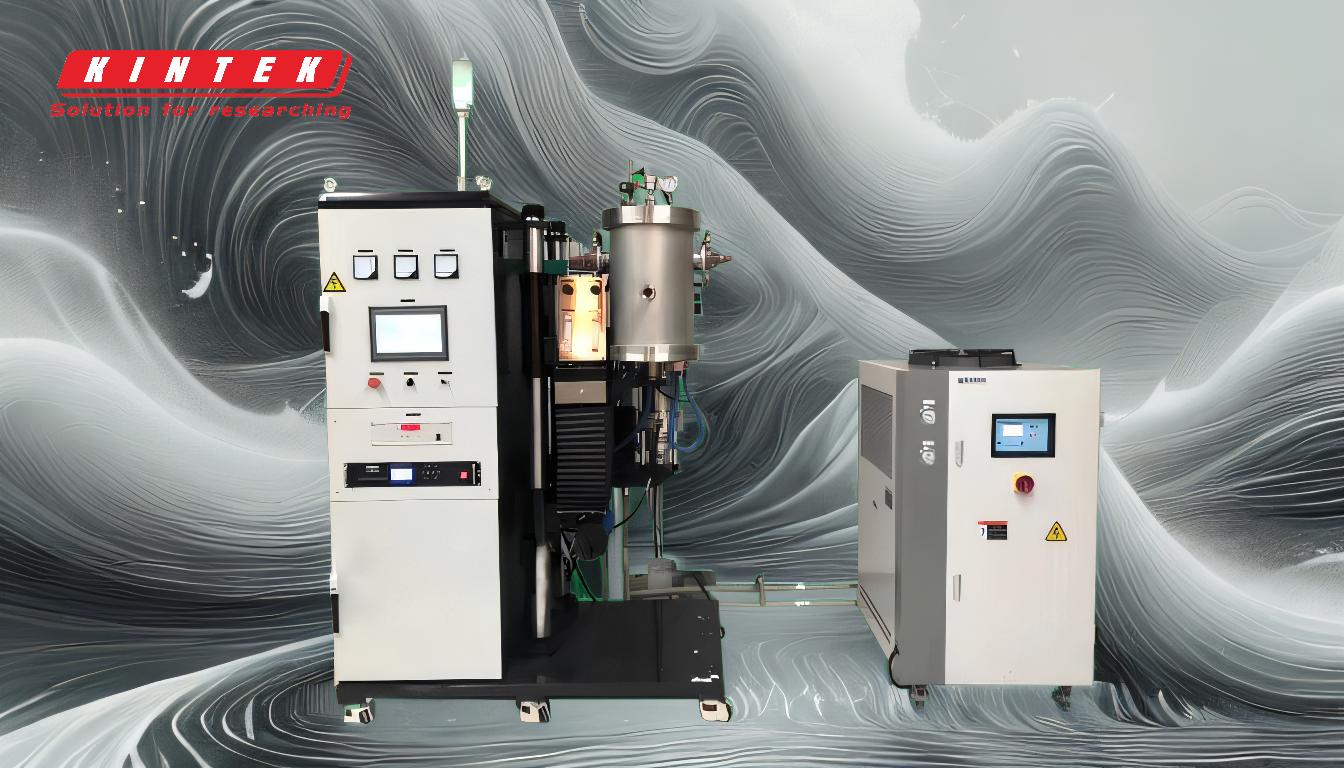
-
Basic Principle of Magnetron Sputtering:
- Magnetron sputtering is a type of physical vapor deposition (PVD) that uses magnetic fields to confine and control the plasma. The process involves ionizing argon gas in a high-vacuum chamber, creating a plasma of positively charged argon ions.
- These ions are attracted to a negatively charged target material, where they collide with the target surface, causing atoms to be ejected (sputtered). These ejected atoms then travel through the vacuum and deposit onto a substrate, forming a thin film.
-
Role of Magnetic Fields:
- The magnetic field in magnetron sputtering is orthogonal to the electric field on the target surface. This configuration traps electrons near the target, increasing the density of the plasma.
- The enhanced plasma density leads to a higher rate of ion collisions with the target, significantly improving the deposition rate compared to traditional sputtering methods.
-
Advantages Over Dipole Sputtering:
- Magnetron sputtering was developed to address the limitations of dipole sputtering, such as low deposition rates and inefficient plasma dissociation.
- The magnetic confinement of the plasma allows for better control over the deposition process, enabling the use of a wide range of target materials, including metals, alloys, and compounds.
-
Process Details:
- A high negative voltage (typically −300 V or more) is applied to the target, attracting positive ions from the plasma. When these ions collide with the target surface, they transfer kinetic energy to the target atoms.
- If the transferred energy exceeds the binding energy of the target atoms, collision cascades occur, leading to the ejection of atoms from the target surface. This process is known as sputtering.
-
Applications:
- Magnetron sputtering is widely used in industries requiring thin-film coatings, such as optics (anti-reflective coatings), electronics (conductive layers), and wear-resistant coatings.
- The ability to co-sputter multiple targets or introduce reactive gases allows for the deposition of complex compound films, expanding its utility in advanced material science.
-
Benefits of Plasma Confinement:
- The magnetic confinement of the plasma not only increases the deposition rate but also protects the substrate from excessive ion bombardment, which can damage delicate materials.
- This makes magnetron sputtering suitable for depositing high-quality thin films on sensitive substrates, such as semiconductors or optical components.
-
Versatility in Material Deposition:
- Magnetron sputtering can deposit a wide variety of materials, including metals, ceramics, and polymers. The process can also be adapted to deposit multi-layer or composite films by adjusting the target materials and process parameters.
- The addition of reactive gases, such as oxygen or nitrogen, enables the formation of compound films (e.g., oxides or nitrides), further broadening its application scope.
By leveraging magnetic fields to control plasma behavior, magnetron sputtering offers a highly efficient and versatile method for thin-film deposition, making it a cornerstone technology in modern material science and industrial applications.
Summary Table:
Aspect | Details |
---|---|
Process Type | Physical Vapor Deposition (PVD) |
Key Mechanism | Magnetic fields control plasma behavior, increasing deposition efficiency. |
Primary Gas Used | Argon (ionized to create plasma) |
Target Materials | Metals, alloys, ceramics, polymers, and compounds |
Applications | Optical coatings, electronics, wear-resistant layers, and more |
Benefits | High deposition rates, substrate protection, and versatility in materials |
Discover how magnetron sputtering can revolutionize your thin-film processes—contact our experts today!