Electrodeposition is a versatile and precise method used to deposit thin films or coatings of materials onto a substrate by passing an electric current through an electrolyte. This technique is widely applied in industries such as electronics, energy storage, and renewable energy due to its ability to produce uniform, robust, and high-quality films. Key applications include the production of nanostructured films for batteries, fuel cells, solar cells, and magnetic read heads. The method's ability to control deposition at the atomic level makes it invaluable for creating materials with enhanced electrical, mechanical, and surface properties.
Key Points Explained:
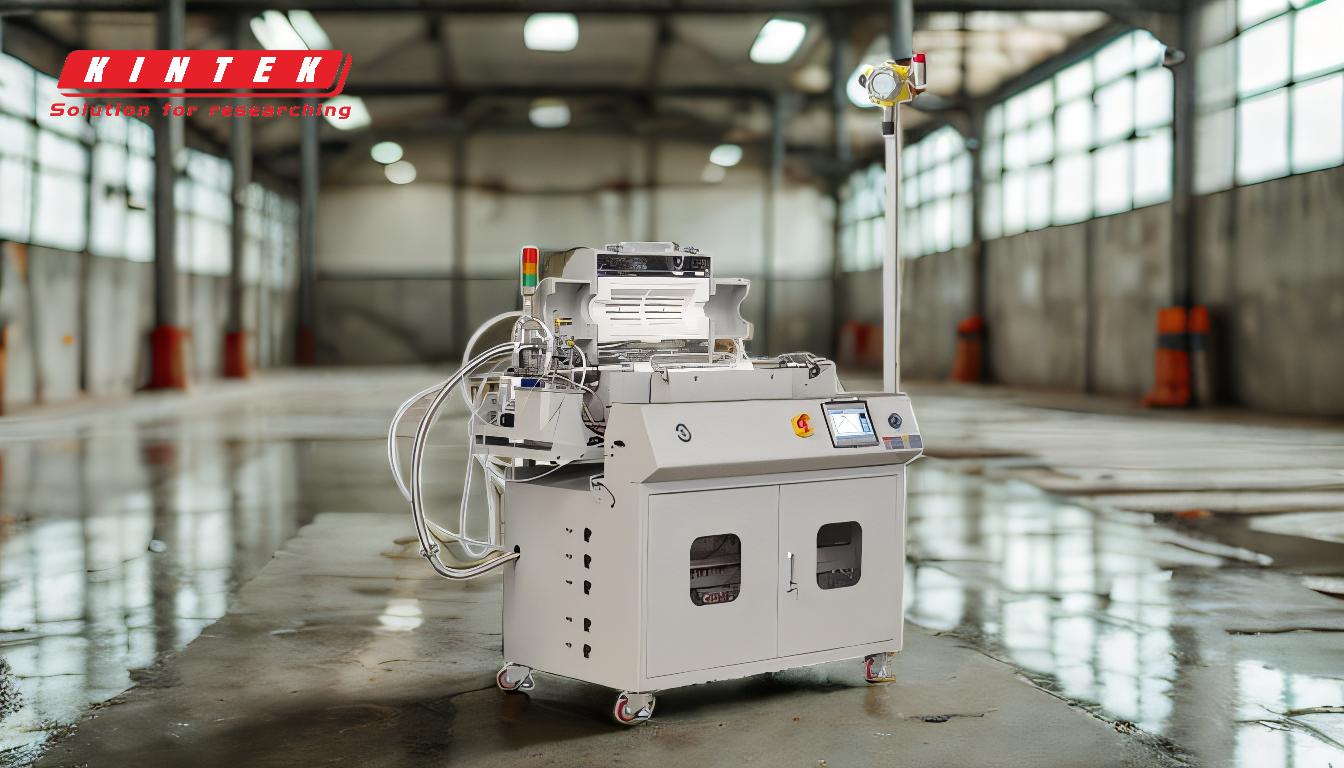
-
Fundamentals of Electrodeposition:
- Electrodeposition involves passing an electric current through two electrodes immersed in an electrolyte. This causes ions from the electrolyte to be reduced and deposited onto the surface of one electrode (the substrate).
- By carefully controlling parameters such as current density, temperature, and electrolyte composition, it is possible to achieve precise deposition, even at the atomic level.
-
Production of Nanostructured Films:
- Electrodeposition is particularly effective for creating nanostructured films of materials like copper, platinum, nickel, and gold.
- These films are mechanically robust, highly flat, and uniform, making them ideal for applications requiring precise surface properties.
- The larger surface area of nanostructured films enhances their electrical properties, which is beneficial for electronic and energy-related applications.
-
Applications in Energy Storage and Conversion:
- Batteries: Electrodeposition is used to create thin films for electrodes in batteries, improving their efficiency and capacity.
- Fuel Cells: The method is employed to produce catalyst layers in fuel cells, enhancing their performance and durability.
- Solar Cells: Electrodeposited films are used in solar cells to improve light absorption and charge carrier separation, increasing energy conversion efficiency.
-
Applications in Electronics:
- Magnetic Read Heads: Electrodeposition is used to fabricate magnetic read heads in hard drives, ensuring high precision and reliability.
- Semiconductors: The technique is applied in the production of semiconductor devices, where uniform and high-quality films are essential for optimal performance.
-
Advantages of Electrodeposition:
- Precision and Control: The ability to deposit materials at the atomic level allows for the creation of highly specialized and functional films.
- Cost-Effectiveness: Electrodeposition is a relatively low-cost method compared to other thin-film deposition techniques.
- Scalability: The process can be easily scaled up for industrial production, making it suitable for large-scale manufacturing.
-
Future Prospects:
- Ongoing research is exploring new materials and applications for electrodeposition, such as in flexible electronics, wearable devices, and advanced energy storage systems.
- The development of environmentally friendly electrolytes and processes is also a focus, aiming to reduce the environmental impact of electrodeposition.
In summary, electrodeposition is a critical technique with broad applications in modern technology, particularly in energy storage, electronics, and renewable energy. Its ability to produce high-quality, nanostructured films with precise control makes it indispensable for advancing these fields.
Summary Table:
Key Aspect | Description |
---|---|
Fundamentals | Uses electric current to deposit ions onto a substrate from an electrolyte. |
Nanostructured Films | Produces robust, flat, and uniform films for enhanced electrical properties. |
Energy Applications | Used in batteries, fuel cells, and solar cells for improved performance. |
Electronics Applications | Fabricates magnetic read heads and semiconductor devices with high precision. |
Advantages | Precise, cost-effective, and scalable for industrial production. |
Future Prospects | Research focuses on flexible electronics, wearable devices, and eco-friendly processes. |
Interested in leveraging electrodeposition for your projects? Contact us today to learn more!