The atmosphere of a sintering furnace plays a critical role in determining the quality and properties of the sintered products. It is carefully controlled to prevent oxidation, decarburization, and other undesirable reactions, while also ensuring proper sintering conditions. Common atmospheres include nitrogen-hydrogen mixtures, pure hydrogen, vacuum, dissociated ammonia, endothermic gas, and inert gases like argon or nitrogen. The choice of atmosphere depends on the material being sintered and the desired outcomes, such as maintaining a neutral, reducing, or protective environment. These atmospheres are regulated across different zones of the furnace to achieve specific sintering vectors and ensure optimal results.
Key Points Explained:
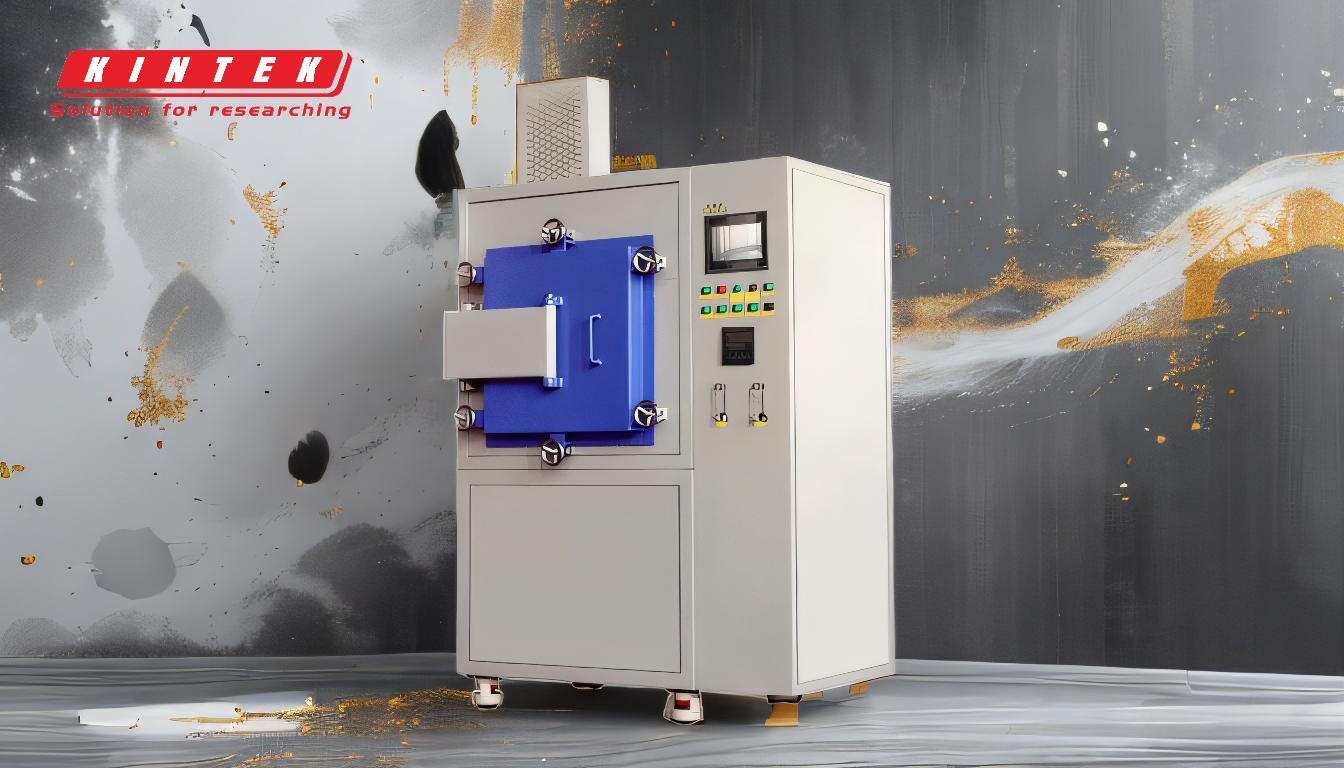
-
Purpose of Controlled Atmospheres in Sintering Furnaces:
- The atmosphere in a sintering furnace is crucial for preventing oxidation, decarburization, and other chemical reactions that could degrade the quality of the sintered product.
- It ensures the proper sintering of powdered metals or other materials by maintaining the required thermal and chemical conditions.
-
Types of Atmospheres:
- Inert/Protective Atmospheres: These include nitrogen, argon, or nitrogen-hydrogen mixtures. They are used to prevent reactions with the material being sintered, particularly for metals that are sensitive to oxidation.
- Hydrogen Atmosphere: Pure hydrogen is often used for its reducing properties, which help in removing oxides from the surface of the material.
- Vacuum: A vacuum environment eliminates the presence of reactive gases, making it ideal for sintering materials that are highly reactive with oxygen or nitrogen.
- Dissociated Ammonia: This atmosphere provides a mix of hydrogen and nitrogen, offering both reducing and protective properties.
- Endothermic Gas: This is a mixture of hydrogen, carbon monoxide, and nitrogen, commonly used in sintering processes to prevent oxidation and decarburization.
-
Atmosphere Selection Based on Material and Process Requirements:
- The choice of atmosphere depends on the material being sintered. For example:
- Oxidizing Atmospheres: Used for materials that require oxidation during sintering.
- Neutral Atmospheres: Suitable for materials that should not react with the atmosphere.
- Reducing Atmospheres: Ideal for materials that need oxide reduction, such as metals.
- Alkaline or Acidic Atmospheres: Used for specialized sintering processes where specific chemical reactions are required.
- The choice of atmosphere depends on the material being sintered. For example:
-
Regulation of Atmosphere in Different Zones:
- Sintering furnaces often have multiple zones, each requiring a specific atmosphere to achieve the desired sintering vectors. For example:
- A reducing atmosphere might be used in the initial heating zone to remove oxides.
- A neutral or inert atmosphere might be maintained in the sintering zone to prevent further reactions.
- A cooling zone might use a protective atmosphere to ensure the material does not oxidize as it cools.
- Sintering furnaces often have multiple zones, each requiring a specific atmosphere to achieve the desired sintering vectors. For example:
-
Operational Modes:
- Sintering furnaces can operate in various modes, including:
- Air: Used for materials that are not sensitive to oxidation.
- Vacuum: Used for highly reactive materials.
- Partial Vacuum or Positive Pressure: Used to control the flow of gases and maintain a stable atmosphere.
- Sintering furnaces can operate in various modes, including:
-
Protective Gases:
- Gases like hydrogen, nitrogen, and carbon monoxide are commonly used to maintain atmospheric pressure and ensure proper sintering conditions. These gases help in controlling the thermal and chemical environment within the furnace.
-
Impact on Sintered Product Quality:
- The choice and control of the atmosphere directly impact the density, strength, and microstructure of the sintered product. Proper atmosphere control ensures uniformity and consistency in the final product.
By carefully selecting and regulating the furnace atmosphere, manufacturers can achieve the desired properties in their sintered products, making it a critical aspect of the sintering process.
Summary Table:
Key Aspect | Details |
---|---|
Purpose of Controlled Atmosphere | Prevents oxidation, decarburization, and ensures proper sintering conditions. |
Types of Atmospheres | Inert (N₂, Ar), Hydrogen, Vacuum, Dissociated Ammonia, Endothermic Gas. |
Atmosphere Selection | Based on material (e.g., oxidizing, neutral, reducing, or protective). |
Regulation in Zones | Different zones require specific atmospheres for optimal sintering vectors. |
Operational Modes | Air, Vacuum, Partial Vacuum, or Positive Pressure. |
Impact on Product Quality | Controls density, strength, and microstructure of sintered products. |
Need help selecting the right sintering furnace atmosphere? Contact our experts today for tailored solutions!