Sintering with ceramic materials is a critical process in the manufacturing of ceramic objects, where ceramic powder particles are consolidated by heating them to high temperatures below their melting point. This process involves material diffusion, grain boundary movement, and densification, resulting in a stronger, more durable, and less porous final product. Sintering can also involve additional forces like pressure or electrical currents to enhance the bonding of particles. The process is essential for creating ceramic components with specific mechanical and structural properties, making it a cornerstone of ceramic manufacturing.
Key Points Explained:
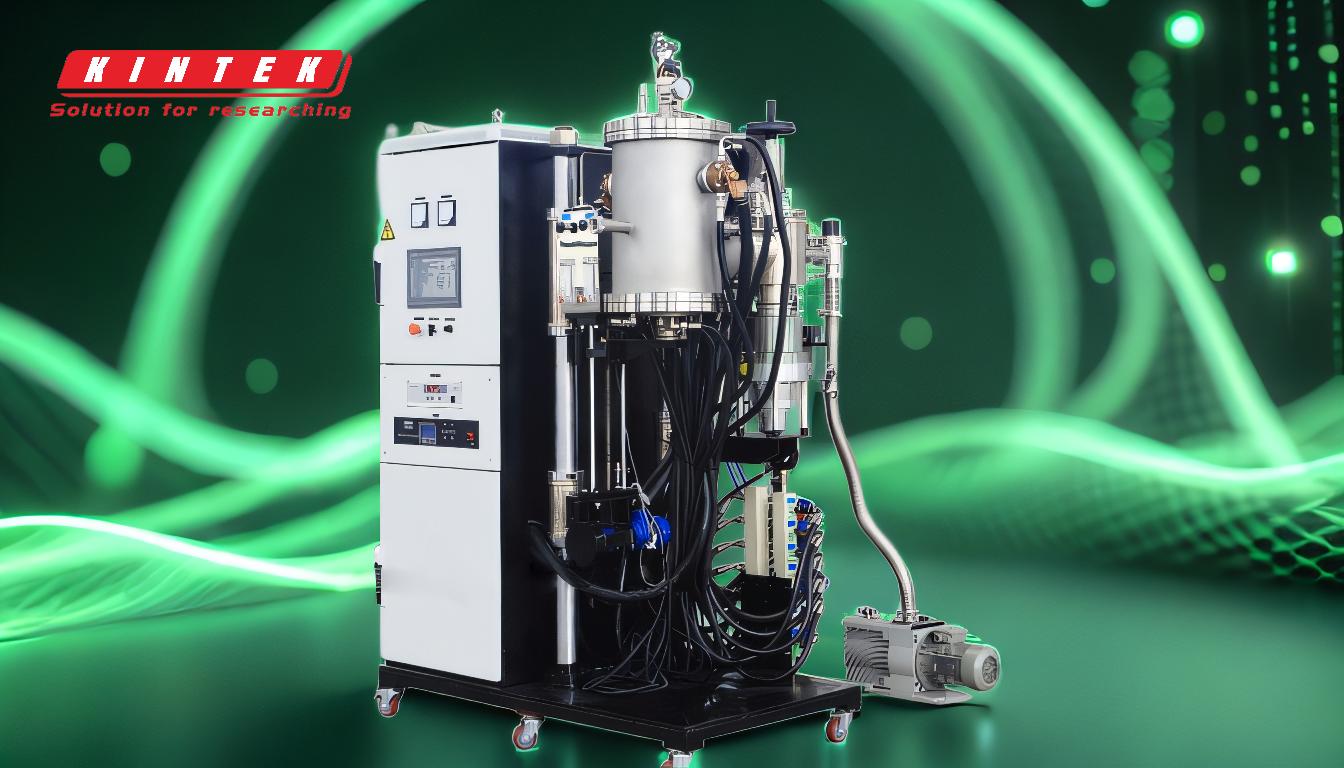
-
Definition of Sintering with Ceramic Materials
- Sintering is a process where ceramic powder particles are heated to high temperatures below their melting point to consolidate them into a solid mass.
- It is also referred to as "firing" in ceramic manufacturing.
- The process involves material diffusion between neighboring particles, leading to densification and the formation of a cohesive structure.
-
Purpose and Outcomes of Sintering
- Reduction of Porosity: Sintering reduces the porosity of the ceramic material, making it denser and less permeable.
- Increased Strength and Durability: The process strengthens the material by forcing atoms to bond more tightly, resulting in a harder and more durable final product.
- Shrinkage: As the material densifies, it undergoes shrinkage, which is a natural outcome of the consolidation process.
-
Key Mechanisms in Sintering
- Material Diffusion: Atoms from the surface of powder particles migrate to neighboring particles, forming bonds and reducing voids.
- Grain Boundary Movement: At high temperatures, grain boundaries within the material shift, contributing to densification and structural integrity.
- Flow of Glass Phases: In some ceramics, glass phases flow during sintering, aiding in the consolidation of the powdery structure.
-
Factors Influencing the Sintering Process
- Temperature: Sintering occurs at high temperatures, typically below the melting point of the ceramic material. The exact temperature depends on the material's composition.
- Pressure: In some cases, external pressure is applied to enhance the densification process.
- Atmosphere: The sintering environment (e.g., air, vacuum, or controlled gas) can affect the outcome by influencing oxidation, reduction, or other chemical reactions.
- Time: The duration of sintering impacts the degree of densification and the final properties of the ceramic.
-
Applications of Ceramic Sintering
- Pottery and Traditional Ceramics: Sintering is widely used in the production of pottery, tiles, and other traditional ceramic objects.
- Advanced Ceramics: The process is essential for manufacturing advanced ceramics used in electronics, aerospace, and medical devices, where high strength and precision are required.
- Industrial Components: Sintered ceramics are used to create components like bearings, seals, and cutting tools due to their hardness and wear resistance.
-
Advantages of Sintering in Ceramic Manufacturing
- Enhanced Material Properties: Sintering improves mechanical strength, thermal stability, and chemical resistance.
- Cost-Effectiveness: The process allows for the production of complex shapes with minimal material waste.
- Versatility: Sintering can be applied to a wide range of ceramic materials, including oxides, carbides, and nitrides.
-
Challenges and Considerations
- Control of Shrinkage: Shrinkage during sintering must be carefully managed to ensure dimensional accuracy in the final product.
- Energy Consumption: The high temperatures required for sintering can make the process energy-intensive.
- Material-Specific Parameters: Each ceramic material has unique sintering requirements, necessitating precise control of temperature, pressure, and atmosphere.
By understanding these key points, ceramic manufacturers and purchasers can make informed decisions about the sintering process, ensuring the production of high-quality ceramic components tailored to specific applications.
Summary Table:
Aspect | Details |
---|---|
Definition | Heating ceramic powders below melting point to form a solid, cohesive mass. |
Purpose | Reduces porosity, increases strength, and creates durable ceramic products. |
Key Mechanisms | Material diffusion, grain boundary movement, and glass phase flow. |
Influencing Factors | Temperature, pressure, atmosphere, and time. |
Applications | Pottery, advanced ceramics, and industrial components. |
Advantages | Enhanced strength, cost-effectiveness, and material versatility. |
Challenges | Shrinkage control, energy consumption, and material-specific parameters. |
Need expert advice on sintering ceramic materials? Contact us today to optimize your ceramic manufacturing process!