Sintering in ceramics is a critical thermal process that transforms ceramic powders into dense, solid materials without melting them completely. It involves heating the powder to a temperature below its melting point, allowing the particles to bond through atomic diffusion, resulting in a hard, durable, and precise final product. This process is essential for achieving specific physical properties, such as hardness, toughness, and abrasion resistance, while enabling the creation of complex shapes and geometries. Sintering is widely used in advanced ceramics and powder metallurgy, offering cost-effective and efficient manufacturing solutions for high-performance materials.
Key Points Explained:
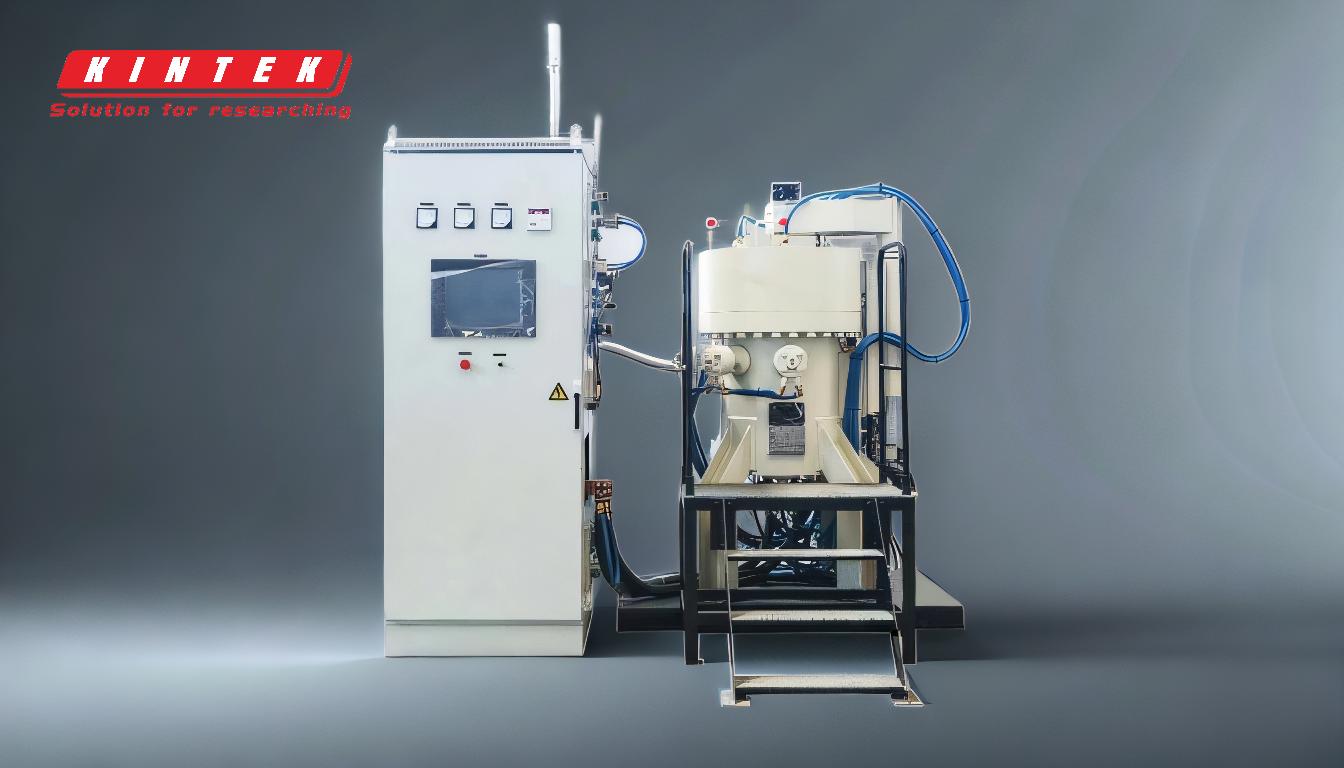
-
Definition of Sintering in Ceramics:
- Sintering is a thermal process that transforms ceramic powders into dense, solid bodies by applying heat and sometimes pressure, without reaching the material's melting point.
- It involves atomic diffusion, where particles bond together to form a cohesive structure.
-
Purpose and Importance:
- Sintering is crucial for producing ceramic components with specific properties such as hardness, toughness, and precision.
- It enables the creation of intricate shapes and geometries that are difficult to achieve through traditional manufacturing methods.
- The process combines the properties of multiple materials, such as toughness and abrasion resistance, into a single product.
-
Process Steps:
- Heating: The ceramic powder is heated to a temperature below its melting point.
- Holding: The material is held at this temperature for a specific duration to allow atomic diffusion and bonding.
- Cooling: The material is cooled to achieve the desired properties and structural integrity.
-
Key Mechanisms:
- Diffusion and Mass Transfer: Atoms move across particle boundaries, fusing them together and reducing porosity.
- Densification: The material becomes denser and more uniform in microstructure, leading to improved mechanical properties.
-
Applications in Ceramics:
- Sintering is widely used in advanced ceramics to produce polycrystalline materials with stable shapes and excellent properties.
- It is essential for manufacturing components in industries such as electronics, aerospace, and medical devices.
-
Advantages of Sintering:
- Cost-Effectiveness: Lower tooling costs for producing complex parts.
- Precision and Repeatability: High accuracy and consistency in mass production.
- Material Versatility: Suitable for materials with high melting points, such as tungsten and molybdenum.
-
Comparison with Other Processes:
- Unlike melting, sintering does not liquefy the material, preserving its structural integrity and enabling the creation of intricate designs.
- It is more efficient for producing high-performance ceramics compared to traditional forming methods.
-
Challenges and Considerations:
- Temperature control is critical to avoid defects such as warping or cracking.
- The sintering process must be optimized to achieve the desired density and properties.
By understanding these key points, ceramic manufacturers and purchasers can appreciate the role of sintering in producing high-quality, durable, and precise ceramic components for various applications.
Summary Table:
Aspect | Details |
---|---|
Definition | A thermal process that bonds ceramic powders without melting them. |
Purpose | Produces hard, tough, and abrasion-resistant ceramic components. |
Process Steps | Heating, holding, and cooling to achieve desired properties. |
Key Mechanisms | Diffusion, mass transfer, and densification. |
Applications | Electronics, aerospace, medical devices, and advanced ceramics. |
Advantages | Cost-effective, precise, repeatable, and versatile for high-melting materials. |
Challenges | Requires precise temperature control to avoid defects. |
Discover how sintering can enhance your ceramic manufacturing—contact our experts today!