Pressing dies are specialized tools used in manufacturing processes to shape or cut materials into specific forms. They are commonly employed in industries such as metalworking, plastics, and ceramics to produce components with high precision and consistency. Pressing dies work by applying force to a material, either through mechanical, hydraulic, or pneumatic means, to deform it into the desired shape. These dies are designed to withstand high pressures and repetitive use, ensuring durability and accuracy in mass production. Understanding the types, materials, and applications of pressing dies is essential for optimizing manufacturing processes and achieving high-quality results.
Key Points Explained:
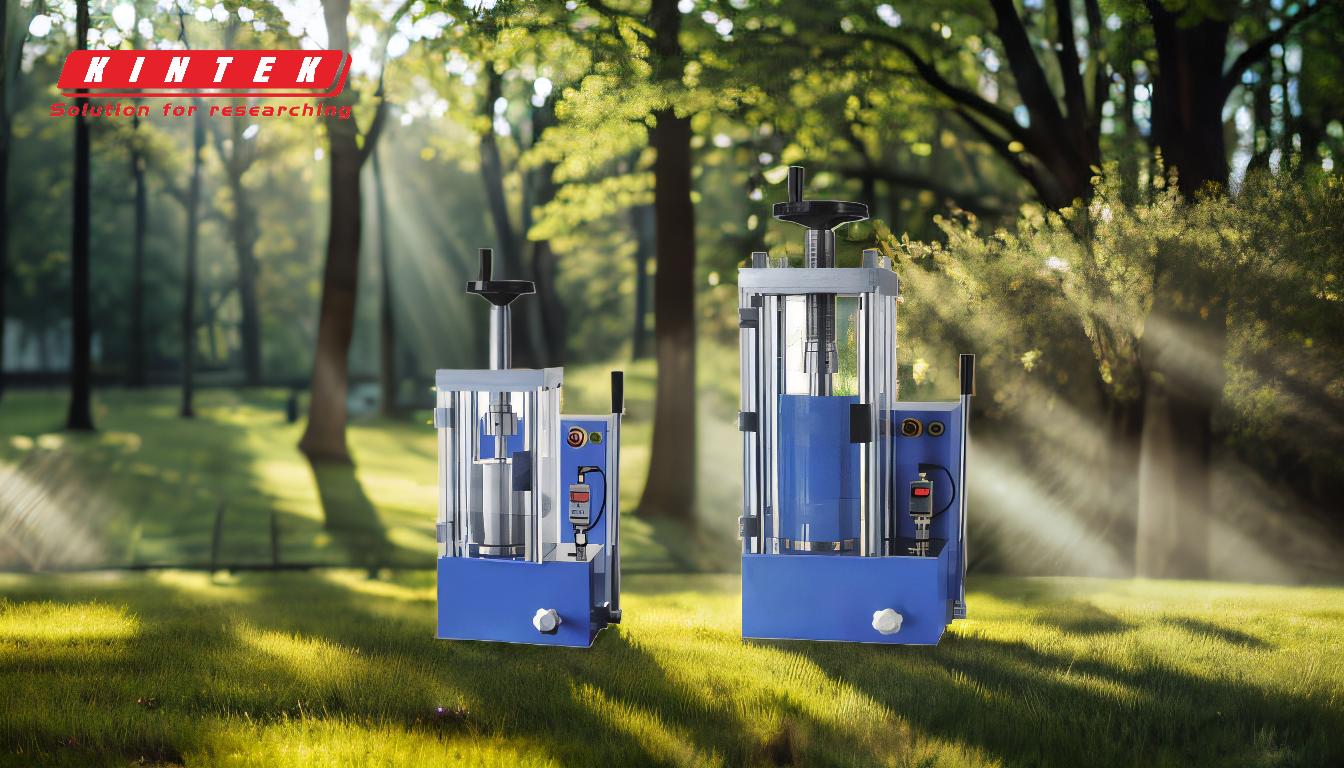
-
Definition and Purpose of Pressing Dies:
- Pressing dies are tools used to shape or cut materials into specific forms by applying force.
- They are essential in industries like metalworking, plastics, and ceramics for producing components with high precision and consistency.
- The primary purpose of pressing dies is to ensure that materials are deformed or cut accurately and efficiently, often in mass production settings.
-
Types of Pressing Dies:
- Blanking Dies: Used to cut flat shapes from sheet metal or other materials.
- Forming Dies: Designed to bend or shape materials into specific geometries without cutting them.
- Piercing Dies: Used to create holes or cutouts in materials.
- Compound Dies: Combine multiple operations, such as blanking and piercing, in a single press cycle.
- Progressive Dies: Perform multiple operations in a sequence as the material moves through the die.
-
Materials Used in Pressing Dies:
- Tool Steel: Commonly used for its hardness, wear resistance, and ability to withstand high pressures.
- Carbide: Offers superior wear resistance and is often used for high-volume production.
- High-Speed Steel (HSS): Known for its toughness and ability to maintain sharp edges under high temperatures.
- Ceramics: Used in specialized applications where extreme hardness and heat resistance are required.
-
Applications of Pressing Dies:
- Automotive Industry: Used to manufacture car body parts, engine components, and other precision parts.
- Electronics: Essential for producing connectors, housings, and other small, intricate components.
- Aerospace: Used to create lightweight, high-strength components for aircraft and spacecraft.
- Consumer Goods: Applied in the production of items like kitchen utensils, appliances, and packaging materials.
-
Design Considerations for Pressing Dies:
- Material Selection: The choice of die material depends on the type of material being processed and the required durability.
- Tolerance and Precision: Dies must be designed to achieve the required dimensional accuracy and surface finish.
- Die Life: Factors such as wear resistance, maintenance, and the number of cycles the die can withstand are critical for cost-effective production.
- Ease of Maintenance: Dies should be designed for easy disassembly, cleaning, and repair to minimize downtime.
-
Advantages of Using Pressing Dies:
- High Precision: Pressing dies allow for the production of components with tight tolerances and consistent quality.
- Efficiency: They enable high-speed production, making them ideal for mass manufacturing.
- Versatility: Pressing dies can be designed to handle a wide range of materials and shapes.
- Cost-Effectiveness: Despite the initial investment, pressing dies reduce per-unit costs in high-volume production.
-
Challenges and Limitations:
- Initial Cost: The design and manufacture of pressing dies can be expensive, especially for complex shapes.
- Maintenance: Regular maintenance is required to ensure the longevity and performance of the dies.
- Material Limitations: Some materials may be difficult to process using pressing dies due to their hardness or brittleness.
- Design Complexity: Creating dies for highly intricate or custom shapes can be challenging and time-consuming.
-
Future Trends in Pressing Die Technology:
- Advanced Materials: The development of new materials with enhanced properties is expected to improve die performance and longevity.
- Automation: Increasing automation in die design and manufacturing processes is likely to enhance precision and reduce lead times.
- Sustainability: There is a growing focus on creating more sustainable die manufacturing processes, including the use of recyclable materials and energy-efficient technologies.
- Digitalization: The integration of digital tools, such as computer-aided design (CAD) and simulation software, is improving the accuracy and efficiency of die design and testing.
By understanding these key points, manufacturers and purchasers can make informed decisions about the selection, use, and maintenance of pressing dies, ultimately improving production efficiency and product quality.
Summary Table:
Aspect | Details |
---|---|
Definition | Tools used to shape or cut materials into specific forms by applying force. |
Types | Blanking, Forming, Piercing, Compound, Progressive Dies. |
Materials | Tool Steel, Carbide, High-Speed Steel (HSS), Ceramics. |
Applications | Automotive, Electronics, Aerospace, Consumer Goods. |
Advantages | High precision, efficiency, versatility, cost-effectiveness. |
Challenges | High initial cost, maintenance, material limitations, design complexity. |
Future Trends | Advanced materials, automation, sustainability, digitalization. |
Discover how pressing dies can optimize your manufacturing process—contact our experts today!