Quench annealing is a specialized heat treatment process that combines the principles of annealing and quenching to achieve specific material properties. It involves heating the material to a high temperature, holding it at that temperature to allow for microstructural changes, and then rapidly cooling (quenching) it to lock in those changes. This process is particularly useful for materials that require both reduced hardness and improved ductility, as well as specific microstructural characteristics that can only be achieved through rapid cooling. Quench annealing is often used in industries where materials need to withstand high stress or where further processing, such as machining or additional heat treatment, is required.
Key Points Explained:
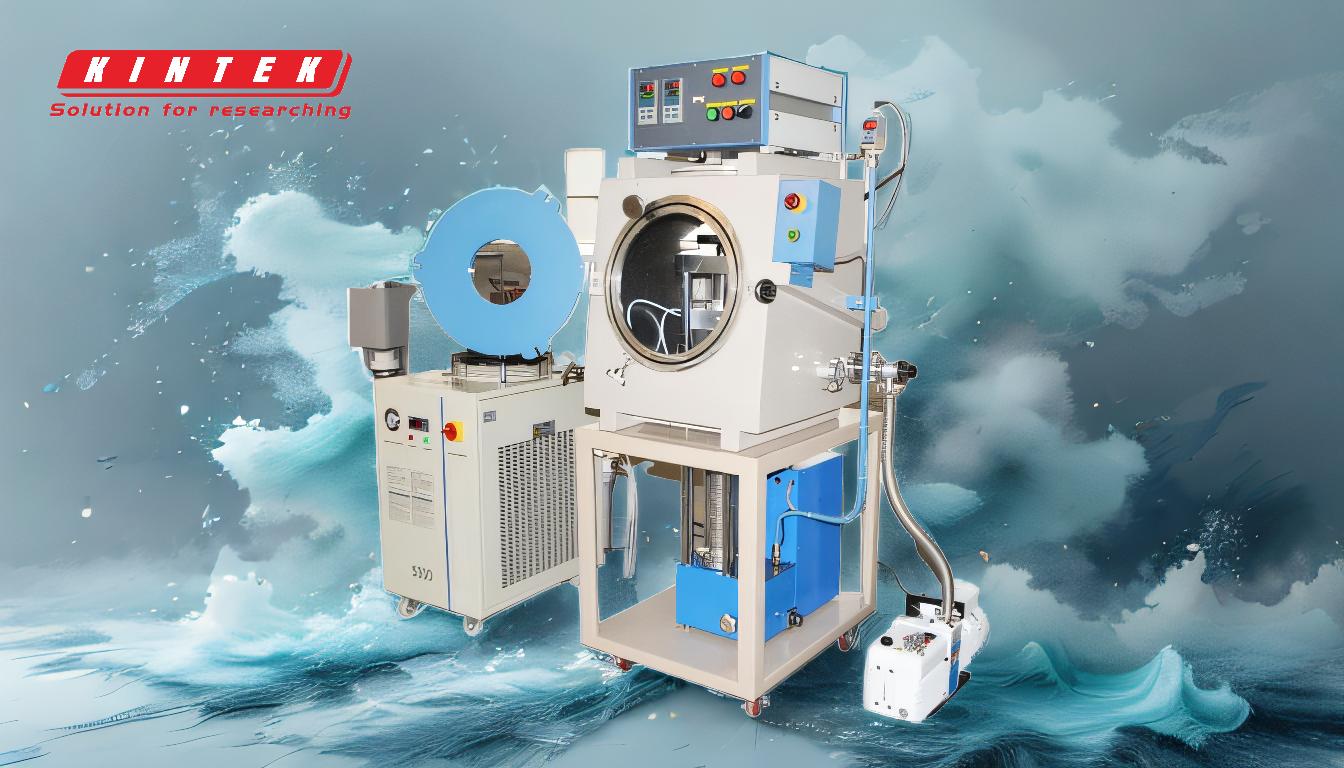
-
Purpose of Quench Annealing:
- Quench annealing is primarily used to reduce the hardness of a material while simultaneously improving its ductility and toughness.
- The process is designed to release internal stresses within the material, making it easier to process and mold during plastic deformation.
- It is particularly beneficial for materials that will undergo further machining or additional heat treatment, as it restores the material to a 'soft' condition.
-
Process Steps:
- Heating: The material is heated to a specific temperature, typically above its recrystallization temperature, to allow for microstructural changes. This step is crucial for reducing the number of dislocations in the crystal structure, which in turn reduces hardness and increases ductility.
- Holding: The material is held at the high temperature for a set period to ensure uniform heating and to allow for complete microstructural transformation. This step is essential for achieving the desired material properties.
- Quenching: After holding at the high temperature, the material is rapidly cooled (quenched) to lock in the new microstructure. Rapid cooling prevents the formation of undesirable phases and ensures that the material retains the desired properties.
-
Microstructural Changes:
- During the heating and holding stages, the material undergoes recrystallization, where new grains form, replacing the deformed grains. This reduces the number of dislocations in the crystal structure, leading to a softer and more ductile material.
- The rapid cooling (quenching) step helps to stabilize the new microstructure, preventing the formation of large grains or other undesirable phases that could affect the material's mechanical properties.
-
Applications of Quench Annealing:
- Industrial Applications: Quench annealing is widely used in industries where materials are subjected to high stress or require further processing. For example, it is commonly used in the production of steel pipes, where the material needs to be both strong and ductile to withstand high pressures.
- Machining: Materials that have undergone quench annealing are easier to machine, as the process reduces hardness and increases ductility, making the material more workable.
- Additional Heat Treatment: Quench annealing can be a precursor to other heat treatment processes, such as tempering, where the material is further heated to achieve specific mechanical properties.
-
Advantages of Quench Annealing:
- Improved Ductility: By reducing the number of dislocations in the crystal structure, quench annealing significantly increases the material's ductility, making it less prone to fracturing under stress.
- Reduced Hardness: The process softens the material, making it easier to machine or shape.
- Stress Relief: Quench annealing relieves internal stresses caused by previous processing or fabrication, reducing the risk of material failure during use.
-
Considerations and Limitations:
- Cooling Rate: The rate of cooling during quenching is critical. Too slow, and the material may not retain the desired microstructure; too fast, and the material could become too brittle.
- Material Selection: Not all materials are suitable for quench annealing. The process is most effective on materials that can undergo significant microstructural changes at high temperatures.
- Energy Consumption: Quench annealing can be energy-intensive due to the high temperatures and rapid cooling required, which may increase production costs.
In summary, quench annealing is a versatile heat treatment process that combines the benefits of annealing and quenching to achieve specific material properties. It is particularly useful in industries where materials need to be both strong and ductile, and where further processing is required. By carefully controlling the heating, holding, and quenching stages, manufacturers can produce materials with improved mechanical properties and reduced internal stresses.
Summary Table:
Aspect | Details |
---|---|
Purpose | Reduces hardness, improves ductility, and relieves internal stresses. |
Process Steps | Heating → Holding → Quenching. |
Microstructural Changes | Recrystallization and grain stabilization during rapid cooling. |
Applications | Steel pipes, machining, and precursor to other heat treatments. |
Advantages | Improved ductility, reduced hardness, and stress relief. |
Limitations | Cooling rate sensitivity, material suitability, and energy consumption. |
Learn how quench annealing can optimize your material properties—contact our experts today!