The best heat treatment for steel depends on the desired properties and the specific application of the steel. Heat treatment processes such as annealing, quenching, tempering, normalizing, case hardening, and martensitic transformation are used to modify the mechanical properties of steel, including strength, hardness, ductility, toughness, wear resistance, and elasticity. Each method has its unique benefits and is chosen based on the intended use of the steel. For example, annealing improves ductility and reduces hardness, while quenching increases hardness and strength. Tempering is often used after quenching to reduce brittleness. The optimal heat treatment process is determined by balancing the required properties for the steel's application.
Key Points Explained:
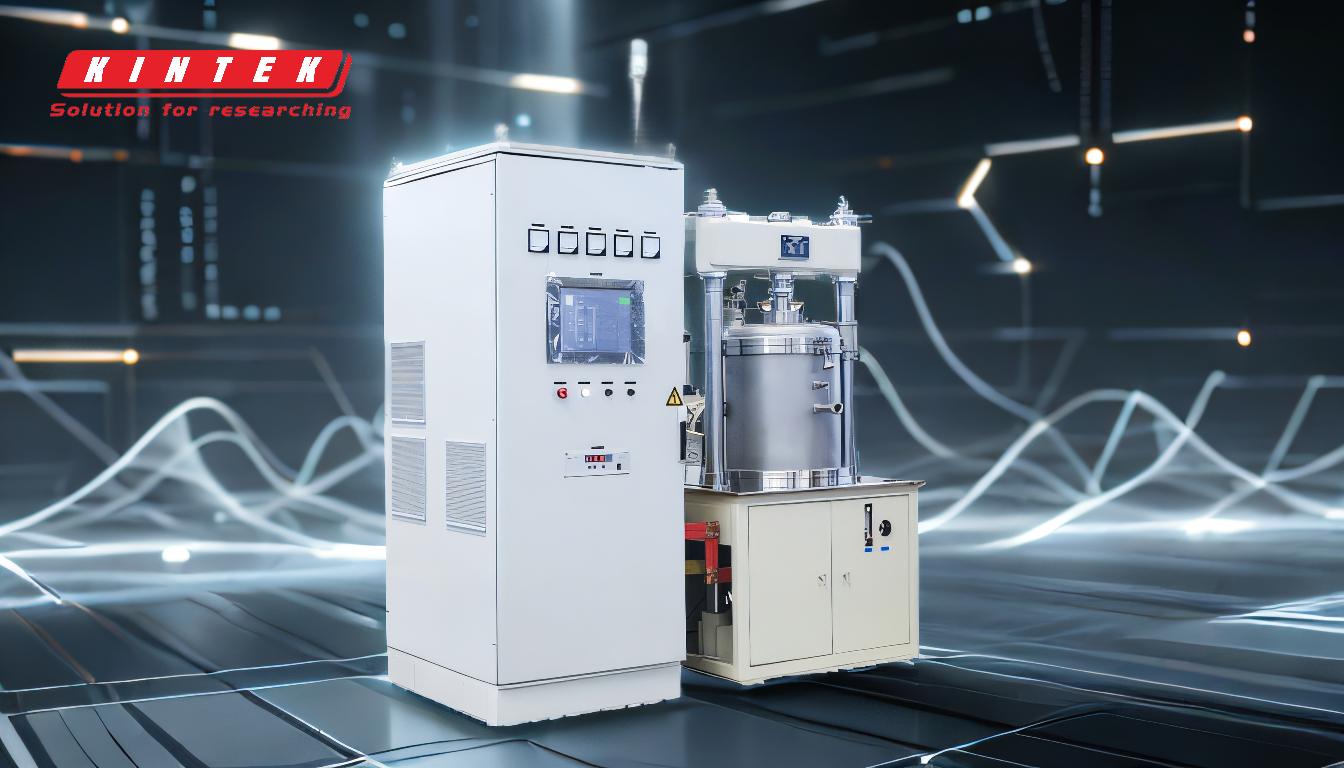
-
Understanding Heat Treatment Goals:
- Heat treatment is used to alter the mechanical properties of steel, such as hardness, strength, toughness, ductility, and wear resistance.
- The choice of heat treatment depends on the desired outcome for the steel's application. For instance, tools requiring high hardness might undergo quenching, while structural components needing toughness might be tempered.
-
Common Heat Treatment Methods:
- Annealing: This process involves heating steel to a specific temperature and then slowly cooling it. Annealing improves ductility, reduces hardness, and relieves internal stresses, making the steel easier to machine or form.
- Quenching: Steel is heated to a high temperature and then rapidly cooled, typically in water, oil, or air. Quenching increases hardness and strength but can make the steel brittle. It is often followed by tempering.
- Tempering: After quenching, tempering involves reheating the steel to a lower temperature and then cooling it. This process reduces brittleness while maintaining hardness and strength, improving toughness.
- Normalizing: Similar to annealing, normalizing involves heating steel and then cooling it in air. This process refines the grain structure, improves mechanical properties, and enhances uniformity.
- Case Hardening: This method hardens the surface of the steel while keeping the core relatively soft. It is ideal for components requiring a hard, wear-resistant surface and a tough interior, such as gears.
- Martensitic Transformation: This involves rapidly cooling steel to form martensite, a hard and brittle microstructure. It is often used in conjunction with quenching and tempering to achieve specific mechanical properties.
-
Selecting the Best Heat Treatment:
- The best heat treatment for steel depends on the application. For example:
- High-Strength Tools: Quenching followed by tempering is ideal to achieve high hardness and strength with reduced brittleness.
- Structural Components: Normalizing or annealing may be preferred to enhance toughness and ductility.
- Wear-Resistant Parts: Case hardening is suitable for applications requiring a hard surface and a tough core.
- The composition of the steel (e.g., carbon content) also influences the choice of heat treatment. High-carbon steels respond well to quenching and tempering, while low-carbon steels may require case hardening.
- The best heat treatment for steel depends on the application. For example:
-
Trade-Offs and Considerations:
- Heat treatment involves trade-offs between properties. For example, increasing hardness through quenching may reduce ductility and toughness.
- The cooling rate during heat treatment is critical. Rapid cooling (quenching) increases hardness but can introduce internal stresses, while slow cooling (annealing) improves ductility but reduces hardness.
- Post-treatment processes, such as tempering, are often necessary to balance properties and reduce brittleness.
-
Practical Applications:
- Automotive Industry: Heat-treated steel is used in engine components, gears, and suspension systems, where a combination of strength, hardness, and toughness is required.
- Tool Manufacturing: Tools such as drills, saws, and dies undergo quenching and tempering to achieve high hardness and wear resistance.
- Construction: Structural steel is often normalized or annealed to improve toughness and durability.
In conclusion, the best heat treatment for steel is determined by the specific requirements of its application. By understanding the properties each heat treatment method imparts, such as hardness, strength, and toughness, and considering the trade-offs involved, the optimal process can be selected to meet the desired performance characteristics.
Summary Table:
Heat Treatment Method | Key Benefits | Common Applications |
---|---|---|
Annealing | Improves ductility, reduces hardness, relieves internal stresses | Machining, forming |
Quenching | Increases hardness and strength, but may cause brittleness | High-strength tools |
Tempering | Reduces brittleness, maintains hardness and strength | Tools, structural components |
Normalizing | Refines grain structure, improves uniformity | Structural steel |
Case Hardening | Hardens surface, keeps core tough | Gears, wear-resistant parts |
Martensitic Transformation | Forms hard, brittle microstructure | High-performance tools |
Need help selecting the right heat treatment for your steel? Contact our experts today for tailored solutions!