Physical Vapor Deposition (PVD) is a process used to create thin, durable coatings on surfaces by vaporizing a solid material in a vacuum and depositing it onto a substrate. This technique is widely used in industries to enhance the properties of materials, such as improving hardness, reducing friction, and increasing resistance to oxidation. PVD is a clean and efficient method that operates at an atomic level, making it a preferred alternative to traditional coating methods like electroplating. The process involves three main steps: gasification of the material, migration of the vaporized particles, and deposition onto the target surface.
Key Points Explained:
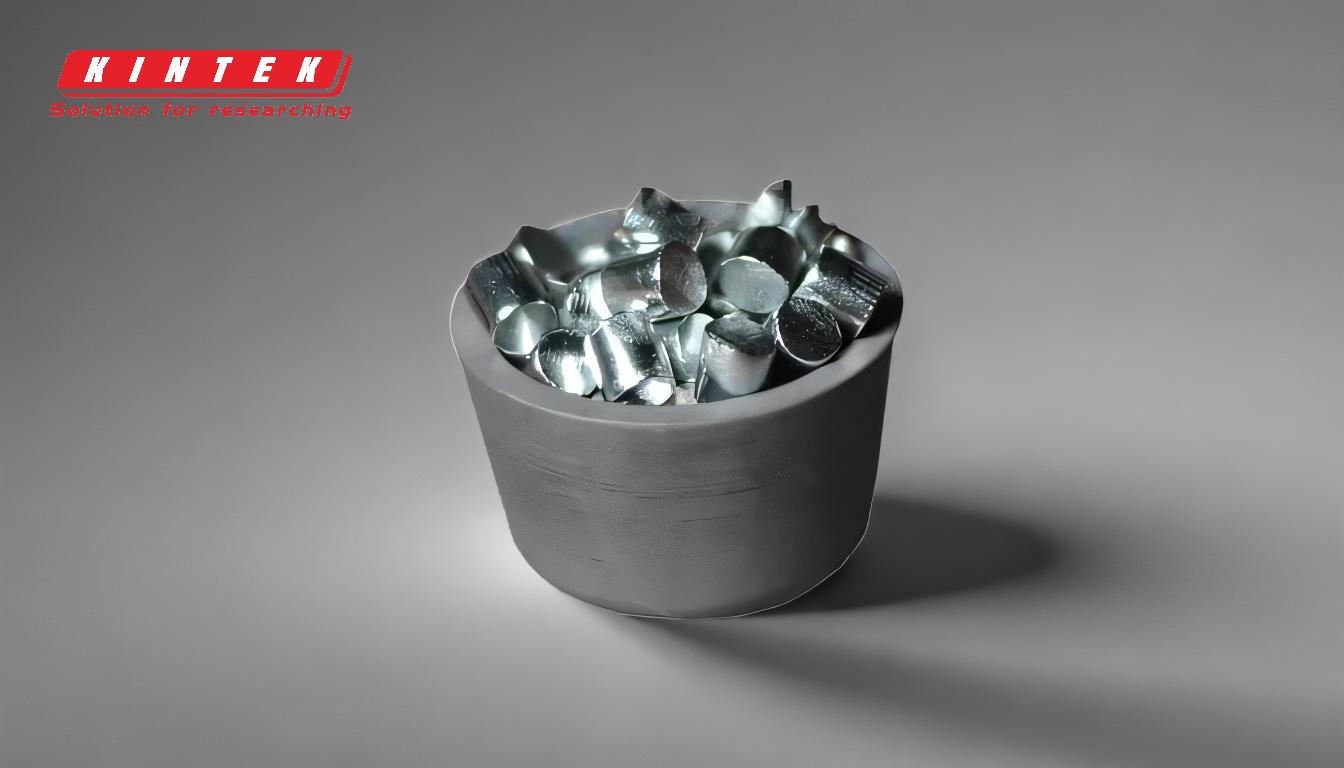
-
What is PVD?
- PVD stands for Physical Vapor Deposition, a process that creates thin, durable coatings on surfaces.
- It involves vaporizing a solid material in a vacuum environment and depositing it onto a substrate.
- This technique is used to enhance material properties such as hardness, friction reduction, and oxidation resistance.
-
How Does PVD Work?
- Gasification of the Material: The solid material is vaporized using methods like evaporation, sputtering, or laser ablation.
- Migration of Particles: The vaporized atoms, molecules, or ions move through the vacuum and may react with other gases.
- Deposition onto Substrate: The vaporized material condenses onto the substrate, forming a thin, uniform coating.
-
Key Features of PVD:
- Vacuum Environment: PVD is conducted under vacuum conditions to ensure a clean and controlled process.
- No Chemical Reactions: Unlike some other coating methods, PVD does not involve chemical reactions, making it a pure physical process.
- Atomic-Level Precision: The process operates at an atomic level, allowing for precise and uniform coatings.
-
Applications of PVD:
- Industrial Coatings: Used to enhance the durability and performance of tools, machinery, and components.
- Decorative Finishes: Applied to products like watches, jewelry, and consumer electronics for aesthetic and protective purposes.
- Aerospace and Automotive: Utilized to improve the performance and longevity of critical components in these industries.
-
Advantages of PVD:
- Durability: PVD coatings are highly durable and resistant to wear, corrosion, and oxidation.
- Versatility: Can be applied to a wide range of materials, including metals, ceramics, and plastics.
- Environmental Friendliness: PVD is a clean process that produces minimal waste and does not involve harmful chemicals.
-
Comparison with Electroplating:
- Process: PVD is a dry process conducted in a vacuum, whereas electroplating involves immersing the substrate in a liquid solution.
- Coating Quality: PVD coatings are typically more uniform and durable compared to electroplated coatings.
- Environmental Impact: PVD is considered more environmentally friendly due to the absence of toxic chemicals and waste.
-
Future of PVD:
- Innovation: Ongoing research is focused on improving PVD techniques to achieve even thinner, more durable coatings.
- Expanding Applications: As industries continue to demand high-performance materials, the use of PVD is expected to grow in sectors like renewable energy, medical devices, and advanced electronics.
In summary, PVD is a versatile and efficient coating technique that offers numerous benefits over traditional methods. Its ability to create durable, high-quality coatings at an atomic level makes it an essential process in modern manufacturing and technology.
Summary Table:
Aspect | Details |
---|---|
What is PVD? | A process to create thin, durable coatings by vaporizing materials in a vacuum. |
How PVD Works | 1. Gasification of material 2. Migration of particles 3. Deposition on substrate |
Key Features | Vacuum environment, no chemical reactions, atomic-level precision. |
Applications | Industrial coatings, decorative finishes, aerospace, and automotive. |
Advantages | Durability, versatility, environmental friendliness. |
Comparison with Electroplating | PVD is cleaner, more uniform, and environmentally friendly. |
Future of PVD | Innovations for thinner coatings, expanding applications in renewable energy and medical devices. |
Learn how PVD coatings can transform your materials—contact our experts today!