Plasma melting is an advanced metallurgical process that uses plasma, an ionized gas, to achieve extremely high temperatures capable of melting metals and alloys. This technique is particularly useful for processing refractory metals, superalloys, and other materials that require precise control over temperature and composition. Plasma melting is widely used in industries such as aerospace, electronics, and advanced manufacturing, where high-purity materials and specific material properties are critical. The process involves generating plasma using an electric arc or other energy sources, which then heats the material to its melting point, ensuring uniform liquefaction and enabling precise control over the final product's properties.
Key Points Explained:
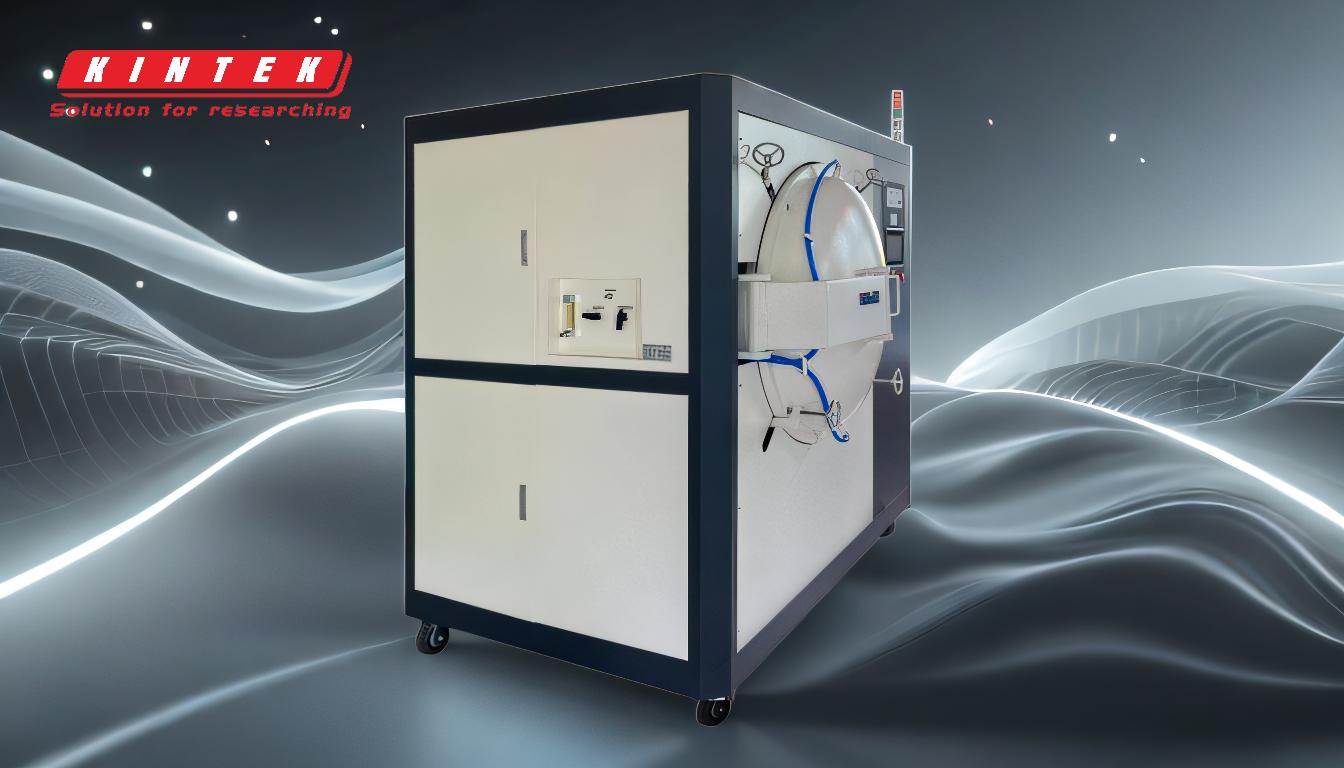
-
What is Plasma Melting?
- Plasma melting is a high-temperature process that uses plasma, an ionized gas, to melt metals and alloys. The plasma is generated by passing an electric current through a gas, creating a high-energy state capable of reaching temperatures up to 20,000°C. This makes it suitable for melting even the most refractory materials, such as tungsten and molybdenum.
-
How Does Plasma Melting Work?
- The process involves creating a plasma arc using an electrode and a gas (often argon or helium). The arc ionizes the gas, forming plasma, which is then directed toward the material to be melted. The intense heat from the plasma rapidly liquefies the material, allowing for precise control over the melting process.
-
Applications of Plasma Melting
- Plasma melting is used in industries requiring high-purity materials, such as aerospace (for superalloys), electronics (for semiconductors), and advanced manufacturing (for refractory metals). It is also employed in recycling precious metals and producing specialized alloys with unique properties.
-
Advantages of Plasma Melting
- High Precision: The process allows for precise control over temperature and composition, ensuring consistent material properties.
- Versatility: It can melt a wide range of materials, including those with extremely high melting points.
- Purity: Plasma melting minimizes contamination, making it ideal for producing high-purity metals and alloys.
-
Challenges and Considerations
- Energy Consumption: Plasma melting requires significant energy input, making it costly for large-scale applications.
- Equipment Complexity: The process involves sophisticated equipment, such as plasma torches and vacuum chambers, which require regular maintenance.
- Material Limitations: While versatile, plasma melting may not be suitable for all materials, particularly those sensitive to high temperatures or reactive gases.
-
Comparison with Other Melting Techniques
- Unlike traditional methods like induction melting or arc melting, plasma melting offers superior control over temperature and atmosphere. This makes it ideal for applications requiring high purity and precise material properties. However, it is generally more expensive and complex than conventional methods.
By leveraging the unique properties of plasma, this melting technique enables the production of advanced materials with tailored properties, making it a cornerstone of modern metallurgy and materials science.
Summary Table:
Aspect | Details |
---|---|
Process | Uses plasma (ionized gas) to achieve temperatures up to 20,000°C. |
Applications | Aerospace, electronics, advanced manufacturing, and precious metal recycling. |
Advantages | High precision, versatility, and minimal contamination. |
Challenges | High energy consumption, complex equipment, and material limitations. |
Comparison | Superior control vs. traditional methods, but more expensive and complex. |
Learn how plasma melting can revolutionize your material processing—contact our experts today!