The Spark Plasma Sintering (SPS) method is an advanced powder metallurgy technique used to fabricate high-performance materials with unique microstructures and properties. It combines the principles of hot pressing and pulsed electric current to achieve rapid heating, short processing times, and precise control over temperature, pressure, and heating rates. SPS operates in a vacuum or controlled atmosphere to prevent oxidation and ensure material purity. The process leverages the "spark plasma effect," which inhibits particle growth and enables the creation of materials with tailored compositions and enhanced properties. Its advantages include low sintering temperatures, fast heating rates, and multi-field coupling (electric-mechanical-thermal), making it ideal for producing advanced ceramics, composites, and nanostructured materials.
Key Points Explained:
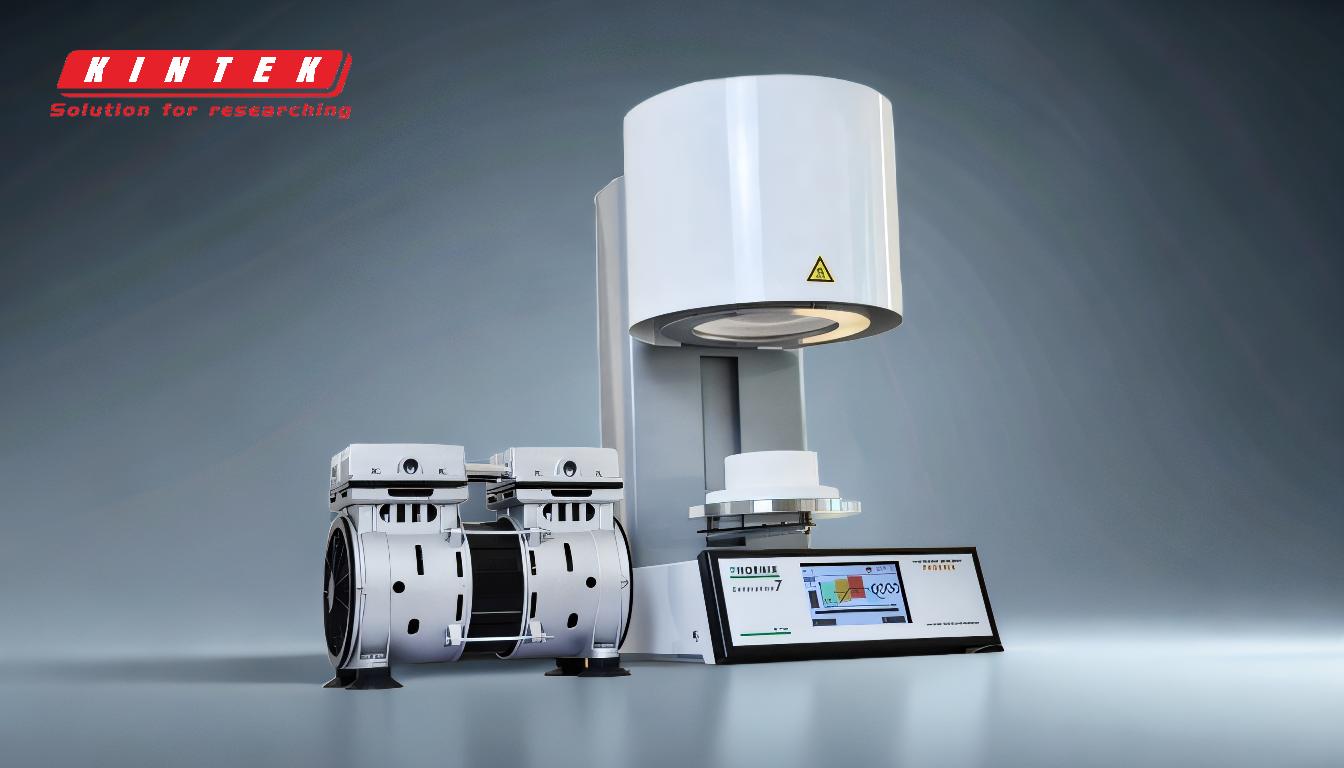
-
Definition and Purpose of SPS:
- SPS, or Spark Plasma Sintering, is a powder consolidation technique that uses pulsed electric currents to rapidly sinter powdered materials into dense, high-performance components.
- It is designed to create materials with unique microstructures and properties that are difficult to achieve through conventional sintering methods.
-
Operating Principles:
- SPS is based on a modified hot pressing setup, where an electric current flows directly through the pressing die (typically made of graphite) and the powdered material.
- The process utilizes pulsed currents to generate rapid heating and short process cycles, often referred to as the "spark plasma effect."
- This effect promotes localized heating at particle interfaces, which enhances densification while inhibiting particle growth, resulting in fine-grained microstructures.
-
Key Features of the SPS Process:
- Fast Heating Rates: SPS achieves extremely high heating rates, often reaching temperatures of 1000°C or higher in minutes, significantly reducing processing times.
- Low Sintering Temperatures: The process allows sintering at lower temperatures compared to traditional methods, minimizing energy consumption and preserving material properties.
- Adjustable Sintering Pressure: The applied pressure can be precisely controlled to optimize densification and material properties.
- Multi-Field Coupling: SPS integrates electric, mechanical, and thermal fields, enabling precise control over the sintering environment and material behavior.
-
Advantages of SPS:
- Material Purity: SPS operates in a vacuum or controlled atmosphere, preventing oxidation and contamination, which is critical for high-purity materials.
- Unique Microstructures: The rapid heating and short holding times inhibit grain growth, allowing the creation of nanostructured and fine-grained materials.
- Versatility: SPS can be used to fabricate a wide range of materials, including ceramics, composites, metals, and functionally graded materials.
- Energy Efficiency: The combination of low sintering temperatures and short processing times makes SPS an energy-efficient technique.
-
Applications of SPS:
- Advanced Ceramics: SPS is widely used to produce dense, high-strength ceramics for applications in aerospace, electronics, and biomedical fields.
- Nanostructured Materials: The process is ideal for creating materials with nanoscale features, such as nanocrystalline metals and nanocomposites.
- Functionally Graded Materials: SPS enables the fabrication of materials with graded compositions and properties, suitable for specialized engineering applications.
- High-Performance Composites: SPS is used to produce composite materials with enhanced mechanical, thermal, and electrical properties.
-
Comparison with Conventional Sintering Methods:
- Speed: SPS significantly reduces processing times compared to traditional sintering methods, which often require hours or days.
- Temperature: SPS achieves densification at lower temperatures, preserving the integrity of temperature-sensitive materials.
- Control: The ability to precisely control temperature, pressure, and heating rates in SPS allows for tailored material properties and microstructures.
-
Challenges and Considerations:
- Equipment Cost: SPS systems are more expensive than conventional sintering equipment due to their advanced technology and precise control capabilities.
- Material Compatibility: Not all materials are suitable for SPS, as some may react with the graphite dies or require specific sintering conditions.
- Scaling Up: While SPS is highly effective for laboratory-scale production, scaling up to industrial levels can present challenges in terms of uniformity and cost-effectiveness.
In summary, the SPS method is a cutting-edge sintering technique that offers unparalleled control over material properties and microstructures. Its ability to combine fast heating rates, low sintering temperatures, and precise pressure control makes it a valuable tool for producing advanced materials with tailored properties. Despite its higher equipment costs and some scalability challenges, SPS is widely recognized for its versatility and efficiency in fabricating high-performance ceramics, composites, and nanostructured materials.
Summary Table:
Key Aspect | Details |
---|---|
Definition | A powder consolidation technique using pulsed electric currents for sintering. |
Operating Principles | Combines hot pressing and pulsed current for rapid heating and densification. |
Key Features | Fast heating rates, low sintering temperatures, adjustable pressure, multi-field coupling. |
Advantages | Material purity, unique microstructures, versatility, energy efficiency. |
Applications | Advanced ceramics, nanostructured materials, functionally graded materials, composites. |
Comparison with Conventional Methods | Faster, lower temperatures, precise control. |
Challenges | High equipment costs, material compatibility, scalability issues. |
Ready to explore how Spark Plasma Sintering can revolutionize your material fabrication? Contact us today to learn more!