A muffle furnace is a versatile and essential piece of equipment used in laboratories, industrial settings, and scientific research for high-temperature applications. Its primary function is to heat materials while isolating them from combustion byproducts, ensuring contamination-free processing. This makes it suitable for a wide range of applications, including material testing, quality control, chemical analysis, and pretreatment of medical samples. Its design features, such as rapid heating and cooling, temperature uniformity, and corrosion resistance, make it highly efficient and durable. Below, we explore the key applications and advantages of a muffle furnace in detail.
Key Points Explained:
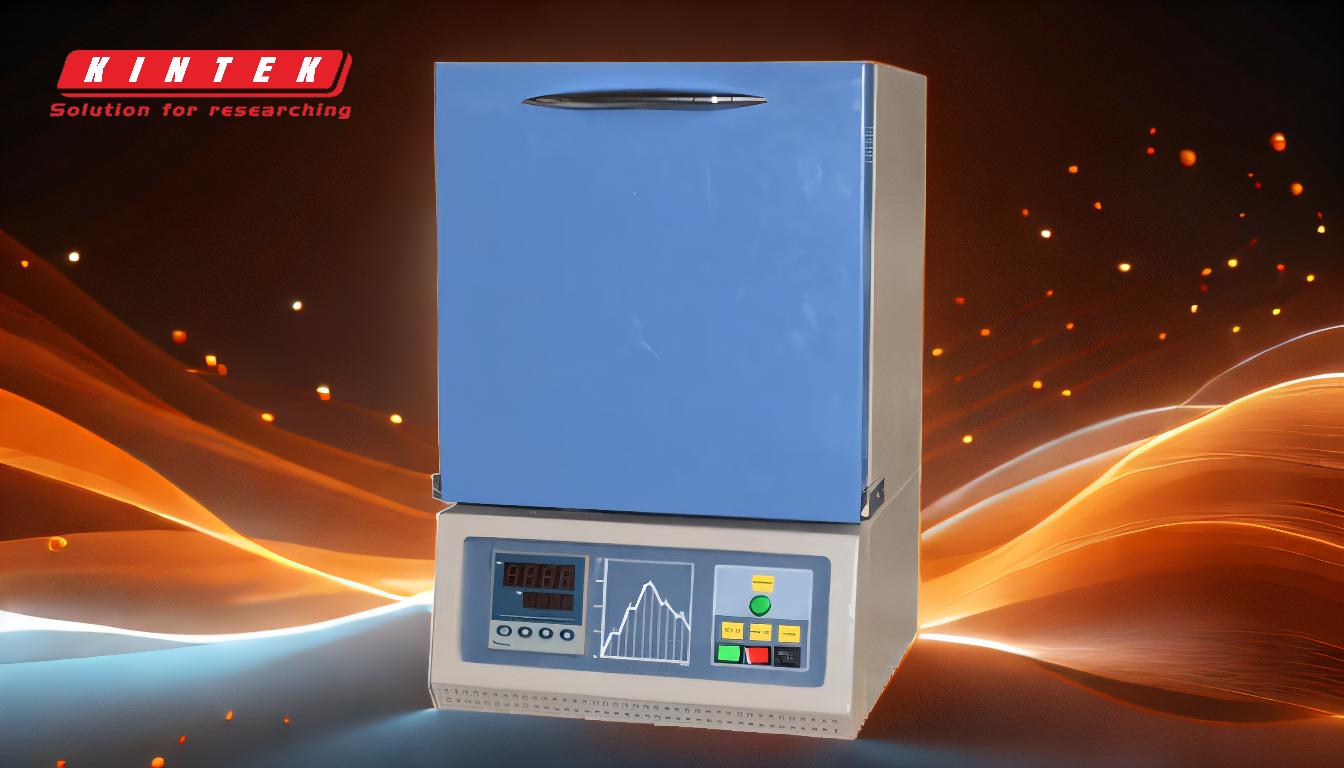
-
High-Temperature Material Testing and Analysis
- Muffle furnaces are widely used for determining the non-combustible and non-volatile content of materials, such as ash content in coal or organic compounds.
- They are essential for identifying the chemical properties of materials like ceramics, glass, and enamel coatings at elevated temperatures.
- Applications include ash melting point analysis, alkali fusion of refractory metals, and flameless ashing of filter paper.
-
Quality Control and Industrial Applications
- In industries, muffle furnaces are used for quality control processes, such as testing the durability and performance of materials under high temperatures.
- They are employed in the production of metals like low-carbon steel, stainless steel, and copper, ensuring uniform heating and consistent results.
- The furnace's ability to isolate materials from combustion byproducts makes it ideal for processes like brazing and sintering.
-
Chemical and Environmental Analysis
- Muffle furnaces play a critical role in chemical analysis, including the decomposition of organic materials and the expulsion of volatile components from inorganic matter.
- They are used in water quality analysis and the pretreatment of medical samples, ensuring accurate and contamination-free results.
- Applications also extend to nuclear fuel disposal and the analysis of coking products and chemical raw materials.
-
Research and Development
- In scientific research, muffle furnaces are used for materials research, such as studying the behavior of materials under extreme temperatures.
- They are essential for high-temperature experiments, including the synthesis of new materials and the testing of thermal properties.
-
Design and Operational Advantages
- Muffle furnaces feature a simple yet robust structure, with high-temperature resistance, oxidation resistance, and corrosion resistance.
- Their step-type assembling structure and integral door design ensure heat retention and prevent hearth collapse.
- Modern electric muffle furnaces use high-temperature heating elements, offering better temperature control, uniformity, and energy efficiency.
-
Isolation from Combustion Byproducts
- The independent combustion and heating chambers in a muffle furnace prevent contamination of the heated material by combustion byproducts.
- This feature is particularly important for processes requiring high purity, such as drug inspections and chemical analysis.
-
Rapid Heating and Cooling Capabilities
- Muffle furnaces are designed for rapid high-temperature heating, recovery, and cooling, making them highly efficient for time-sensitive applications.
- The use of insulated materials minimizes heat loss, ensuring energy efficiency and consistent performance.
In summary, the muffle furnace is a critical tool in various fields due to its ability to provide contamination-free, high-temperature processing. Its applications range from material testing and quality control to chemical analysis and scientific research, supported by its durable design, operational efficiency, and advanced temperature control features.
Summary Table:
Application | Key Uses |
---|---|
High-Temperature Material Testing | Ash content analysis, alkali fusion, flameless ashing, chemical property testing |
Quality Control | Durability testing, metal production, brazing, sintering |
Chemical Analysis | Organic material decomposition, water quality analysis, medical sample prep |
Research & Development | Materials research, high-temperature experiments, thermal property testing |
Design Advantages | Contamination-free processing, rapid heating/cooling, energy efficiency |
Unlock the full potential of a muffle furnace for your applications—contact us today to learn more!