Sputtering of nanomaterials is a physical vapor deposition (PVD) technique used to deposit thin films of materials at the nanoscale. It involves bombarding a target material with high-energy ions, typically from an inert gas like argon, in a vacuum environment. The bombardment causes atoms or molecules to be ejected from the target's surface, which then travel through the vacuum chamber and deposit onto a substrate, forming a thin, uniform film. This process is widely used in industries such as electronics, optics, and packaging due to its precision and ability to produce high-quality coatings.
Key Points Explained:
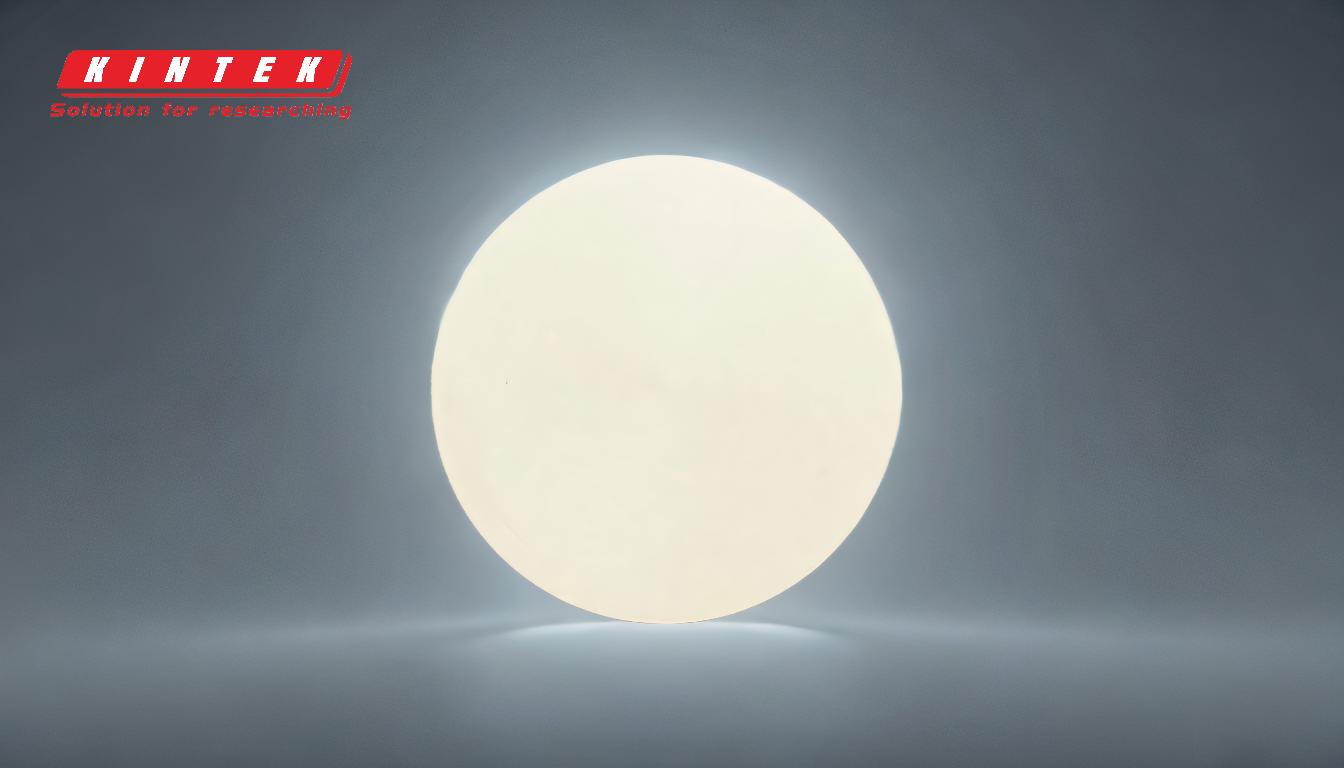
-
Basic Principle of Sputtering:
- Sputtering is a process where ions of an inert gas (e.g., argon or xenon) are accelerated toward a target material in a vacuum chamber.
- The ions transfer their kinetic energy to the target material, causing atoms or molecules to be ejected from its surface.
- These ejected particles are neutral and travel through the chamber to deposit onto a substrate, forming a thin film.
-
Components of the Sputtering System:
- Vacuum Chamber: The process occurs in a vacuum to minimize contamination and allow the ejected particles to travel unimpeded.
- Target Material: The material to be sputtered, which serves as the source of the thin film.
- Substrate: The surface onto which the sputtered material is deposited.
- Inert Gas: Typically argon, which is ionized to create the plasma needed for sputtering.
- Electric Field: A voltage is applied between the target (cathode) and the substrate (anode) to accelerate the ions toward the target.
-
Mechanism of Sputtering:
- Gas atoms in the chamber are ionized to form a plasma.
- The positively charged ions are accelerated toward the target material by the electric field.
- When the ions strike the target, they transfer their energy, causing atoms or molecules to be ejected from the target's surface.
- The ejected particles travel through the chamber and deposit onto the substrate, forming a thin film.
-
Applications of Sputtering in Nanomaterials:
- Electronics: Sputtering is used to deposit thin films for semiconductors, integrated circuits, and other electronic components.
- Optics: It is employed to create reflective coatings for mirrors and anti-reflective coatings for lenses.
- Packaging: Sputtered films are used in packaging materials, such as the metallic layers in potato chip bags.
- Advanced Materials: The technique is used to produce nanomaterials with precise properties for research and industrial applications.
-
Advantages of Sputtering:
- Precision: Sputtering allows for the deposition of very thin, uniform films with high accuracy.
- Versatility: It can be used with a wide range of materials, including metals, semiconductors, and insulators.
- Quality: The process produces high-quality coatings with excellent adhesion and minimal defects.
- Scalability: Sputtering is suitable for both small-scale research and large-scale industrial production.
-
Challenges and Considerations:
- Vacuum Requirements: The process requires a high vacuum, which can be costly and complex to maintain.
- Energy Consumption: Sputtering can be energy-intensive due to the need for plasma generation and ion acceleration.
- Target Erosion: The target material erodes over time, requiring periodic replacement or refurbishment.
- Uniformity: Achieving uniform deposition across large substrates can be challenging and may require advanced techniques like magnetron sputtering.
-
Historical Context:
- Sputtering has been used since the early 1800s and has evolved into a mature and reliable technique for thin film deposition.
- Its applications have expanded significantly with advancements in materials science and nanotechnology, making it a cornerstone of modern manufacturing processes.
In summary, sputtering of nanomaterials is a versatile and precise technique for depositing thin films at the nanoscale. It plays a critical role in various industries, from electronics to optics, and continues to be a key technology in the development of advanced materials and devices.
Summary Table:
Aspect | Details |
---|---|
Basic Principle | Ions bombard a target material, ejecting atoms that form a thin film. |
Key Components | Vacuum chamber, target material, substrate, inert gas, electric field. |
Applications | Electronics, optics, packaging, advanced materials. |
Advantages | Precision, versatility, high-quality coatings, scalability. |
Challenges | High vacuum requirements, energy consumption, target erosion, uniformity. |
Discover how sputtering can enhance your production process—contact our experts today!