The annealing process in a furnace is a heat treatment method used to alter the physical and mechanical properties of materials, primarily metals, to improve their ductility, reduce internal stresses, and enhance machinability. This process involves heating the material above its recrystallization temperature, maintaining it at this temperature for a specific duration, and then cooling it at a controlled rate. The result is a material with a refined microstructure, reduced hardness, and increased flexibility, making it easier to shape and work with. Annealing furnaces, such as the vacuum annealing furnace, are specifically designed to facilitate this process by providing precise temperature control and uniform heating.
Key Points Explained:
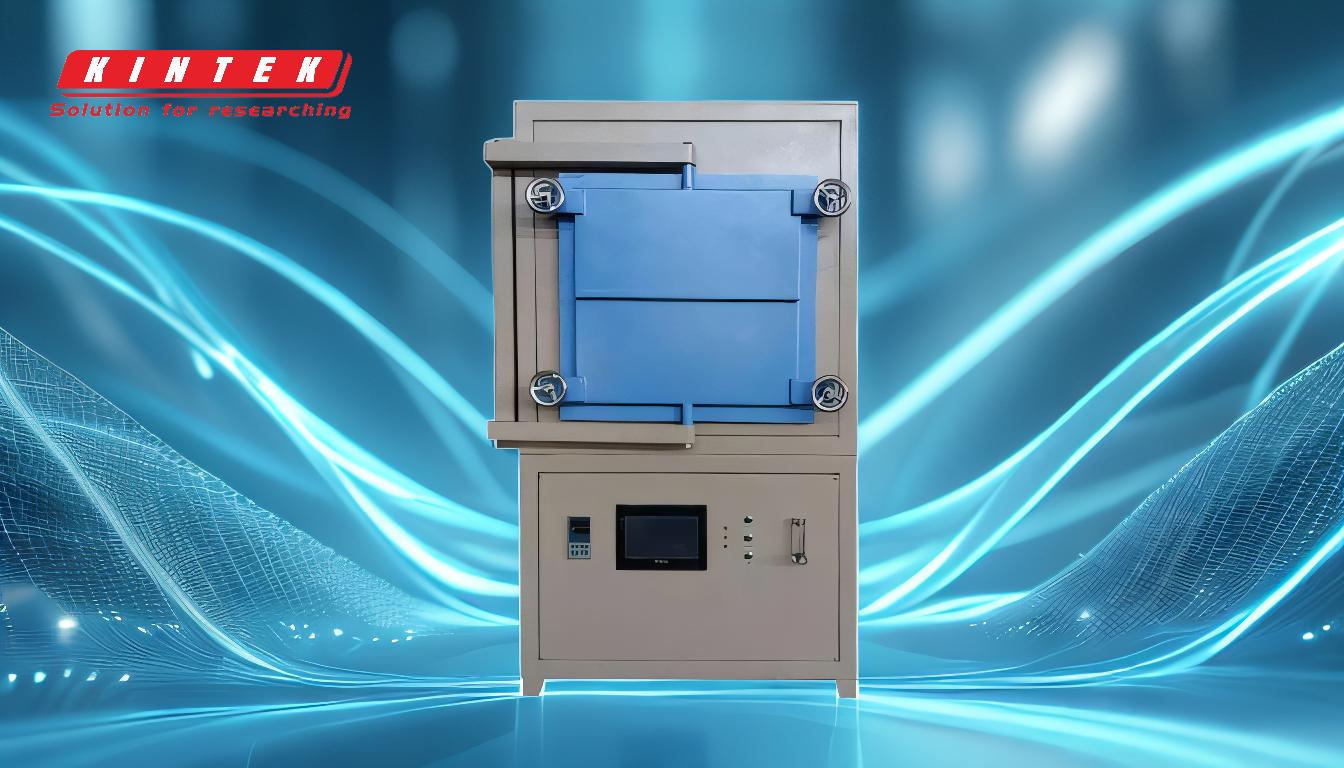
-
Purpose of Annealing:
- Improves Ductility: Annealing makes materials more pliable, allowing them to be shaped without cracking.
- Reduces Internal Stresses: The process relieves internal stresses that can lead to material failure.
- Enhances Machinability: By reducing hardness, annealing makes materials easier to machine.
- Improves Mechanical and Electrical Properties: The process can enhance the overall performance of the material.
-
Stages of the Annealing Process:
- Recovery: The material is heated to a temperature that relieves internal stresses without altering its microstructure significantly.
- Recrystallization: The material is heated above its recrystallization temperature but below its melting point, allowing new grains to form without melting.
- Grain Growth: As the material cools, new grains grow, resulting in a more refined and uniform microstructure.
-
Role of the Annealing Furnace:
- Temperature Control: Annealing furnaces provide precise temperature control to ensure the material reaches and maintains the required temperature for the desired duration.
- Uniform Heating: The furnace ensures that the material is heated evenly, preventing localized overheating or cooling.
- Controlled Cooling: The furnace allows for controlled cooling rates, which are crucial for achieving the desired material properties. A cooling circulator can be used to manage this process effectively.
-
Recrystallization Temperature:
- Definition: The recrystallization temperature is the temperature at which new grains begin to form in the material, replacing the deformed grains.
- Importance: Heating the material above this temperature is essential for the annealing process to be effective.
-
Cooling Process:
- Slow Cooling: The material is cooled slowly to room temperature to allow the new grains to grow and stabilize, resulting in a more ductile and less brittle material.
- Controlled Rate: The cooling rate is carefully controlled to prevent the reintroduction of internal stresses.
-
Applications of Annealing:
- Metalworking: Annealing is widely used in metalworking to prepare metals for further processing, such as rolling, forging, or machining.
- Electronics: The process is used in the production of electronic components to improve their electrical properties.
- Manufacturing: Annealing is essential in the manufacturing of various products, from automotive parts to construction materials.
-
Benefits of Annealing:
- Enhanced Workability: The material becomes easier to work with, reducing the risk of cracking or breaking during fabrication.
- Improved Performance: The material's mechanical and electrical properties are enhanced, leading to better performance in its intended application.
- Stress Relief: Internal stresses are relieved, reducing the likelihood of material failure under stress.
In summary, the annealing process in a furnace is a critical heat treatment method that transforms the properties of materials, making them more suitable for various industrial applications. By carefully controlling the heating and cooling processes, annealing furnaces play a vital role in achieving the desired material characteristics.
Summary Table:
Aspect | Details |
---|---|
Purpose | Improves ductility, reduces internal stresses, enhances machinability. |
Stages | Recovery, recrystallization, grain growth. |
Furnace Role | Precise temperature control, uniform heating, controlled cooling. |
Applications | Metalworking, electronics, manufacturing. |
Benefits | Enhanced workability, improved performance, stress relief. |
Discover how annealing can optimize your materials—contact our experts today for tailored solutions!