Sintering is a critical process in materials science where atomic diffusion plays a central role in transforming powdered materials into solid, dense structures. The atomic mechanism of sintering involves the movement of atoms across particle boundaries, driven by heat and pressure, which leads to the fusion of particles and the reduction of porosity. This process occurs below the material's melting point, ensuring that the particles bond without fully liquefying. Sintering is widely used in industries to produce ceramics, metals, and plastics, and it involves several stages, including powder preparation, compression, heating, and solidification. Understanding the atomic mechanisms behind sintering is essential for optimizing material properties and manufacturing processes.
Key Points Explained:
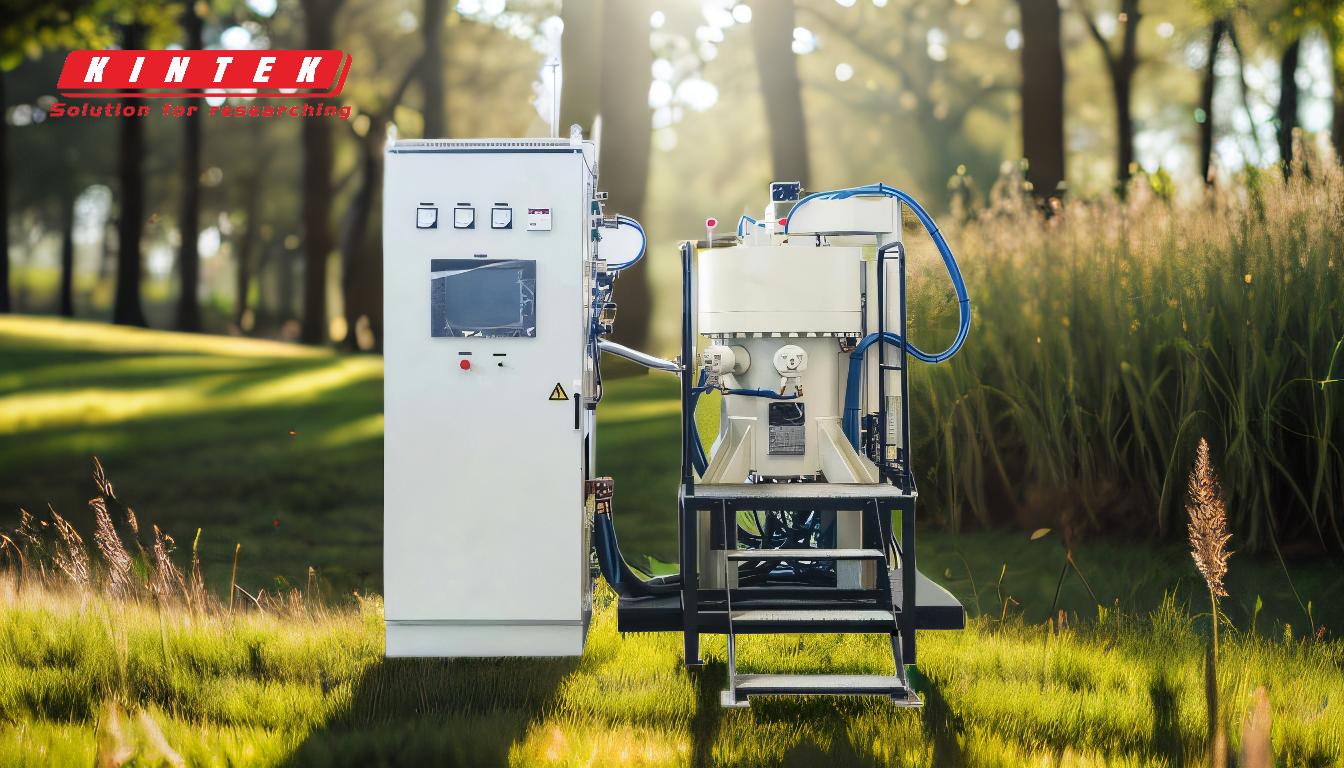
-
Atomic Diffusion in Sintering:
- The core mechanism of sintering is the diffusion of atoms across the surfaces of powder particles. This diffusion is driven by thermal energy and pressure, which cause atoms to migrate from areas of high energy (such as particle surfaces) to areas of low energy (such as grain boundaries or pores).
- As atoms move, they form bonds between adjacent particles, leading to the formation of "necks" or bridges between them. This initial stage reduces the surface area and energy of the system, stabilizing the material.
-
Stages of Sintering:
- Initial Stage: Atoms begin to migrate, forming necks between particles. This stage is characterized by the reduction of surface area and the onset of particle bonding.
- Intermediate Stage: As sintering progresses, the necks grow, and the porosity of the material decreases. The particles start to densify, and the material begins to take on a more solid form.
- Final Stage: In the last stage, small pores are eliminated, and the material reaches its maximum density. The atomic diffusion continues until the material becomes a unified, low-porosity mass.
-
Role of Heat and Pressure:
- Heat provides the energy necessary for atomic diffusion. By heating the material to a temperature below its melting point, atoms gain enough energy to move and bond without causing the material to melt.
- Pressure aids in the compaction of the powder, reducing the distance between particles and facilitating atomic diffusion. In some cases, pressure is applied during sintering to accelerate the process and improve material density.
-
Liquid Phase Sintering (LPS):
- In some sintering processes, a liquid phase is introduced to enhance atomic diffusion. This liquid phase, often a lower-melting-point material, wets the solid particles and promotes faster bonding.
- LPS is particularly useful for materials that are difficult to sinter using solid-state diffusion alone, as it allows for faster densification and improved material properties.
-
Applications and Importance:
- Sintering is used in the production of a wide range of materials, including ceramics, metals, and plastics. It is essential for creating components with high strength, durability, and precision.
- The atomic mechanisms of sintering are crucial for understanding how to optimize material properties, such as density, porosity, and mechanical strength, for specific applications.
-
Comparison with Graphitization:
- While sintering involves the bonding of particles through atomic diffusion, graphitization is a different process where carbon atoms are removed one at a time from a diamond surface. This process breaks carbon-carbon bonds and transforms the material's structure.
- Understanding the differences between these processes highlights the unique atomic mechanisms involved in sintering and its role in material consolidation.
By breaking down the atomic mechanisms of sintering, we gain insight into how heat, pressure, and atomic diffusion work together to transform powdered materials into solid, functional components. This knowledge is essential for advancing materials science and improving manufacturing techniques across various industries.
Summary Table:
Key Aspect | Description |
---|---|
Atomic Diffusion | Atoms migrate across particle surfaces, driven by heat and pressure. |
Stages of Sintering | Initial (neck formation), Intermediate (densification), Final (pore elimination). |
Role of Heat and Pressure | Heat enables atomic movement; pressure compacts particles for faster bonding. |
Liquid Phase Sintering | Introduces a liquid phase to enhance diffusion and bonding in challenging materials. |
Applications | Used in ceramics, metals, and plastics to create strong, durable components. |
Comparison with Graphitization | Sintering bonds particles; graphitization removes carbon atoms from diamond. |
Want to optimize your sintering process? Contact our experts today for tailored solutions!